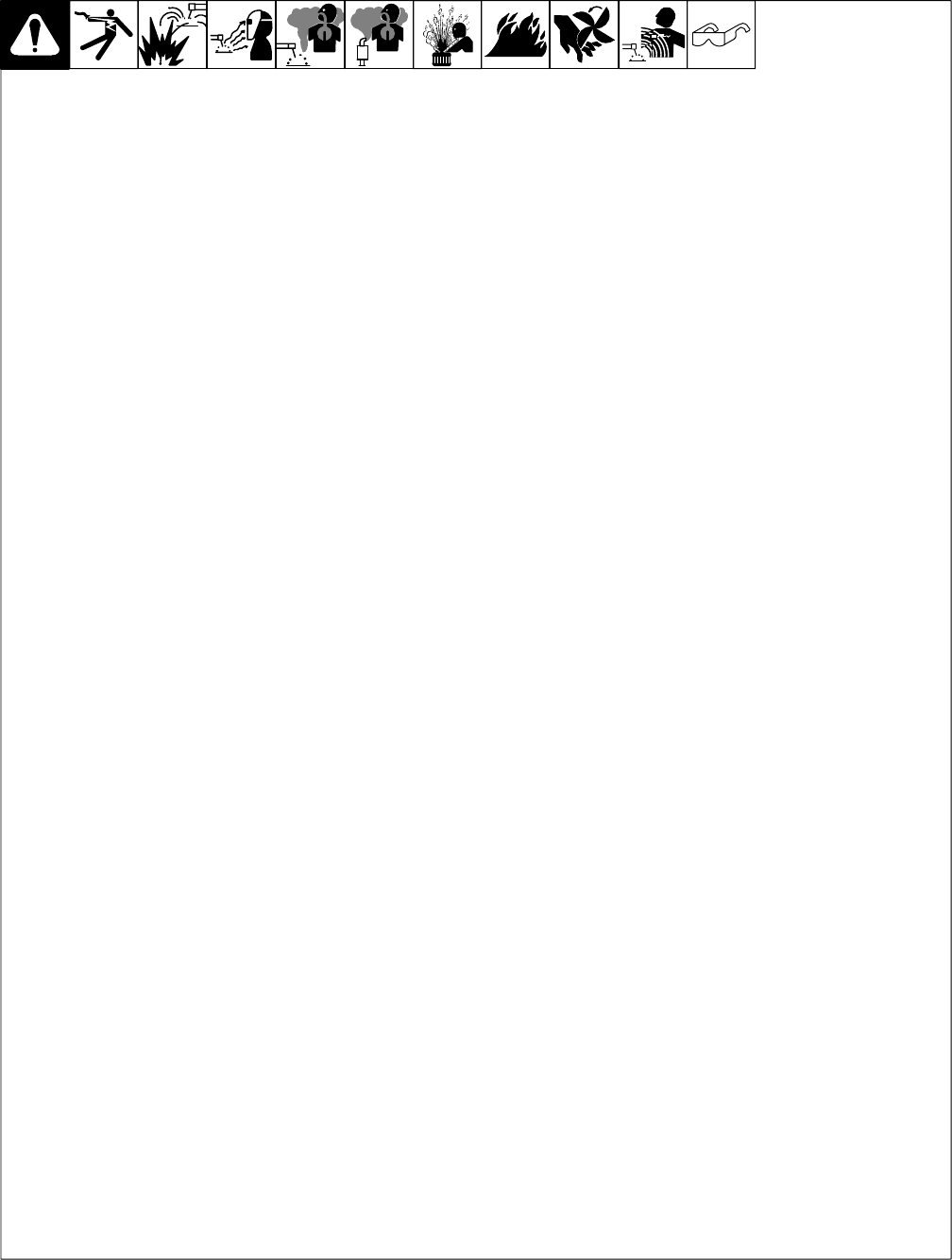
OM-4421 Page 27
6-2. Description Of Front Panel Controls For CC Models (See Section 6-1)
Engine Starting Controls
1 Starting Aid Switch
Use switch to energize starting aid for cold
weather starting (see starting instructions fol-
lowing).
