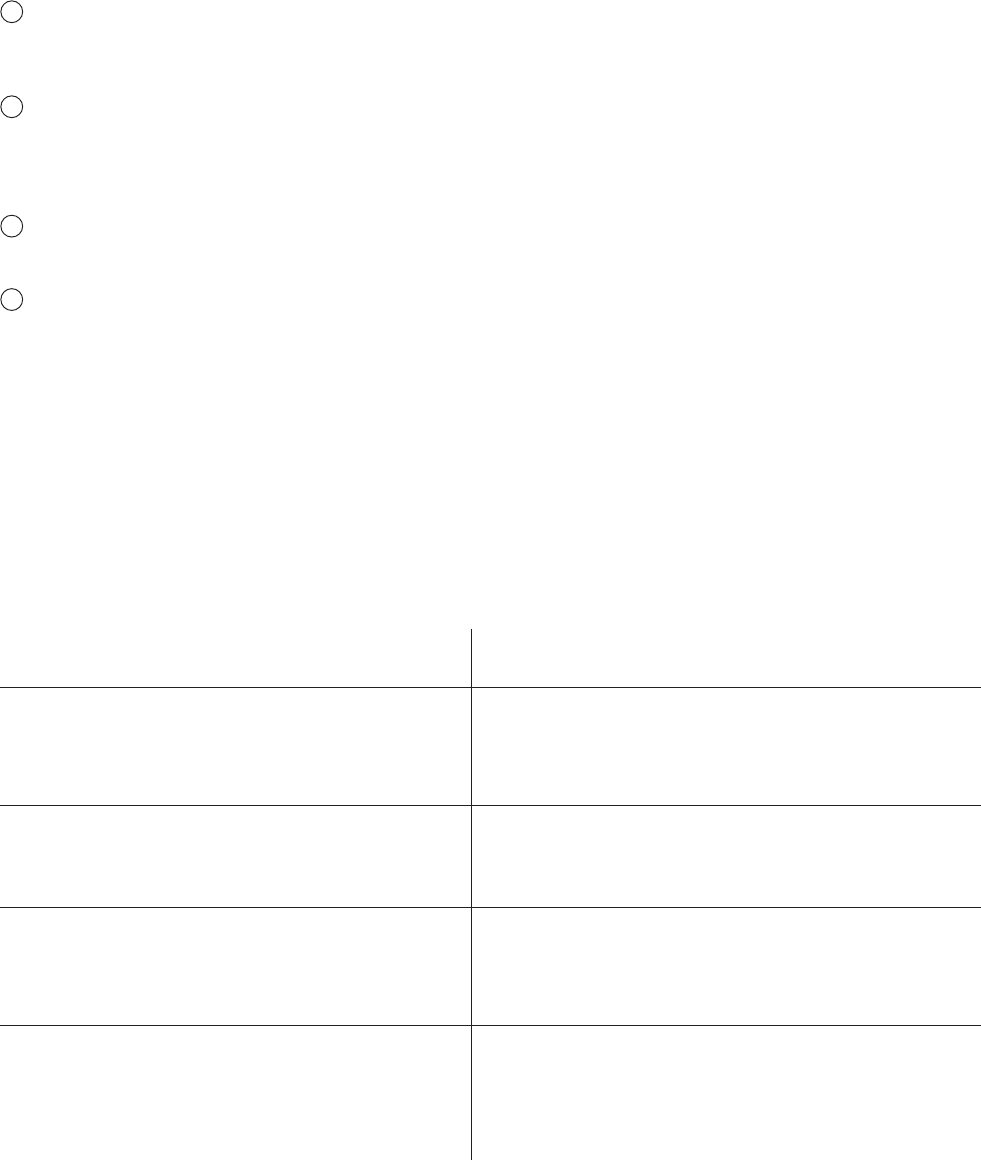
6 TIG Welding (optional)
Due to the same welding characteristics as with manual arc welding, TIG welding is possible with models Invert
130/40 and 130/60.
For TIG welding a TIG torch model SR 17 V (see section 11) is used, which is always connected to the negative
(-) pole. The arc is started by scratching with the tungsten electrode on the workpiece (causing a short-circuit).
The shielding gas is supplied directly from the pressure reducing device of the gas cylinder to the torch. A gas flow
rate of 6-7 l/min is recommended. Pure argon is required as shielding gas.
The earth lead is connected to socket [4]. The welding current is selected with the potentiometer [2], then the arc
is ignited by a brief contact of the tungsten electrode with the workpiece (scratch start).
When welding the control light [3] comes on and the
welding current goes off.
It is difficult to keep the arc burning.
Machine switched on but no welding current.
Poor arc starting with TIG welding
Porous welding seam
8 Trouble Shooting
Thermal overload protection has engaged. Let machine
run idle for several minutes to let cool down.
If the electrode is not moist, damaged or has been stored
too long, there may be a voltage drop (less than 190 V at
full load), probably caused by too long and extension
cord.
- check mains fuse
- voltage too high (over 250 V), which triggers the
corresponding protection device
- insufficient or no gas supply
- tungsten electrode wrongly ground
- wrong electrode diameter
- workpiece surface not clean (oil, grease)
- wrong setting of shielding gas flow rate (too much or
too little)
- wrong shielding gas (pure argon only)
- impurities in shielding gas
- wrong position of TIG torch
6.1 Practical Hints for Operation
To ensure good arc starting and good welding results the following should be adhered to:
1
2
3
4
Electrode types
Only thoriated electrodes are recommended for use, e.g.
WT 20 1.8 - 2.2 % thorium oxide, colour code: red or grey
Electrode diameter
The electrode diameter must correspond to the welding current.
Rule of thumb: less than 80 A Ø 1.0 mm
70 to 140 A Ø 1.6 mm
Tungsten electrodes have to be ground in longitudinal direction. Use a fine grit grinding wheel and grind from
tip to shaft.
Too much gas flow can reduced the arc starting ability (arc extinguished by blowing).
7 Overloads
The inverter welding machines are positively protected against overloads by several independent protection
devices. If the permissible duty cycle is exceeded, the machine is shut down automatically. This is indicated by
the control light [3]. After a short cooldown period the machine is operational again.
Important: Do not switch the machine off during the cooldown period, as this will cut the power to the fan,
considerably extending the cooldown period.