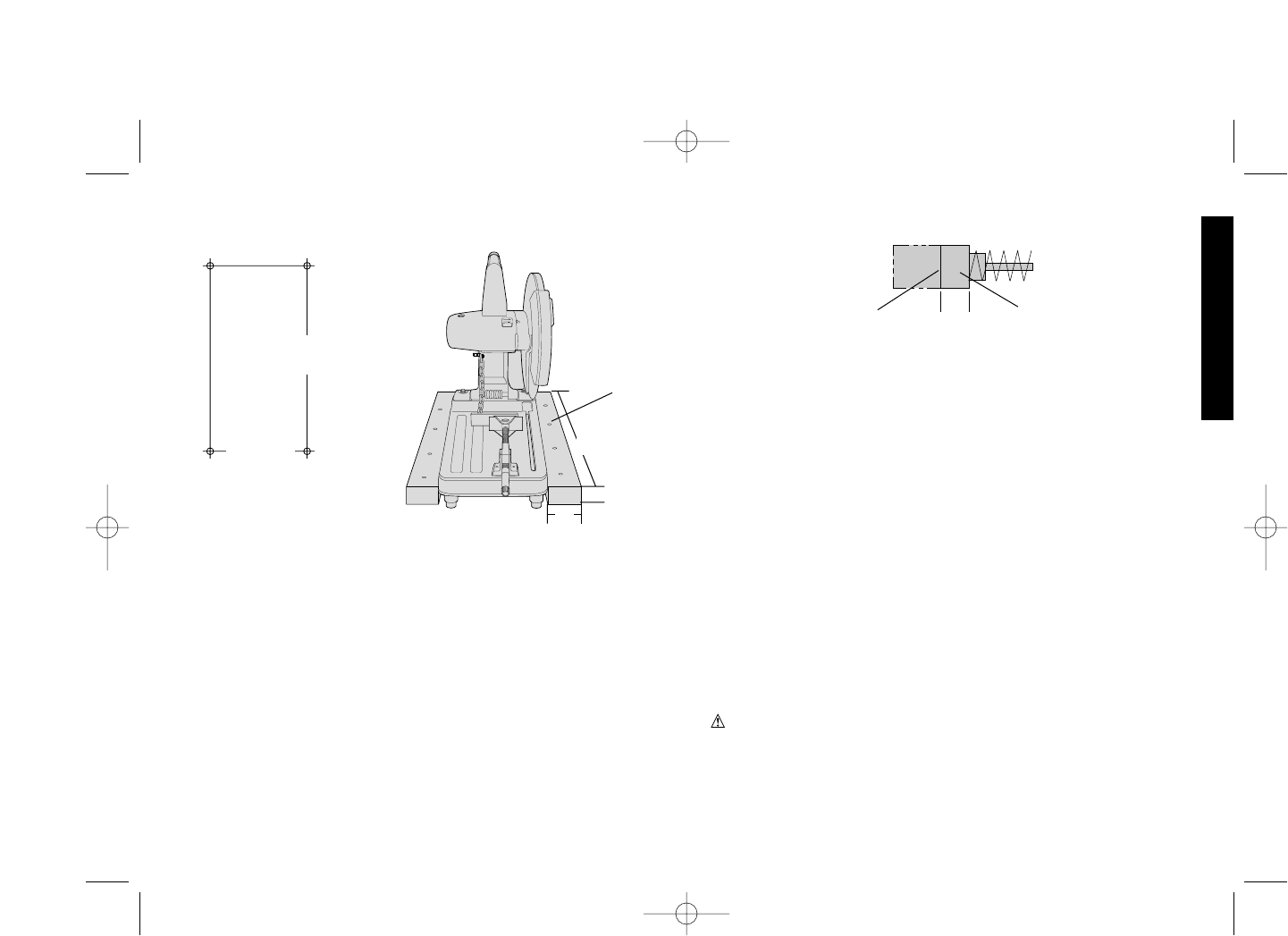
6
English
Motor Brush Inspection and
Replacement
Be sure tool is unplugged before inspecting brushes. Brushes should
be regularly inspected for wear. To inspect brushes, unscrew the
two end cap screws and remove end cap. To remove each brush, first
unplug the shunt wire terminal connection. Then carefully back the
brush spring out of the brush box and remove brush. Brushes should
slide freely in brush box. If brushes are worn down to .3” they should
be replaced (see Figure 9). To reinstall each brush carefully back
the spring out of the brush box, insert the brush and return the spring
making sure it is pressing on the brush and not touching the brush
box. Then replace the end cap and two screws.
Operation Tips for More Accurate Cuts
• Allow the wheel to do the cutting. Excessive force will cause the
wheel to glaze reducing cutting efficiency and/or to deflect causing
inaccurate cuts.
• Adjust fence angle. (Figure 3)
• Make sure material is laying flat across base.
• Properly clamp material to avoid movement and vibration.
Cleaning
Blowing dust and grit out of the main housing by means of an air hose
is recommended and may be done as often as dirt is seen collecting
in and around the air vents.
Accessories
Recommended accessories for use with your tool are available at
extra cost from your local dealer or authorized service center. If you
need assistance in locating any accessory for your tool, contact:
D
EWALT Industrial Tool Co., 701 East Joppa Road, Baltimore, MD
21286
CAUTION: The use of any other accessory not recommended
for use with this tool could be hazardous.
Important
To assure product SAFETY and RELIABILITY, repairs, maintenance
and adjustment should be performed by authorized service centers
or other qualified service organizations, always using identical
FIG. 7
FIG. 8
16-3/8"
(416 mm)
8-1/2"
(216 mm)
ST
O
P
PE
R
PIN
20"
2"-3"
NAIL
4"
FIG. 9
0.3"
7.62 mm
BRUSH
WEAR LINE
383823-01/DW870 5/3/02 1:33 PM Page 9