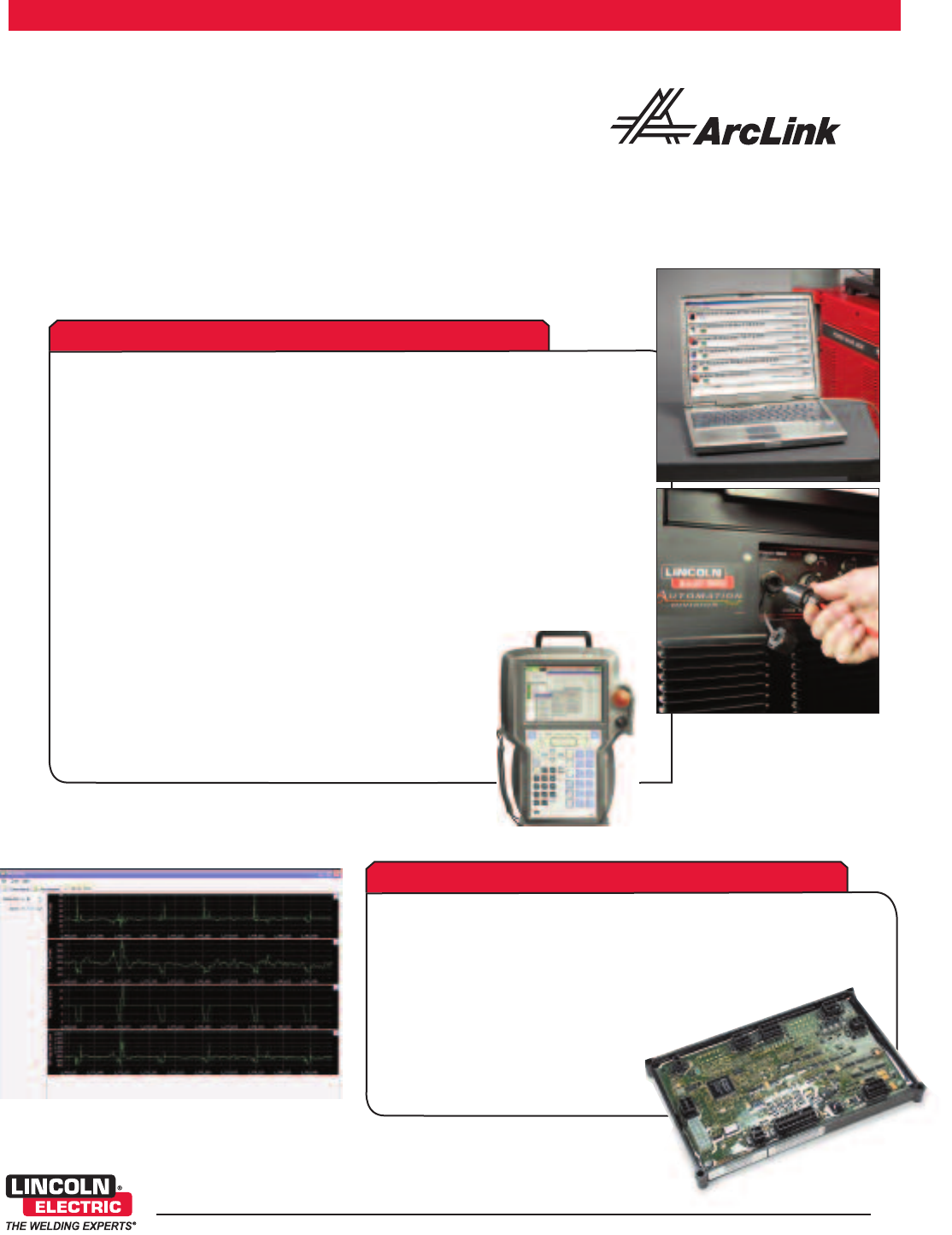
HIGH SPEED DIGITAL CONTROL TECHNOLOGY & FEATURES:
Lincoln Electric emerges as an industry leader with a distributed control architecture
design in the Power Wave
®
i400 system created with a flexible design that ensures
future expansion capabilities and features.
The state-of-the-art technology used in this system is designed with the highest
performance digital controls in the robotic power source marketplace:
• Over 5000 MIPS processing power
• 100 Mbps full duplex data transfer rate
• 32 Mbytes SDRAM memory
• More than 16 Mbytes FLASH Memory
Publication E4.20
www.lincolnelectric.com
[5]
DIGITAL COMMUNICATIONS TECHNOLOGY
®
The Lincoln Electric Company led the industry with the introduction of ArcLink
®
, the first digital
c
ommunications protocol for the arc welding industry introduced in 2002. ArcLink
®
i
s a protocol, or
means of communicating and sharing information between intelligent components for seamless, time-
critical data transfer in an arc welding system.
Continuing this leading position, Lincoln Electric has now introduced another industry first with
ArcLink
®
XT, which takes all of the same features and benefits of traditional ArcLink communication,
but eXtends this communication protocol on an Ethernet connection directly to the FANUC
®
Robotics
R30iA controller.
For more information see Nextweld
®
Document #NX-1.30
®
LINCOLN ELECTRIC AND FANUC
®
ROBOTICS ADVANTAGES:
ArcLink XT Features:
New Standard Features - Ethernet is a standard feature on the Power Wave
®
i400 with no
additional hardware cost and also offers Lincoln Electric's Production Monitoring™ utility as a
part of the robotic solution.
Performance Based Design - 100 MHz, full duplex Ethernet interface offers a reliable and
consistent hardware platform for industrial environments, and facilitates future feature expansion.
Lower Cost System - Lower cost system for multi-equipment (multi-arm) through addition of a
network Ethernet switch. No additional cards or hardware required.
ArcLink Features:
Common User Interface - The Teach Pendant can display actual volts,
wire feed speed, etc, in process specific units.
Reduced Set-up Time - As an ArcLink
®
device, all communication with the
robot controller, power source, wire feeder are automatically recognized.
Full Access to Welding Database - Search by process, material, and
procedure right from the Teach Pendant and access all set-up variables.