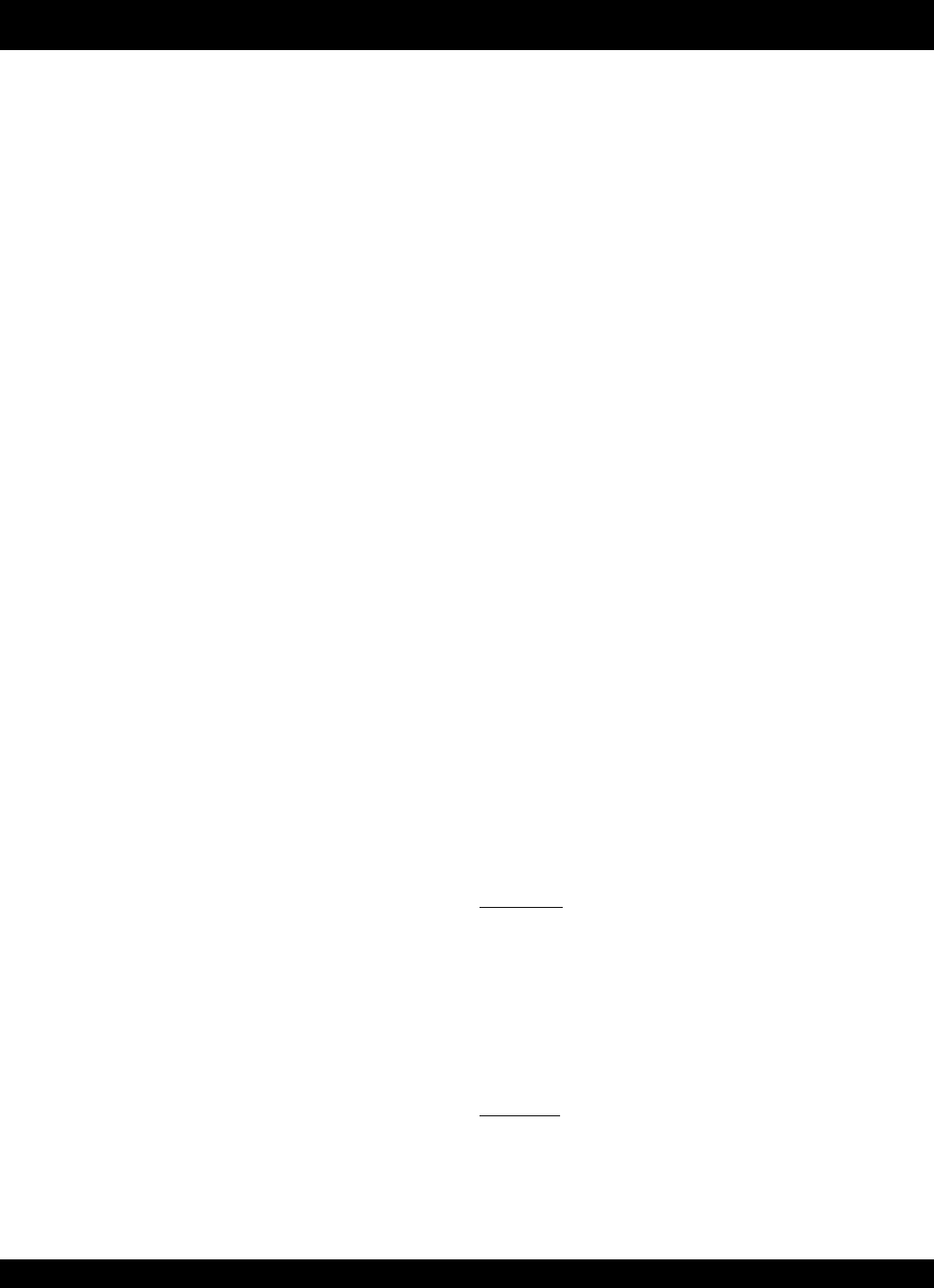
ESSICK FM9 — PARTS & OPERATION MANUAL — REV. #1 (03/12/01) — PAGE 7
FM-9 — OPERATIONS
SAFETY
1. Do not operate or service this equipment before reading the
operating and maintenance instruction manual.
2. Do not operate this equipment unless all guards and safety
devices are attached and in place.
3. Stop engine when leaving equipment.
4. Block unit when parking on a slope.
5. Maintain this equipment in safe operating condition at all
times.
6. Caution must be exercised while servicing this equipment.
Rotating and moving parts can cause injury if contacted.
7. Stop engine before adding fuel or oil. Never spray water
over the engine or electrical motor.
8. Keep all inexperienced and unauthorized people away from
equipment at all times.
9. Unauthorized equipment modifications will void all
warranties.
10. Run transmission in reverse gear to relieve back pressure
before disconnecting gun or hoses.
11. Screen must be on hopper at all times machine is in
operation.
12. Stop engine before putting hands in hopper.
13. Wear safety eye glasses at all times when working around
machine or material lines.
14. Electrical operated machines refer to supplemental FM5E-
I safety/operating instructions
GENERAL
The essick model FM9 plastering machine is in a class by itself.
Its main functions are that of a standard finishing machine: Mainly
applying acoustical ceilings, exterior dash stucco finish and
inside sand finish, as well as fireproofing steel beams. Although
it was not designed to be used in place of a high-volume base
coat plastering machine, it may be used to apply inside brown
and it is capable of applying a half-sand, half-vermiculite mix at
a very practical rate, which is satisfactory for some jobs.
This machine is equipped with a transmission having 3 forward
speeds plus a reverse gear and is powered by a 9.2 hp engine,
which also drives a heavy-duty twin-cylinder air compressor.
Although the procedure for mixing and applying the materials
varies with each material being sprayed, the following procedure
applies to all the materials mentioned above.
OPERATING INSTRUCTIONS
Connect the air lines from the machine to the air control block
mounted on the nozzle. One air line runs from the air compressor
outlet on the machine to the inlet on the control block next to the
sleeve valve. This line has air blowing out of it when the
compressor is running. The other air line runs from the sleeve
valve on the control block to the throttle cylinder inlet on the
machine.
In operation, the compressor furnishes air to the control block.
The valve located on the front of the block is for the adjustment of
atomized air which is used for the spraying of material. The sleeve
valve operates the throttle cylinder on the engine. When the
sleeve valve is in the closed position, air pressure is applied to
the cylinder and the engine will speed up to the preset governed
speed. When the sleeve valve is in the open position, air pressure
is released from the spring loaded throttle cylinder and the
engine will return to idle speed.
Before starting engine, check oil levels in engine crankcase,
transmission and compressor. Place volume control lever
(transmission lever) in the position for the desired speed to be
used. Turn the throttle control air valve, located on the spray gun,
to the “off position.
After mixing the material, lubricate the pump and hose by pouring
a few gallons of water into the hopper. Adjust the air pressure to
approximately 20 lbs. and turn the throttle control air valve to
“on” position.
Continue to pump out the water until it reaches the level of the
pump. Then fill the hopper half full with the material to be sprayed.
After the remaining water in the hose has been pumped out and
material appears at the nozzle, point nozzle into hopper and
make final air adjustments. With final adjustments made, turn air
valve off.
CAUTION: Never turn off pump until material appears at nozzle.
This may cause separation of the material, which would clog up
pump and hose.
Fill hopper and carry nozzle and hose to spraying area. Turn air
valve”on” and proceed to spray, working a pattern. Always overlap
the spray, but never hold the gun still in an attempt to fill a void or
defect.
CAUTION: Never run the pump dry, as this causes rapid
pump wear or damage.