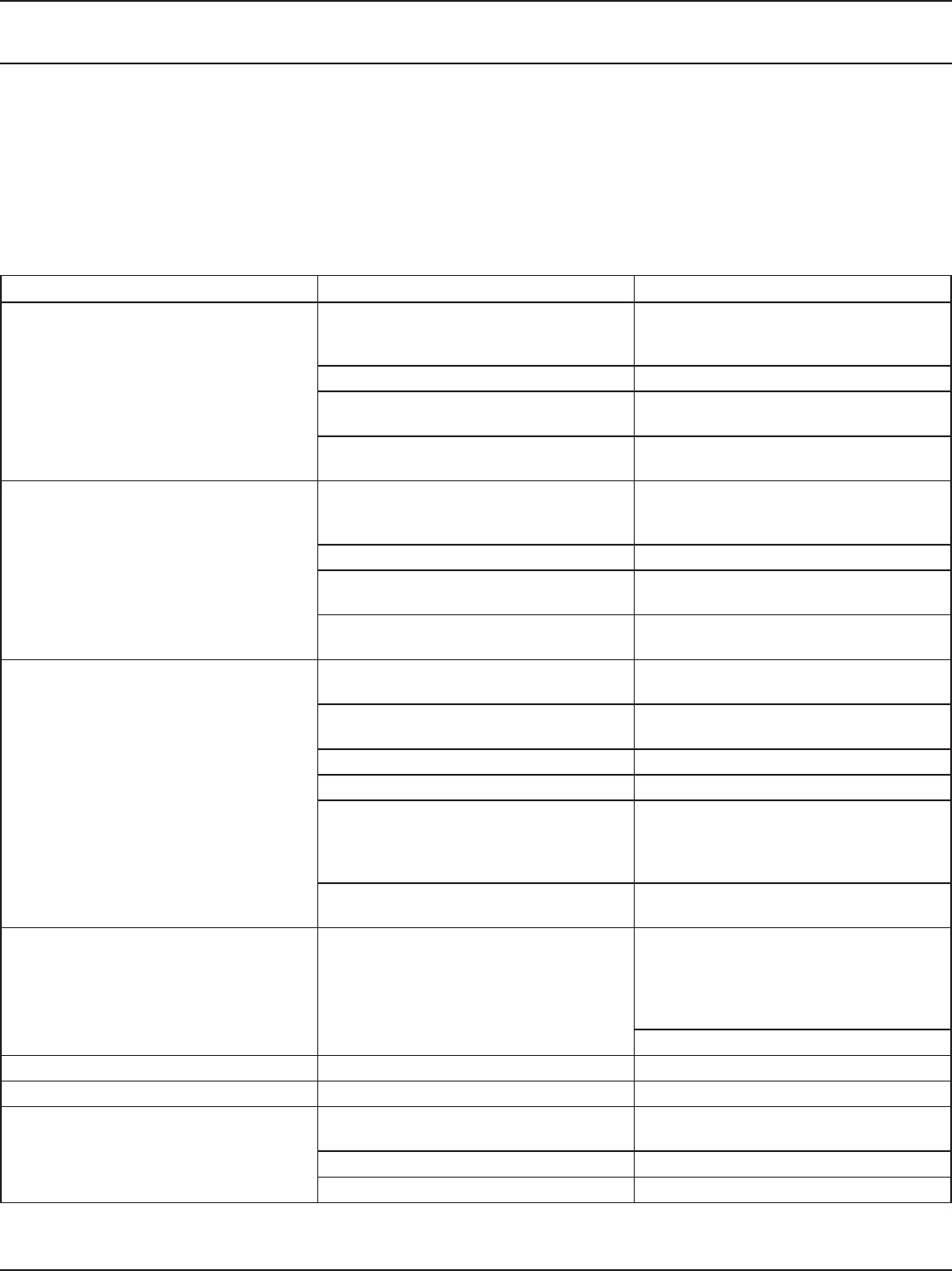
15
TROUBLESHOOTING
PROBLEM CAUSE SOLUTION
Drill does not run.
Power unit not functioning
Check power unit for proper fl ow and
pressure (7-9 gpm/26-34 lpm, 1500-2000
psi/104-140 bar).
Couplers or hoses blocked. Remove restriction.
Flow direction reversed. Pressure and
return lined hoses reversed at ports.
Be sure hoses are connected to their
proper ports..
Mechanical failure of piston or automatic
valve.
Disassemble drill and inspect for damaged
parts.
Drill does not drill effectively.
Power unit not functioning.
Check power unit for proper fl ow and
pressure (7-9 gpm/26-34 lpm, 1500-2000
psi/104-140 bar).
Couplers or hoses blocked. Remove restriction.
Low accumulator charge (pressure hose
will pulse more than normal).
Recharge accumulator. Replace dia-
phragm if charge loss continues.
Oil too hot (above 140° F/60° C).
Provide cooler to maintain proper oil tem-
perature.
Drill operates slow.
Low fl ow supply from power unit.
Check power unit for proper fl ow (7-9
gpm/26-34 lpm).
High backpressure.
Check hydraulic system for excessive
backpressure (over 250 psi/17 bar).
Couplers or hoses blocked. Remove restriction.
Orifi ce plug or internal passage blocked. Remove restriction.
Oil too hot (above 140° F/60° C) or too
cold (below 60° F/16° C).
Check power unit for proper oil tempera-
tures. Bypass cooler to warm oil up or
provide cooler to maintain proper tempera-
ture.
Relief valve set too low.
Adjust relief valve to 2100-2250 psi/145-
155 bar.
Drill gets hot.
Hot oil going through tool.
Check power unit. Be sure fl ow rate is
not too high causing part of the oil to go
through the relief valve. Provide coooler
to maintain proper oil temperature (140°
F/60°C maximum).
Check relief valve setting.
Oil leakage on drill bit. Lower piston or drive hex seal failure. Replace seals.
Oil leakage around trigger. Valve spool seal failure. Replace seals.
Low rotation torque.
Motor not completely broken in.
Continued operation or break in with motor
break-in block will correct.
Damage to motor clearences. Repair as required.
Mechanical binding during drilling. Take care to guide drill straight.
If symptoms of poor performance develop, the following
chart can be used as a guide to correct the problem.
When diagnosing faults in operation of the hammer drill,
always check that the hydraulic power source is supply-
ing the correct hydraulic fl ow and a pressure to the tool as
listed in the table. Use a fl owmeter known to be accurate.
Check the fl ow with the hydraulic fl uid temperature at least
80
o
F / 27
o
C.