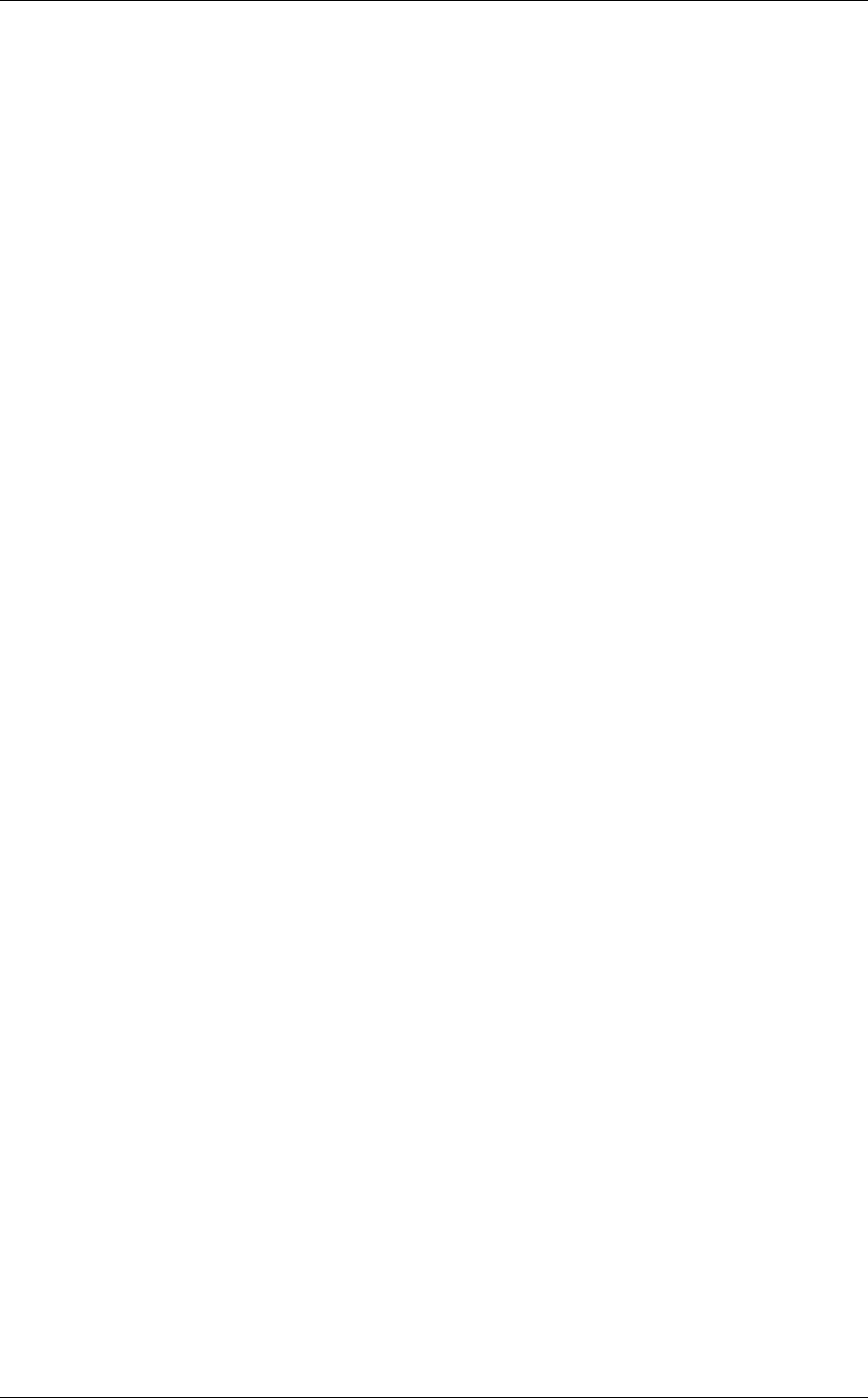
4.7 Servo Control
C141-E050-02EN 4-19
(1) Write/read recovery
This area is used to absorb the write/read transient and to stabilize the AGC.
(2) Servo mark
This area gererates a timing for demodulating the gray code and position-
demodulating the servo A to D by detecting the servo mark.
(3) Gray code (including index bit)
This area is used as cylinder address. The data in this area is converted into the
binary data by the gray code demodulation circuit
(4) Servo A, servo B, servo C, servo D
This area is used as position signals between tracks, and the IDD control at on-
track so that servo A level equals to servo B level.
(5) PAD
This area is used as a gap between servo and data.
4.7.4 Actuator motor control
The voice coil motor (VCM) is controlled by feeding back the servo data recorded
on the data surface. The MPU fetches the position sense data on the servo frame
at a constant interval of sampling time, executes calculation, and updates the
VCM drive current.
The servo control of the actuator includes the operation to move the head to the
reference cylinder, the seek operation to move the head to the target cylinder to
read or write data, and the track-following operation to position the head onto the
target track.
(1) Operation to move the head to the reference cylinder
The MPU moves the head to the reference cylinder when the power is turned. The
reference cylinder is in the data area.
When power is applied the heads are moved from the inner circumference shunt
zone to the normal servo data zone in the following sequence:
a) Micro current is fed to the VCM to press the head against the inner
circumference.
b) Micro current is fed to the VCM to move the head toward the outer
circumference.
c) When the servo mark is detected the head is moved slowly toward the outer
circumference at a constant speed.