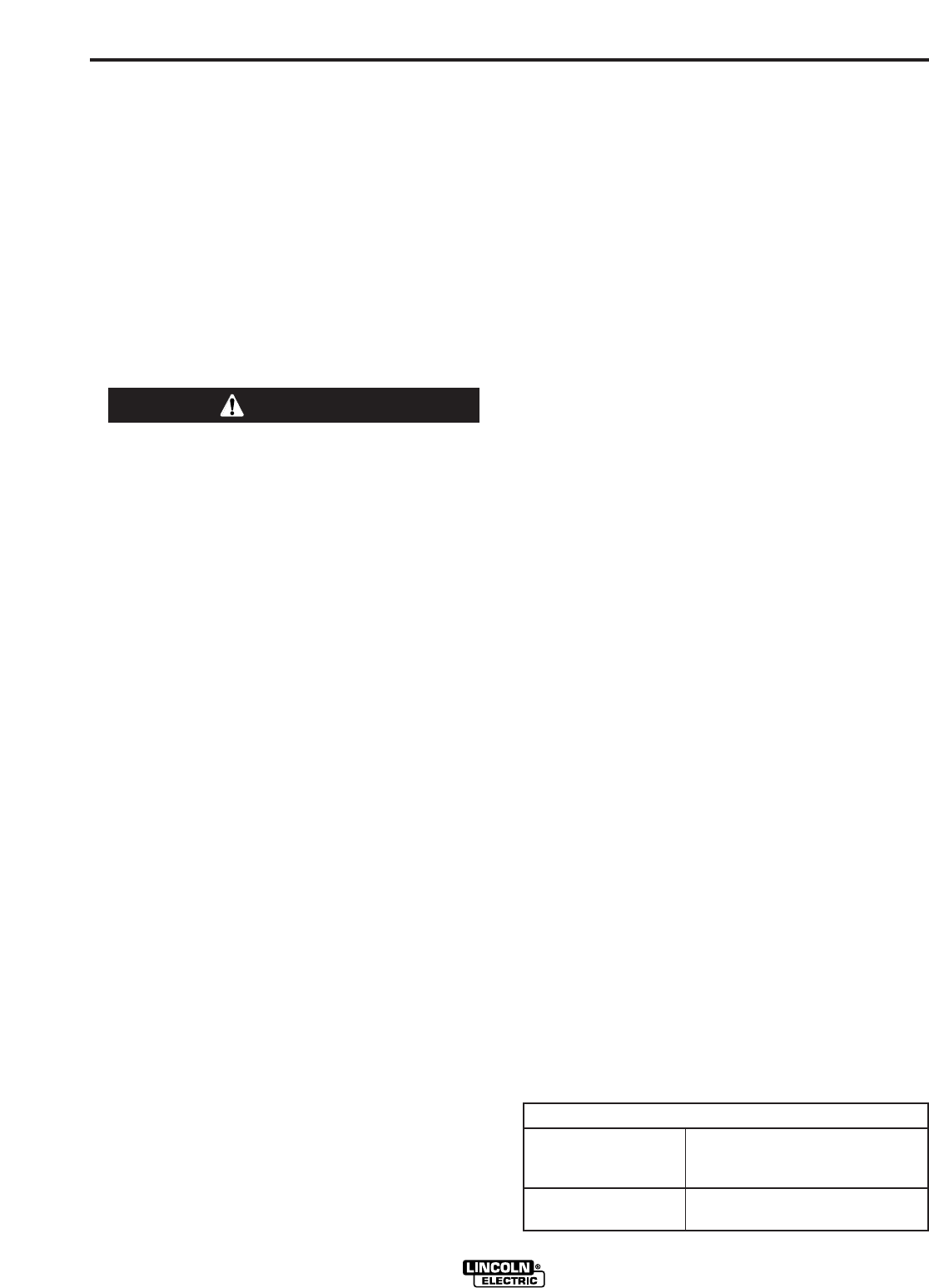
A-5
INSTALLATION
RANGER 10,000 PLUS AND RANGER 10,000
A-5
LOCATION / VENTILATION
The welder should be located to provide an unrestricted
flow of clean, cool air to the cooling air inlets and to avoid
heated air coming out of the welder recirculating
back to the cooling air inlet. Also, locate the welder so
that engine exhaust fumes are properly vented to an out-
side area.
