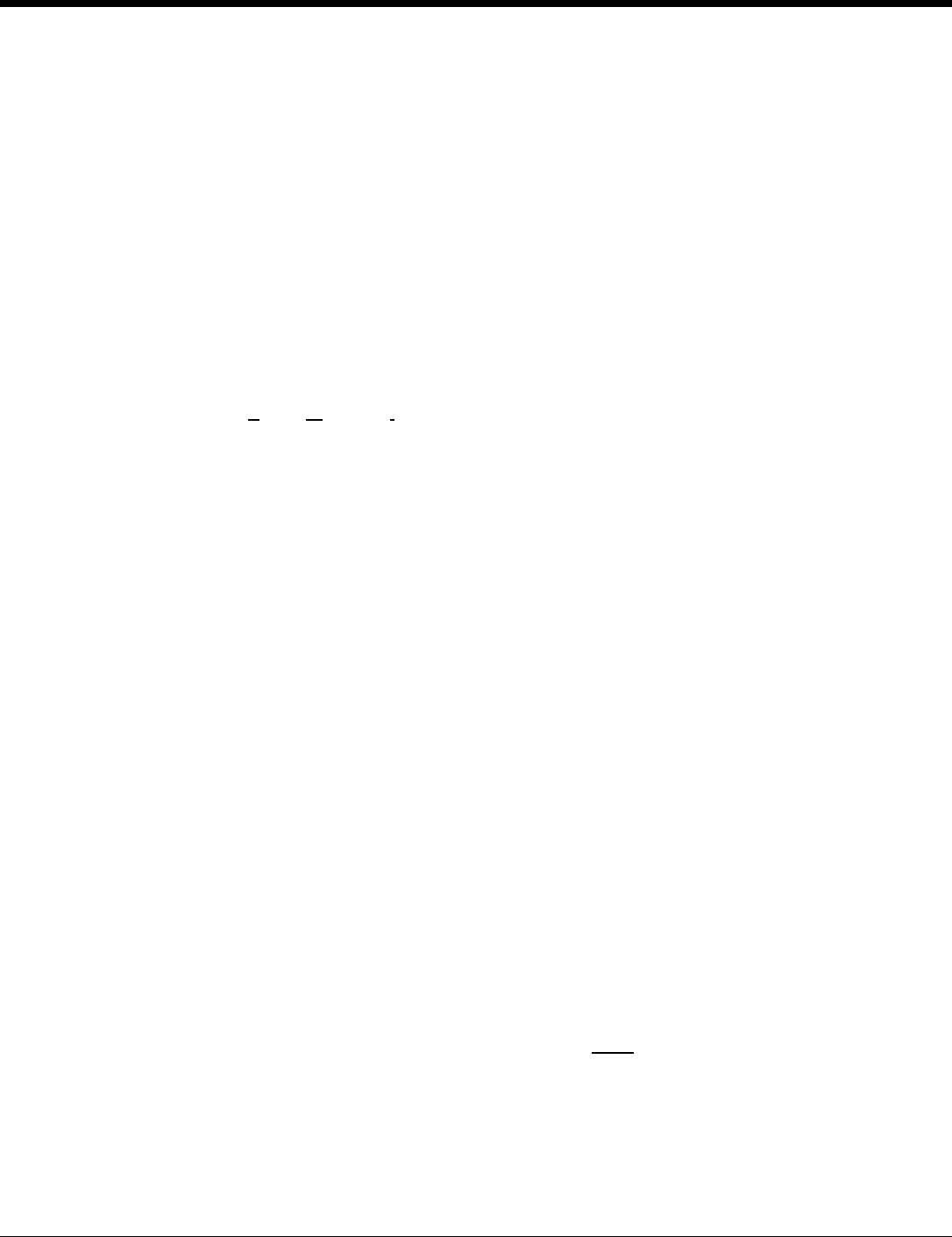
12
Flex Cables
Note: To ensure optimum engine stability, use the flex cables shipped with the scan engine.
The host flex cable is used to carry power and data signals between the engine and the host system. The flex
cable should allow for a minimal voltage drop and maintain a good ground connection between the host and
the engine. In terms of grounding and voltage drop, a shorter cable is better. The 10-POS flex cable used to
connect the engine to the host or the engine to the decode PCB must be equal to or less than 67.5 mm in
length. The 12-POS flex cable used to connect the decode PCB to the host must be equal to or less than 80
mm in length.
In addition to power, the flex cable also carries the digital signals required for communication. The cable
design is especially important in USB interface applications due to the relative high speed of the USB signals.
The impedance of the cable should match, or be as close as possible to the impedance of the USB driver
(approximately 45 ohms per trace).
The routing of the flex cables plays a critical role in the system design. The host flex cable should be routed
away from high frequency devices with frequencies that can couple onto the flex cable and cause potential
data corruption or unwanted e
lectromagnetic inference (EMI).
Thermal Considerations
The IS4800 laser scan engine series is qualified over the specified operational temperatures (0°C to 40°C) for
all operating modes. Ambient temperatures must not exceed this range in order to obtain optimal operation.
Operating the IS4800 in continuous mode for an extended period may produce considerable heating. This
mode should be limited and sufficient airflow should be provided whenever possible to minimize internal
heating. Excessive heating may potentially damage the IS4800 engine.
Printed Circuit Board (PCB) Component Clearance
Warning: When designing the IS4800 into the final product, eliminate all possible dangers of shorting
sensitive electronic components in the IS4800 engine. A short could enable the scan engine to
emit Class 3R radiation. Any CDRH filing will require a disclosure of the design ensuring a method
to mitigate a potential short.
Magnetic Sensitivity
The scan engine can be negatively affected by magnetic fields:
• Use only non-magnetic screws and locating pins.
• Do not mount the engine within 1.00" (25.4 mm) of any magnetic materials.
Airborne Contaminants and Foreign Materials
The scan engine has very sensitive miniature electrical and optical components that must be protected from
airborne contaminants and foreign materials. In order to prevent permanently damaging the scan engine and
voiding the limited warranty (on page 38), the scan engine enclosure
must
• Sealed to prevent infiltration by airborne contaminants and foreign materials such as dust, dirt, smoke,
and smog.
be:
• Sealed to protect against water, humidity and be non-condensing.
See page 26 - 27 for additional electrical specifications.
See page 29 - 31 for additional pinout information.