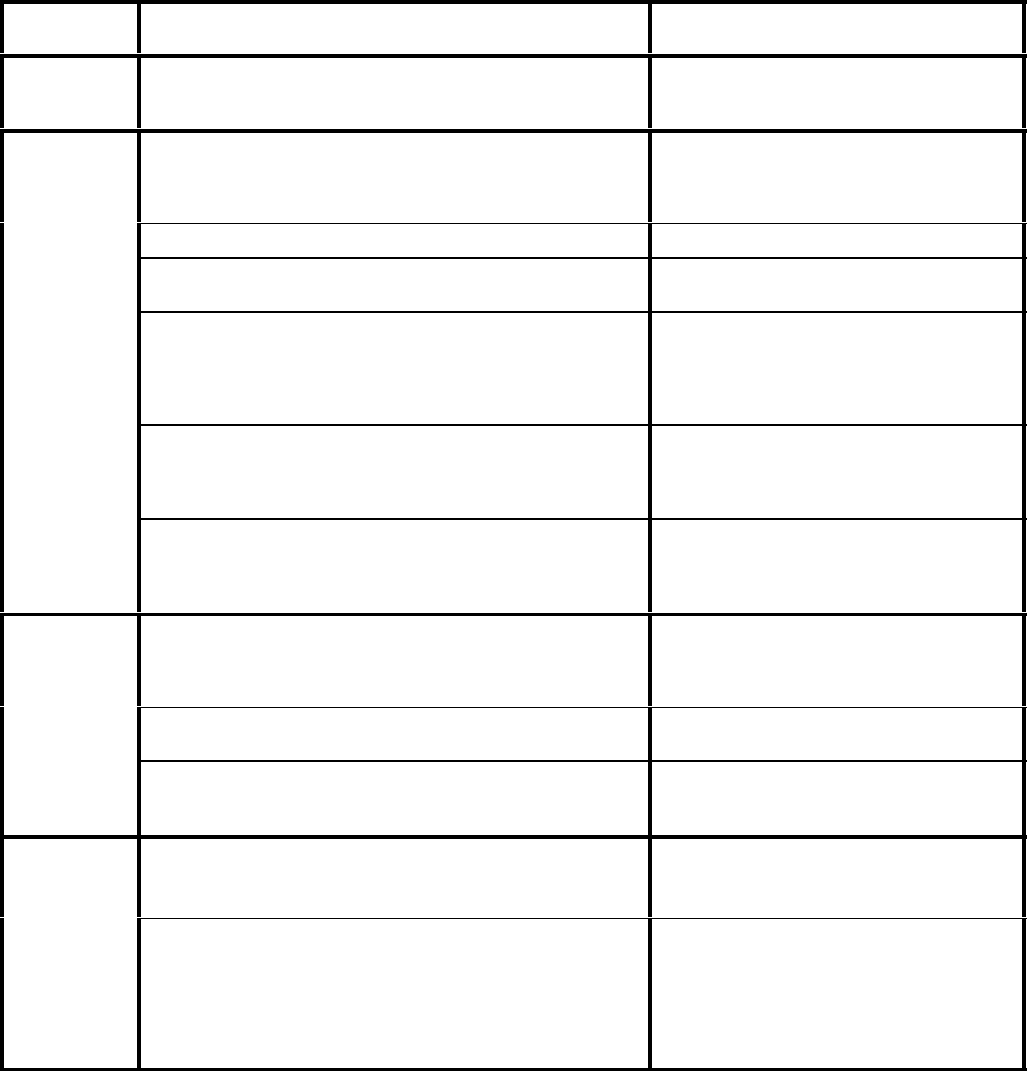
309067 7
Intermediate Problem Solving
TYPE OF
PROBLEM
WHAT TO CHECK
If check is OK, go to next check
WHAT TO DO
When check is not OK, refer to this column
Drain valve
leaks
1. Drain valve for correct torque and/or worn parts. Check for
debris trapped on seat.
1. Tighten to 185 in-lb (21 Nm). Clean
valve and replace with new gasket (55)
and sealant 110–110. See page 18.
No output:
motor runs
and pump
strokes
1. Paint supply. 1. Refill and reprime pump.
2. For clogged intake strainer. 2. Remove and clean, then reinstall.
3. For loose suction tube or fittings. 3. Tighten; use thread sealant on
npt threads of adapter fitting (43).
4. To see if intake valve ball and piston ball are seating
properly. See page 11.
4. Remove intake valve and clean. Check
ball and seat for nicks; replace as need-
ed. See page 11. Strain paint before us-
ing to remove particles that could clog
pump.
5. For leaking around throat packing nut which may indicate
worn or damaged packings. See page 11.
5. Replace packings. See page 11. Also
check piston valve seat for hardened
paint or nicks and replace if necessary.
Tighten packing nut.
6. Release gun trigger. Observe resting position of pump rod
(222).
6. If pump consistently comes to rest
with rod (222) fully extended, piston
packings and/or piston valve may be
worn. Service pump. See page 11.
No output:
motor runs but
pump does not
stroke
1. Displacement pump connecting rod pin (14).
See Fig. 9, page 11.
1. Replace pin if missing. Be sure retainer
spring (15) is fully in groove all around
connecting rod.
2. Connecting rod assembly (12) for damage. See page 15. 2. Replace connecting rod assembly. See
page 15.
3. Be sure crank in drive housing rotates; plug in sprayer and
turn on briefly to check. Turn off and unplug sprayer.
See page 15.
3. Check drive housing assembly for dam-
age and replace if necessary. See
page 15.
Spray pattern
variations
1. Spray tip worn beyond sprayer pressure capability. 1. Replace spray tip.
NOTE: Smaller size tip provides
longer life.
2. Motor control board (22a) by performing motor control
board diagnostics on page 13. If diagnostics indicate, sub-
stitute with a good board.
CAUTION: Do not perform this check until motor armature
is determined to be good. A bad motor armature can burn
out a good board.
2. Replace board. See page 13.