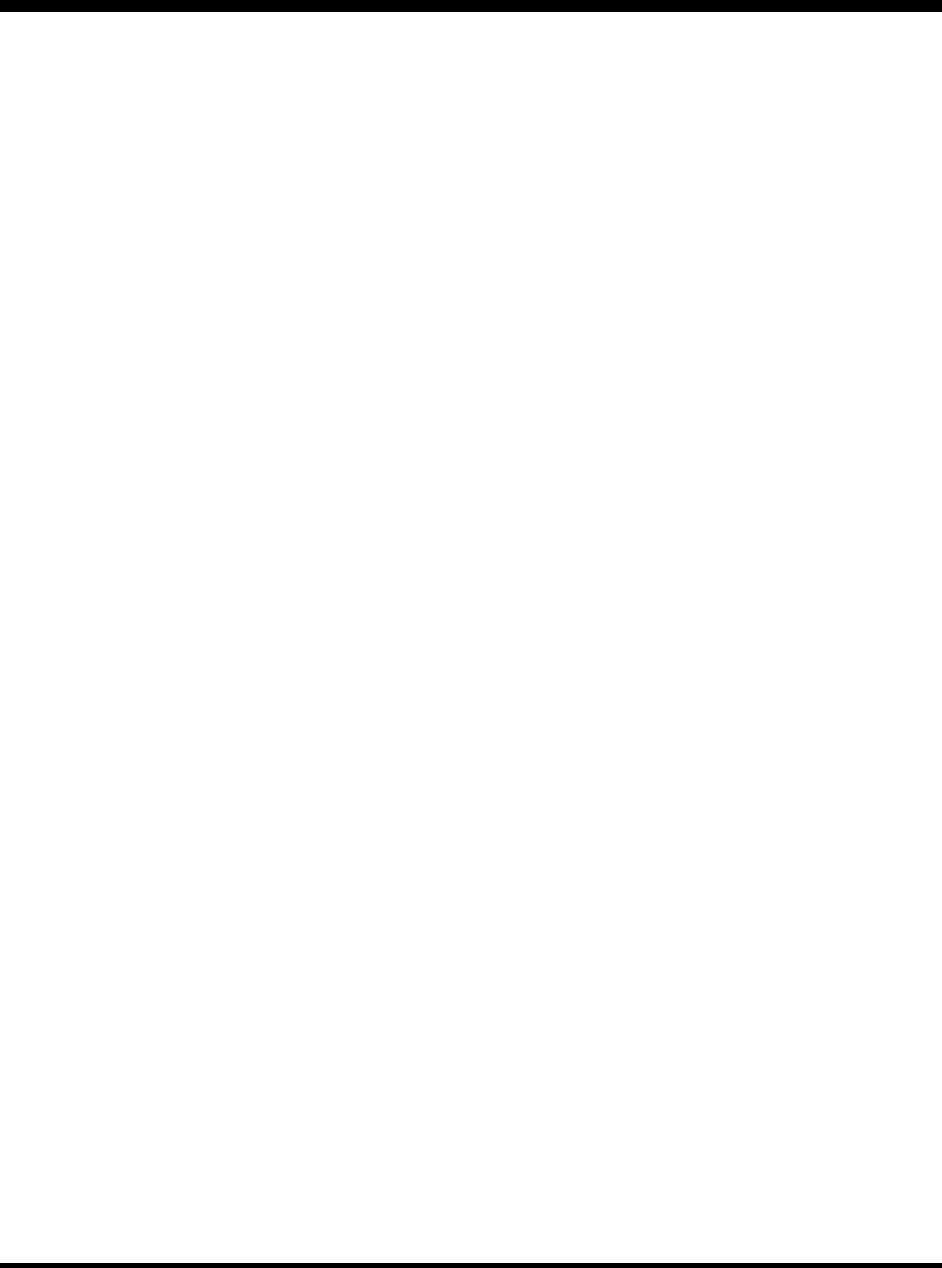
Page 26
5 Maintenance
5-1 Maintaining Drive Components
For continuing reliable operation of the granulator, it is of the
utmost importance that the motor drive belt tension is correct.
Correct tension reduces wear on the rotor and motor bearings and
reduces slip to a minimum.
Belt drives must be tensioned at the “Run-In” recommended force.
Check the tension at least twice during the first two days’
operation. After the belts have seated themselves in the sheave
grooves and the initial stretch is removed, re-tension the belts to
the “Normal Running” recommended force.
A gauge is available from customer service or the belt
manufacturer which facilitates the measurement of belt deflection
and force.
The Belt Tensioning Chart in Figure 1 gives the recommended
force required to deflect teach belt by an amount equal to the belt
span divided by 64. The Deflection Force Value relates to a single
V-belt element.
1. Verify that the alignment of the sprockets is correct. Using a
straightedge of sufficient length to span from one sprocket to
the other, place it along the sides of both sprockets. The entire
edge of each sprocket should contact the straightedge.
2. Measure the timing belt sag. See Figure 1.
3. Determine the force required to deflect one belt 1/64” (0.40
mm) per 1 inch (25.4 mm) of span length as follows:
a. Measure span length (t) of your drive.
b. At the center of span (t), apply a force perpendicular to
the span large enough to deflect one belt on the drive
1/64” (0.40 mm) span length from its normal position.
4. Compare this deflection force with range of forces in the Belt
Tensioning Chart as follows:
a. If it is less than the minimum recommended force, belts
should be tightened.
b. If it is more than the maximum recommended
deflection force, the drive is as tight as it needs to be.