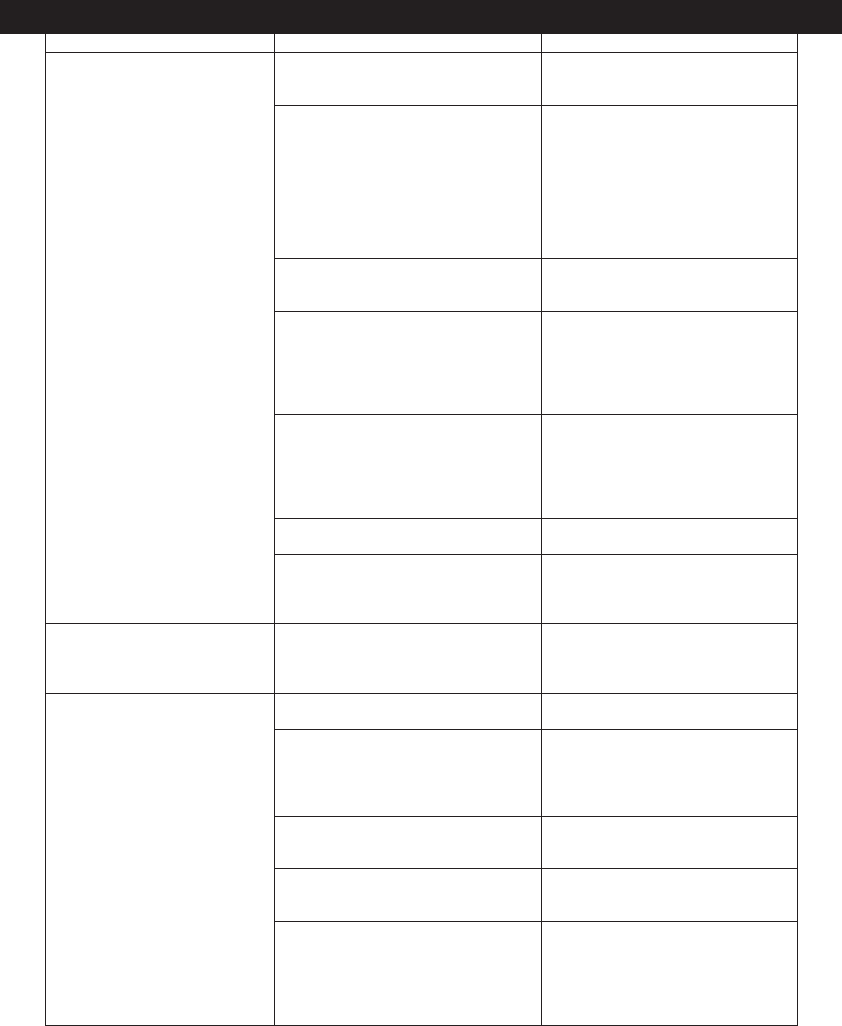
34-8700-5191-8 5 Revision 10/03/07
Symptom Possible Cause Solution
Low Power and/or Low Free Speed
Insufcient Air Pressure
Check air line pressure at the Inlet of
the Sander while the tool is running at
free speed. It must be 90 psig (6.2 Bar).
Clogged Mufer(s)
See the “Housing Disassembly” section
for Mufer removal. The Mufer can
be back ushed with a clean, suitable
cleaning solution until all contaminates
and obstructions have been removed. If
the Mufer can not be properly cleaned
then replace it. Replace Mufer Insert
(See the
“Housing Assembly” Section).
Plugged Inlet Screen
Clean the Inlet Screen with a clean,
suitable cleaning solution. If Screen
does not come clean replace it.
One or more Worn or Broken Vanes
Install a complete set of new Vanes
(all vanes must be replaced for proper
operation). Coat all vanes with quality
pneumatic tool oil. See “Motor Disas-
sembly” and
“Motor Assembly”.
Internal air leakage in the Motor Housing
indicated by higher than normal air con-
sumption and lower than normal speed.
Check for proper Motor alignment and
Lock Ring engagement. Check for
damaged O-Ring in Lock Ring groove.
Remove Motor Assembly and Re-Install
the Motor Assembly. See “Motor Disas-
sembly” and “Motor Assembly”.
Motor Parts Worn
Overhaul Motor. Contact authorized
Service Center.
Worn or broken Spindle Bearings
Replace the worn or broken Bearings.
See “Shaft Balancer and Spindle Disas-
sembly” and “Spindle Bearings, Bearing
Shield and Shaft Balancer Assembly”.
Air leakage through the Speed
Control and/or Valve Stem.
Dirty, broken or bent Valve Spring, Valve
or Valve Seat.
Disassemble, inspect and replace worn
or damaged parts. See Steps 2 and 3
in “Housing Disassembly” and Steps 2
and 3 in “Housing Assembly”.
Vibration/Rough Operation
Incorrect Pad
Only use Pad Sizes and Weights
designed for the machine.
Addition of interface pad or other material
Only use abrasive and/or interface
designed for the machine. Do not at-
tach anything to the Sanders Pad face
that was not specically designed to be
used with the Pad and Sander.
Improper lubrication or buildup of foreign
debris.
Disassemble the Sander and clean in
a suitable cleaning solution. Assemble
the Sander.
Worn or broken Rear or Front Motor
Bearing(s)
Replace the worn or broken Bearings.
See “Motor Disassembly” and “Motor
Assembly”.
For vacuum machines it is possible to
have too much vacuum while sanding on
a at surface causing the pad to stick to
the sanding surface.
For SGV machines add extra washer(s)
to the pad spindle to increase the gap
between the pad and shroud. For CV
machines reduce vacuum through
the vacuum system and/or add extra
washer(s) to the pad.
Troubleshooting Guide