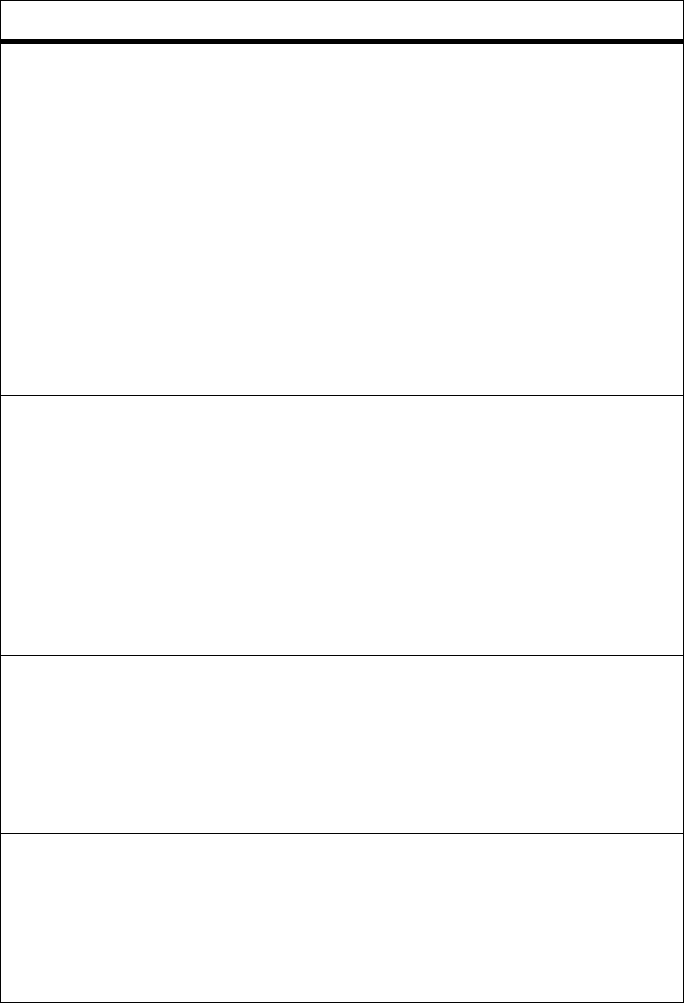
14
SM-97
PROBLEM CAUSE & REMEDY
Motor will not run.
1. Inefficient air supply
—Check 90 psi and 32 CFM air supply.
2. Clogged air inlet screen
—Replace-see pg.6(pc #75, pg.13).
3. Broken or severely worn rotor blades
—Replace-see pg.6(pc #69, pg.13).
4. Rust due to improper storage of tool
—Disassemble and clean– Refer to Dis-
assembly procedure.
5. Broken throttle valve pin or lever
—Replace–see pg.6(pc. #78/80, pg. 13).
Motor will not reach
RPM.
1. Insufficient air volume
—Check 32 CFM supply.
2. Dirty air inlet screen
—Clean –see pg. 6 (pc.#75, pg.13).
3. Worn rotor blades
—Replace-see pg.6(pc #69, pg.13).
4. Air supply hose chocked or too small
—See Operating Procedure recom-
mended hose.
Motor stalls at high
torque
1. Insufficient air pressure
—Check 90 psi supply
2. Dirty air inlet screen
—Clean –see pg. 6 (pc.#75, pg.13).
3. Rotor blades worn, chipped or broken
—Replace-see pg.6(pc #69, pg.13).
Motor fails to stop
1. Broken throttle valve spring
—Replace-see pg.6(pc #76, pg.13).
2. Valve ball does not seal
—Replace or rework valve seat-Refer to
pg. 6 (pc.#77, pg.13)
TROUBLE-SHOOTING
3
SM-97
GUIDELINES FOR TUBE EXPANSION
RECOMMENDED OPERATING AIR PRESSURE 90 PSI
OPERATION
Tube Expansion Calculations
Tube Sheet Hole Dia. .760
- Tube O.D. -.750
= Clearance =.010
+ Tube I.D. +.652
=I.D. @ Metal to Metal =.662
+4%Reduction (.049x.04x2) +.004
=Expanded I.D. =.666
Improperly rolled joints create additional expense to correct, whether
they are under-rolled and can be corrected merely by rerolling, or
over-rolled and require removal and replacement. The optimal joint is
one that develops a leak tight joint with adequate strength for the ser-
vice intended with the minimum amount of cold working or reduction
of the tube wall. Experience
indicates that joints of this type are ob-
tainable with non-ferrous tubes in surface condensers by expanding
to a wall reduction of 3% to 4% after metal to metal contact of the
tube 0.D. with the tube sheet hole. Steel tubes in heat exchangers
may require wall
reductions of 5% to 10%; soft copper and aluminum tubes in heat ex-
changers also require larger wall reductions in the area of 8% to 12%.
Boiler tubes requiring development of optimum joint strength require
wall reductions of 12% to 14%.
A typical example of the application of this method is indicated for a
3/4” x 18 ga. tube in a condenser.
1. Make sure there is an adequate supply of clean air of 90
psi lubricated with light machine oil of SAE 10 viscosity.
This should be done before all long runs of tube expanding
and after every four hours of continuous use unless an air
line lubricator of ample capacity is used. SEE
’LUBRICATION’ SECTION BELOW.