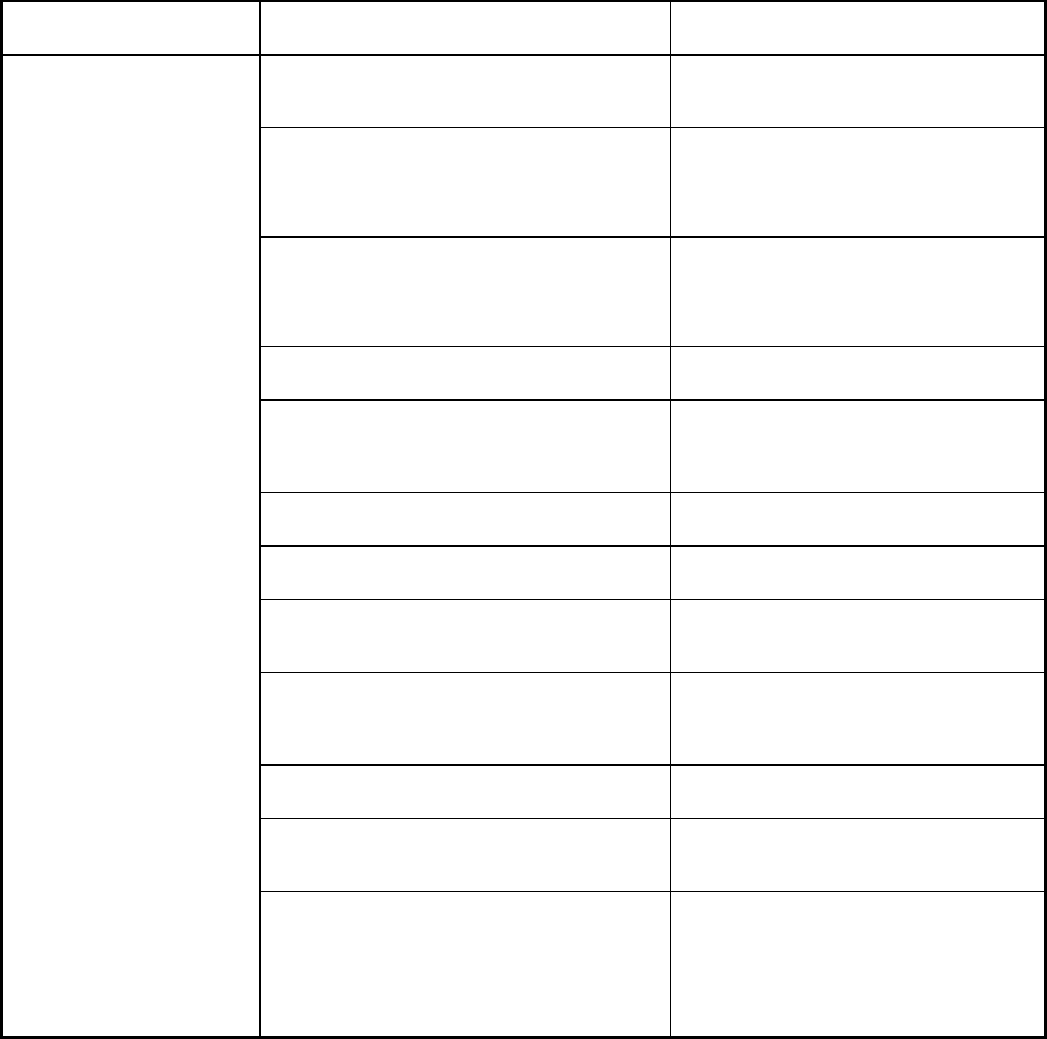
6 308842
Troubleshooting
LOW OUTPUT
TYPE OF PROBLEM
WHAT TO CHECK
If check is OK, go to next check
WHAT TO DO
When check is not OK refer to this column
Low Output 1. For worn spray tip. 1. Follow Pressure Relief Procedure Warn-
ing, then replace tip. See your separate
gun or tip manual.
2. Verify pump does not continue to stroke when
gun trigger is released. Plug in and turn on
sprayer. Prime with paint. Trigger gun momen-
tarily, then release and lock safety latch. Relieve
pressure, turn off and unplug sprayer.
2. Service pump. See page 17.
3. Electrical supply with volt meter.
Meter must read:
210–250 VAC for models 232144, 145, 154.
100–120 VAC for models 232148, 158.
90–110 VAC for models 232156, 157.
3. Reset building circuit breaker; replace
building fuse. Repair electrical outlet or try
another outlet.
4. Extension cord size and length; must be at least
12 gauge wire and no longer than 300 ft.
4. Replace with a correct, grounded exten-
sion cord.
5. Leads from motor to pressure control circuit
board (104) for damaged or loose wires or con-
nectors. Inspect wiring insulation and terminals
for signs of overheating.
5. Be sure male terminal blades are centered
and firmly connected to female terminals.
Replace any loose terminal or damaged
wiring. Securely reconnect terminals.
6. For loose motor brush leads and terminals. See
page 9.
6. Tighten terminal screws. Replace brushes
if leads are damaged. See page 9.
7. For worn motor brushes which must be 1/2 in.
minimum. See page 9.
7. Replace brushes. See page 9.
8. For broken and misaligned motor brush
springs. Rolled portion of spring must rest
squarely on top of brush.
8. Replace spring if broken. Realign spring
with brush. See page 9.
9. Motor brushes for binding in brush holders. See
page 9.
9. Clean brush holders, remove carbon dust
with small cleaning brush. Align brush lead
with slot in brush holder to assure free verti-
cal brush movement.
10.Stall pressure. 10.Replace with new pressure control board
(104). See page 12.
11.Motor armature for shorts by using an armature
tester (growler) or perform spin test. See page
9.
12.Replace motor. See page 16.
12.Motor control board (104) by performing motor
control board diagnostics on page 12. If diag-
nostics indicate, substitute with a good board.
CAUTION: Do not perform this check until mo-
tor armature is determined to be good. A bad
motor armature can burn out a good board.
11.Replace with new pressure control board
(104). See page 12.