2 Engine Control Switch
Use switch to start and stop engine.
To Start:
Y Do not use ether. Using ether voids
warranty.
. If engine does not start, let engine come
to a complete stop before attempting re-
start.
Above 325 F (05 C): turn Engine Control
switch to Start. Release Engine Control
switch when engine starts.
Below 325 F (05 C): push Starting Aid switch
up for 60 seconds. While still holding Starting
Aid switch, turn Engine Control switch to
Start. Release Engine Control switch and
Starting Aid switch when engine starts.
To Stop: turn Engine Control switch to Off
position.
Engine Gauges And Meters
3 Engine Hour Meter
Use hour meter to monitor engine run time to
help schedule maintenance.
4 Fuel Gauge
Use gauge to check fuel level.
To check fuel level when engine is not run-
ning, turn Engine Control switch to Run posi-
tion.
5 Battery Voltmeter (Optional)
Use gauge to check battery voltage and moni-
tor the engine charging system. The meter
should read about 14 volts dc when the en-
gine is running, and about 12 volts dc when
the engine is stopped.
6 Engine Coolant Temperature Gauge
(Optional)
Normal temperature is 180 - 203° F (82 - 95°
C). Engine stops if temperature exceeds 220°
F (104° C).
7 Engine Oil Pressure Gauge (Optional)
Normal pressure is 30 − 60 psi (207 − 414
kPa). Engine stops if pressure is below 10 psi
(69 kPa).
Weld Controls
. Max OCV Control Circuit: This unit has
a max OCV control circuit that resets Am-
perage Adjust control R1 to maximum
when the arc breaks. When an arc is
struck, weld output control returns to the
R1 front panel or combination front panel/
remote control setting. The Amperage
Adjust control adjusts amperage only
when welding and does not adjust open-
circuit voltage.
The max OCV circuit is disabled when
the Stick/TIG Selection switch is in
Scratch Start TIG position (see item 10).
8 Ampere Range Switch
Y Do not switch under load.
Use switch to select weld amperage range.
For most welding applications, use lowest
amperage range possible to help prevent arc
outages.
9 Amperage Adjust Control
Control adjusts amperage within range se-
lected by Ampere Range switch. Weld output
would be about 168 A DC with controls set as
shown (50% of 110 to 225 A).
. The numbers around the control are for
reference only and do not represent an
actual percentage value.
10 Stick/TIG Selection Switch
Use switch to disable the max OCV circuit
and the arc drive (dig) circuit for scratch start
TIG welding (see max OCV note under Weld
Controls).
When switch is in the Stick position, the max
OCV circuit resets Amperage Adjust Control
R1 to maximum when the arc breaks.
Also in the Stick position, the arc drive (dig)
circuit provides additional amperage during
low voltage (short arc length conditions) to
prevent “sticking” electrodes.
When switch is in Scratch Start TIG position,
the max OCV and arc drive (dig) circuits are
disabled and OCV changes when the control
is adjusted.
11 Amperage Adjust Switch And Remote
Amperage Adjust Receptacle
Connect optional remote control to RC13
(See Section 5-10). Use switch to select front
panel or remote amperage control. For re-
mote control, place switch in Remote position
and connect remote control to Remote Am-
perage Adjust receptacle RC13 (see Sec-
tions 5-10 and 6-3).
12 Polarity Switch (Optional)
Y Do not switch under load.
Use switch to change weld output. Select ei-
ther DC Electrode Positive (DCEP) or DC
Electrode Negative (DCEN).
Weld Meters
13 AC/DC Voltmeter (Optional)
Voltmeter displays voltage at the weld output
terminals, but not necessarily the welding arc
due to resistance of cable and connections.
14 AC/DC Ammeter (Optional)
Ammeter displays amperage output of the
unit.