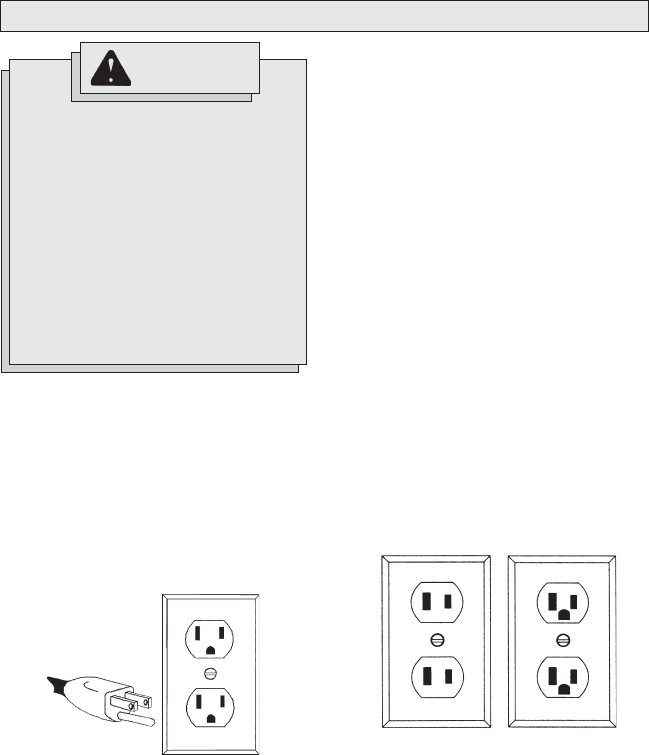
4 5
Kickback is the result of saw misuse
and/or incorrect operating procedures or
conditions and can be avoided by taking
proper precautions as given below:
a. Maintain a fi rm grip with both hands
on the saw and position your arms
to resist kickback forces. Position
your body to either side of the
blade, but not in line with the blade.
Kickback could cause the saw to jump
backwards, but kickback forces can
be controlled by the operator, if proper
precautions are taken.
b. When blade is binding, or when inter-
rupting a cut for any reason, release
the trigger and hold the saw motion-
less in the material until the blade
comes to a complete stop. Never
attempt to remove the saw from the
work or pull the saw backward while
the blade is in motion or kickback
may occur. Investigate and take cor-
rective actions to eliminate the cause
of blade binding.
c. When restarting a saw in the work-
piece, centre the saw blade in the kerf
and check that saw teeth are not en-
gaged into the material. If saw blade is
binding, it may walk up or kickback from
the workpiece as the saw is restarted.
d. Support large panels to minimise the
risk of blade pinching and kickback.
Large panels tend to sag under their
own weight. Supports must be placed
under the panel on both sides, near
the line of cut and near the edge of the
panel.
e. Do not use dull or damaged blades.
Unsharpened or improperly set blades
produce narrow kerf causing excessive
friction, blade binding and kickback.
f. Blade depth and bevel adjusting
locking levers must be tight and
secure before making cut. If blade
adjustment shifts while cutting, it may
cause binding and kickback.
g. Use extra caution when making a
“plunge cut” into existing walls or
other blind areas. The protruding
blade may cut objects that can cause
kickback.
10. Check lower guard for proper closing
before each use. Do not operate the
saw if lower guard does not move
freely and close instantly. Never
clamp or tie the lower guard into
the open position. If saw is acciden-
tally dropped, lower guard may be bent.
Raise the lower guard with the retracting
handle and make sure it moves freely and
does not touch the blade or any other part,
in all angles and depths of cut.
11. Check the operation of the lower
guard spring. If the guard and the
spring are not operating properly,
they must be serviced before use.
Lower guard may operate sluggishly
due to damaged parts, gummy deposits,
or a build-up of debris.
12. Lower guard should be retracted
manually only for special cuts such
as “plunge cuts”and “compound
cuts.” Raise lower guard by retract-
ing handle and as soon as blade
enters the material, the lower guard
must be released. For all other saw-
ing, the lower guard should operate
automatically.
13. Always observe that the lower guard
is covering the blade before plac-
ing saw down on bench or fl oor. An
unprotected, coasting blade will cause
the saw to walk backwards, cutting
whatever is in its path. Be aware of the
time it takes for the blade to stop after
switch is released.
14. Do not use abrasive wheels with
circular saws. Dust and grit can cause
lower guard to hang up and not operate
properly.
15. Maintain labels and nameplates.
These carry important information.
If unreadable or missing, contact a
MILWAUKEE service facility for a free
replacement.
16. WARNING: Some dust created by
power sanding, sawing, grinding, drill-
ing, and other construction activities
contains chemicals known to cause
cancer, birth defects or other reproduc-
tive harm. Some examples of these
chemicals are:
• lead from lead-based paint
• crystalline silica from bricks and ce-
ment and other masonry products,
and
• arsenic and chromium from chemi-
cally-treated lumber.
Your risk from these exposures varies,
depending on how often you do this
type of work. To reduce your exposure
to these chemicals: work in a well ven-
tilated area, and work with approved
safety equipment, such as those dust
masks that are specifi cally designed to
fi lter out microscopic particles.
The grounding prong in the plug is connected
through the green wire inside the cord to
the grounding system in the tool. The green
wire in the cord must be the only wire con-
nected to the tool's grounding system and
must never be attached to an electrically
“live” terminal.
Your tool must be plugged into an appropri-
ate outlet, properly installed and grounded in
accordance with all codes and ordinances.
The plug and outlet should look like those
in Figure A.
Double Insulated Tools:
Tools with Two Prong Plugs
Tools marked “Double Insulated” do not
require grounding. They have a special
double insulation system which satisfies
OSHA requirements and complies with
the applicable standards of Underwriters
Laboratories, Inc., the Canadian Standard
Association and the National Electrical
Code. Double Insulated tools may be used
in either of the 120 volt outlets shown in
Figures B and C.
Grounded Tools:
Tools with Three Prong Plugs
Tools marked “Grounding Required” have a
three wire cord and three prong grounding
plug. The plug must be connected to a prop-
erly grounded outlet (See Figure A). If the
tool should electrically malfunction or break
down, grounding provides a low resistance
path to carry electricity away from the user,
reducing the risk of electric shock.
Fig. B
Fig. C
Fig. A
Improperly connecting the grounding
wire can result in the risk of electric
shock. Check with a qualifi ed electri-
cian if you are in doubt as to whether
the outlet is properly grounded. Do
not modify the plug provided with
the tool. Never remove the grounding
prong from the plug. Do not use the
tool if the cord or plug is damaged.
If damaged, have it repaired by a
MILWAUKEE service facility before
use. If the plug will not fi t the outlet,
have a proper outlet installed by a
qualifi ed electrician.
GROUNDING
WARNING