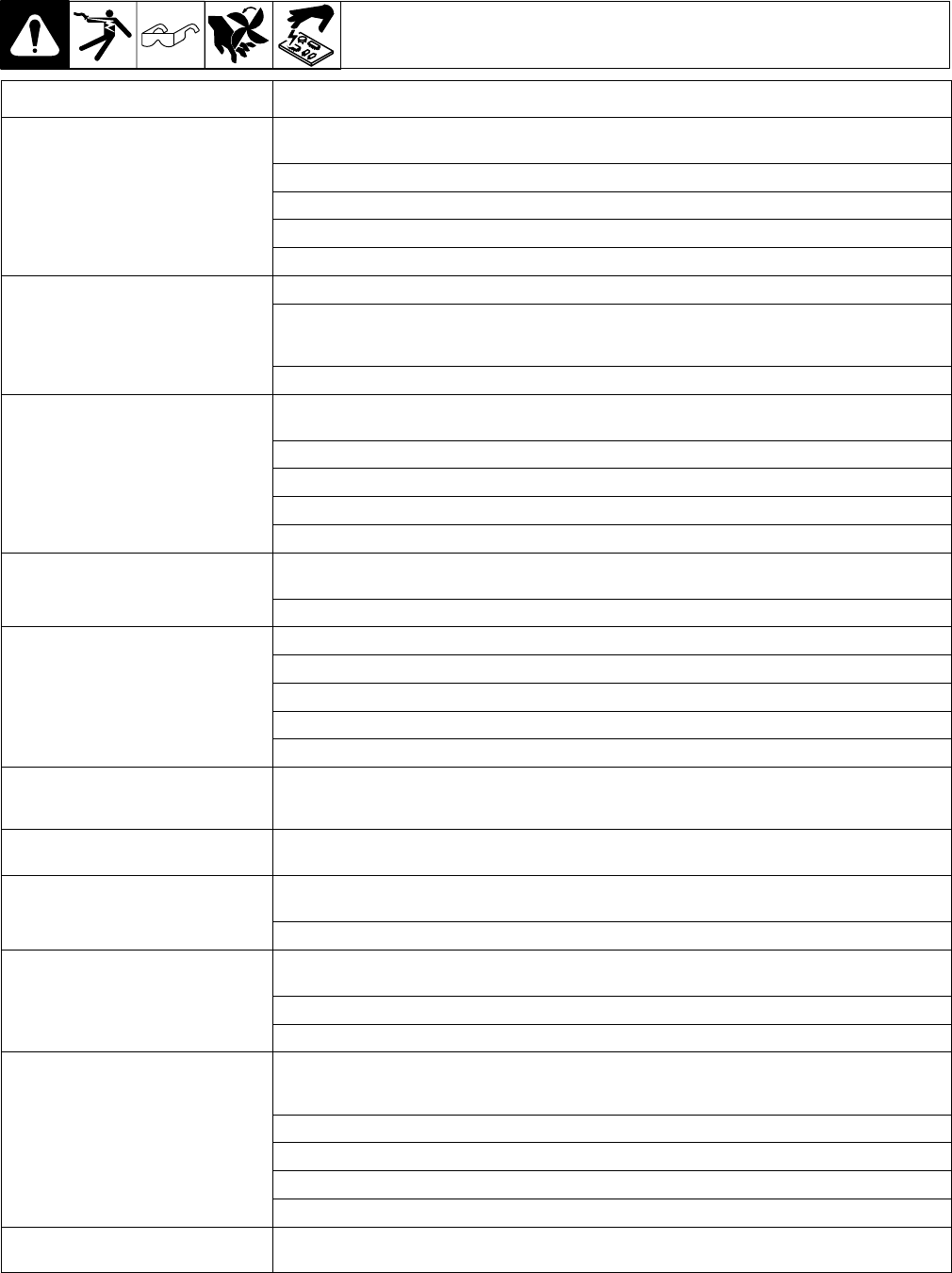
OM-277 Page 24
5-3. Troubleshooting
Trouble Remedy
No weld output; unit completely inop-
erative; pilot light PL1 off.
Place line disconnect device in On position (see Section 3-13).
Check for open line fuse(s), and replace if open (see Section 3-13).
Check for proper input power connections (see Section 3-13).
Check for proper jumper link position (see Section 3-12).
Check fuse F1, and replace if necessary (see Section 5-2).
No weld output; pilot light PL1 on. Unit overheated. Allow unit to cool with fan On (see Section 3-2).
If using remote control, place Output (Contactor) switch in Remote 14 position, and connect remote
control (see Sections 3-9 and 3-10). If remote is not being used, place switch in On position (see
Section 4-2).
Check, repair, or replace remote control.
Limited weld output and low
open-circuit voltage.
Check position of Remote Amperage/Voltage Control switch (see Section 4-2).
Check for open line fuse(s), and replace if open (see Section 3-13).
Check for proper input power connections (see Section 3-13).
Check for proper jumper link position (see Section 3-12).
Clean and tighten all weld output connections.
Unit provides only maximum or mini-
mum weld output.
Have Factory Authorized Service Agent check control board PC1 and hall device HD1.
Check position of Remote Amperage/Voltage Control switch (see Section 4-2).
Erratic or improper weld output. Use proper size and type of weld cable (see Section 3-8).
Clean and tighten all weld connections.
Check wire feeder installation according to Owner’s Manual.
Check position of Process selector switch (see Section 4-2).
Have Factory Authorized Service Agent check control board PC1 and hall device HD1.
No 115 volts ac output at duplex recep-
tacle, Remote 14 receptacle, or termi-
nal strip 1T.
Reset circuit breaker CB1 (see Section 3-7).
No 24 volts ac output at Remote 14 re-
ceptacle or terminal strip 1T.
Reset circuit breaker CB2 (see Section 3-7).
Fan not operating. Note: fan only runs
when cooling is necessary.
Check for and remove anything blocking fan movement.
Have Factory Authorized Service Agent check fan motor.
Wandering arc; poor control of arc di-
rection.
Reduce gas flow rate.
Select proper size tungsten.
Properly prepare tungsten.
Tungsten electrode oxidizing and not
remaining bright after conclusion of
weld.
Shield weld zone from drafts.
Increase postflow time.
Check and tighten all gas fittings.
Properly prepare tungsten.
Check for water in torch, and repair torch if necessary. See torch Owner’s Manual.
Digital meter not working properly. Have Factory Authorized Service Agent check control board PC1 and connections, and replace if
necessary.