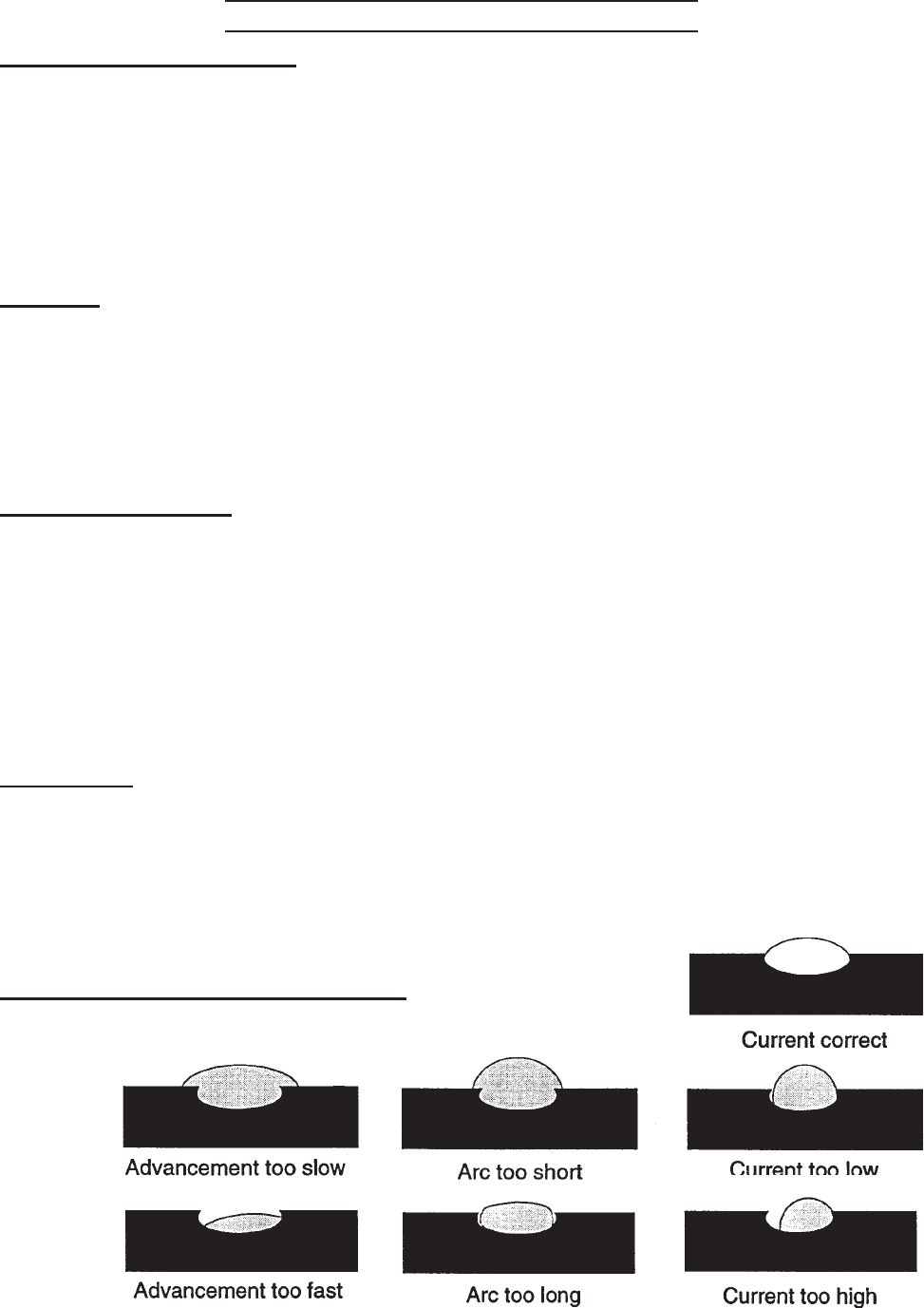
Page 14- SKU: 98870
Troubleshooting Arc Welding Defects
Porosity and Surface Holes
Most porosity cannot be seen, but serious porosity weakens the weld.
Before welding, remove all surface contaminants, such as Mill Scale, Rust, Paint,
Dirt, Grease, or Moisture.
Keep the weld puddle molten for a longer period, allowing time for gasses to escape.
Steel with an extra low Manganese or Carbon content, or with a high percentage of
Sulfur or Phosphorous will need to be welded using an E7018 rod.
Use a shorter arc length electrode, such as E7018.
Undercut
Undercutting appears as slight scratches at the bead edges. Under certain conditions it can
seriously decrease the weld strength.
Reduce the Amperage, travel speed, or electrode diameter until the puddle size be-
comes manageable.
Adjust the Electrode angle so the Arc Force holds the metal in the corners.
Use a uniform travel speed, and avoid excessive weaving.
Weld Material Spatter
Spattering does not inuence weld strength, but is considered an appearance defect.
Lower the current, check the specied range for the electrode being used.
Be sure you are using the correct polarity.
Try to minimize the arc length.
Look for Arc Blow conditions. Note: Arc Blow generally occurs only when using a DC
welder. This is an AC welder.
Wet or moist ux or workpiece may cause splatter. Note: Wet electrodes may be
dried by baking at 300° F until the moisture is gone, usually in 1-2 hours.
Poor Fusion
Poor Fusion is bad bonding of the weld metal to any part of the work piece. This must be
corrected, since it results in a weak weld joint.
Increase the Amperage.
Clean the joint edges of dirt, rust, paint, or use an E6013 electrode.
Decrease the gap between the work pieces.
Use a weaving technique to better ll the gap.
Visual Inspection of the nished weld
Compare your weld joints to these drawings for suggestions on
achieving better welds.
1.
2.
3.
4.
1.
2.
3.
1.
2.
3.
4.
5.
1.
2.
3.
4.