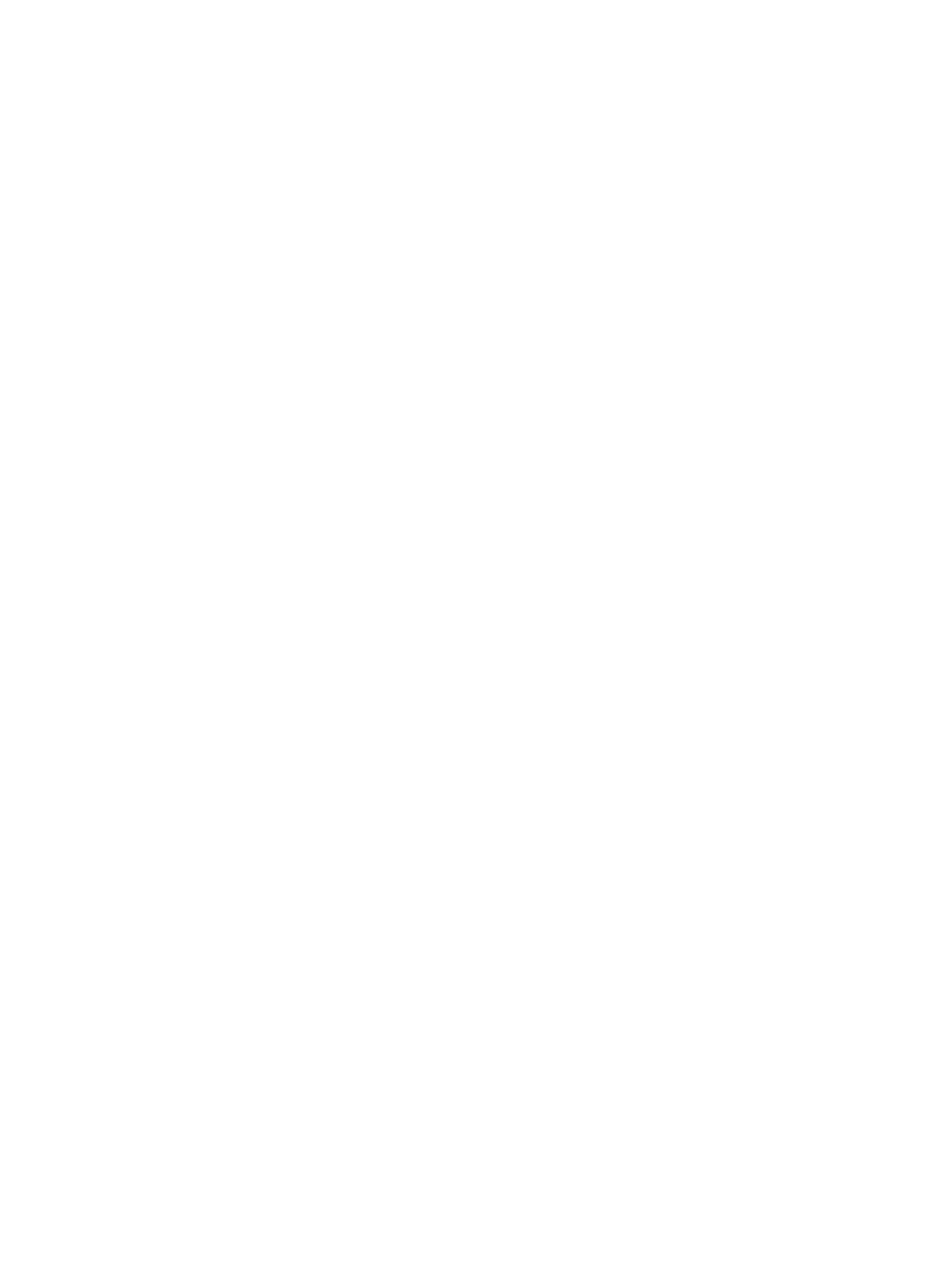
H.E.R.O. INDUSTRIES 300S / 300SL LEGEND Owner’s Manual
18
TROUBLESHOOTING
SITUATION
POSSIBLE CAUSE (REMEDY)
ELECTRIC MOTOR WON'T START/RUN
1. Unit unplugged or building circuit fuse is blown. (check, replace or reset fuse)
2. Pump under pressure. (reduce pressure setting by turning pressure control knob counter-clockwise,
trigger gun to relieve pressure).
3. Too light or too long of extension cord. (replace with correct cord. If distance greater than 100 feet,
obtain and install extra length of H.E.R.O. airless spray hose).
4. Unit's thermal overload switch has opened. (determine and correct cause of overheating).
ELECTRIC MOTOR STALLS/QUITS
1. See "Electric Motor Won't Start/Run
2. Drive belt is loose. (tighten drive belts by evenly turning belt tension bolts on either side of motor
clockwise. Loose belts generally emit loud squealing noises).
3. Unit primes, builds pressure, but pump “seizes” or “stops” when gun is triggered. ( loose belts, tighten).
TOTAL LOSS OF PRESSURE, DIAPHRAGM MOVEMENT CANNOT BE STOPPED OR
ALTERED. (SEE "DIAPHRAGM TEST")
1. Paint too thick. (thin paint according to manufacturer's recommendations).
2. Intake ball (ref# 13) worn or jammed opened/closed. (remove intake endcap (ref# 11) and cage (ref# 14).
Inspect intake ball, (ref# 13), to ensure it is free, round, and has no nicks or cuts. Inspect ball cage and
cage spring for damage or wear. Inspect for foreign material jamming ball. Replace parts as needed).
3. Intake seat loose/bypassing. (remove intake endcap, (ref# 11) and ball cage, (ref# 14). Check seat to
ensure it is tightly secured in endcap block. Remove intake elbow (ref# 8) and inspect block from the
inbound direction. Look for any washout or erosion. Removal of seat may be required for positive
identification of washout or erosion.
4. Outgo valve ball (ref# 26) worn or jammed. (remove outgo valve, (ref# 22). Invert valve and unthread
outgo valve upper, (ref# 29), from outgo lower, (ref# 23). Remove crush washer, (ref# 24), outgo seat,
(ref# 25), outgo ball, (ref# 26), outgo cage, (ref# 27), outgo spring, (ref# 28), from outgo upper tunnel.
Inspect outgo ball to ensure that it is round and free of nicks or cuts. Inspect for foreign material jamming
ball. Inspect ball and cage for wear. Replace parts as needed).
5. Outgo valve (ref# 22) incorrectly assembled. (disassemble and reassemble outgo valve, closely following
detailed instructions on page 24).
TOTAL LOSS OF PRESSURE, DIAPHRAGM HAS NO MOVEMENT OR MOVEMENT CAN BE
STOPPED. (SEE "DIAPHRAGM TEST")
1. Hydraulic intake valve (ref# 62) defective. (remove hydraulic feed line, (ref# 63), from hydraulic
intake valve. Plug hydraulic feed line so hydraulic fluid does not drain. Remove hydraulic intake valve
from elbow, (ref# 61). Check hydraulic intake valve to ensure that it flows in one way only, into the
cylinder. Replace if necessary. NOTE; Item cannot be repaired ).