STACKING
RANGER 10,000 PLUS AND RANGER 10,000 machines
cannot be stacked.
CONNECTION OF LINCOLN ELECTRIC
WIRE FEEDERS
Shut off welder before making any electrical connec-
tions.
----------------------------------------------------------------------------
WIRE FEED (CONSTANT VOLTAGE)
CONNECTION OF LN-15 ACROSS-THE-ARC WIRE
FEEDER
The LN-15 has an internal contactor and the electrode is
not energized until the gun trigger is closed. When the
gun trigger is closed the wire will begin to feed and the
welding process is started.
a. Shut the welder off.
b. Connect the electrode cable from the LN-15 to
the“ELECTRODE” terminal of the welder. Connect the
work cable to the “TO WORK” terminal of the welder.
c. Set the Polarity switch to the desired polarity, either
DC (-) or DC (+).
d. Attach the single lead from the front of the LN-15 to
work using the spring clip at the end of the lead.
This is a control lead to supply current to the wire
feeder motor; it does not carry welding current.
e. Set the “RANGE” switch to the “WIRE FEED-CV”
position
f. Place the Engine switch in the “Auto Idle” position.
g. Adjust the wire feed speed at the LN-15 and adjust
the welding voltage with the output “CONTROL” at
the welder. Output “CONTROL” must be set above 3.
Note: LN-15 Control Cable model will not work with
the RANGER 10,000 PLUS AND RANGER 10,000.
CONNECTION OF THE LN-25 TO THE RANGER 10,000
a. Shut the welder off.
b. Connect the electrode cable from the LN-25 to
the“ELECTRODE” terminal of the welder. Connect
the work cable to the “TO WORK” terminal of the
welder.
c. Position the welder “Polarity” switch to the desired
polarity, either DC (-) or DC (+).
RANGER 10,000 PLUS AND RANGER 10,000
Constant Current 225 Amps AC @ 25 Volts
210 Amps DC @ 25 Volts
Constant Voltage 200 Amps DC @ 20 Volts
d. Position the “RANGE” switch to the “WIRE FEED”
position.
e. Attach the single lead from the LN-25 control box to
the work using the spring clip on the end of the lead
- it carries no welding current.
f. Place the engine switch in the “AUTO” position.
g. Adjust wire feed speed at the LN-25 and adjust the
welding voltage with the output “CONTROL” at the
welder.
NOTE: The welding electrode is energized at all times,
unless an LN-25 with built-in contactor is used. If the
output “CONTROL” is set below “3”, the LN-25 contactor
may not pull in.
CONNECTION OF K930-2 TIG MODULE TO THE
RANGER 10,000.
The TIG Module is an accessory that provides high fre-
quency and shielding gas control for AC and DC GTAW
(TIG) welding. See IM528 supplied with the
TIG Module for installation instructions.
Note: The TIG Module does not require the use of a high
frequency bypass capacitor. However, if the RANGER
10,000 PLUS or RANGER 10,000 is used with any other
high frequency equipment, the bypass capacitor must be
installed, order kit T12246.
INSTRUCTIONS
ADDITIONAL SAFETY PRECAUTIONS
Always operate the welder with the roof and case sides
in place as this provides maximum protection from mov-
ing parts and assures proper cooling air flow.
Read and understand all Safety Precautions before oper-
ating this machine. Always follow these and any other
safety procedures included in this manual and in the
Engine Owner’s Manual.
WELDER OPERATION
WELDER OUTPUT
• Maximum Open Circuit Voltage at 3700 RPM is
80 Volts RMS.
• Duty Cycle is the percentage of time the load is
being applied in a 10 minute period. For example, a
60% duty cycle represents 6 minutes of load and 4
minutes of no load in a 10 minute period. Duty Cycle
for the RANGER 10,000 PLUS AND RANGER
10,000
is 100%.
WARNING