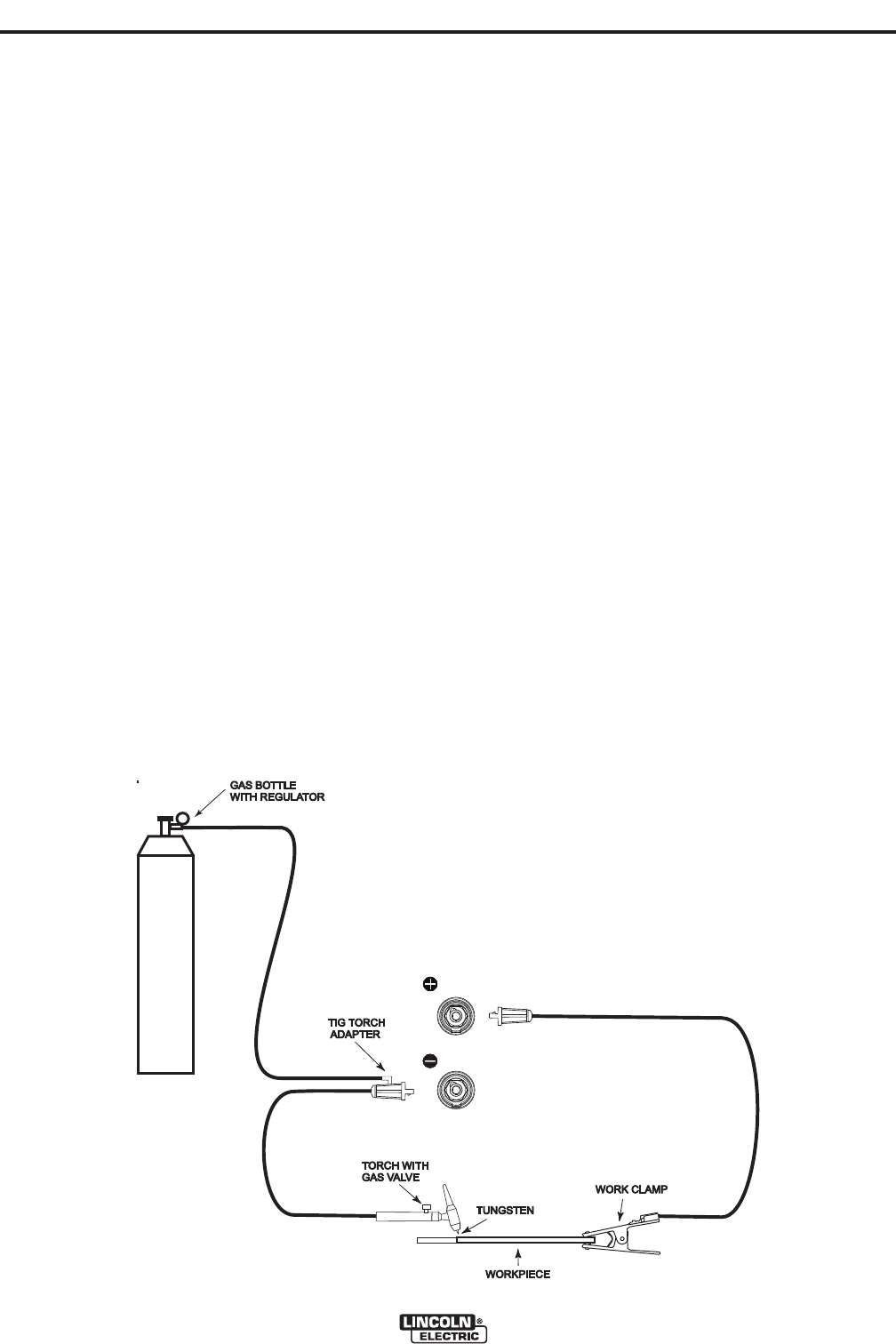
!"$&!
7. Once the electrode is burned down move the elec-
trode quickly from the weld to extinguish the arc.
8. Turn the machine off and remove the stub by open-
ing the jaws of the electrode holder and insert a
new electrode.
<A2 The welded work piece and electrode stub are
hot after welding. Allow them to cool down
before touching or use pliers to move. Always
make sure the welder is turned off before set-
ting down the Electrode Holder.
&) &' %& $& %
)
This machine is capable of direct current (DC) TIG
welding which is suitable for hard metals such as
steel, stainless steel, copper and brass. The TIG
process is good for welding thin materials requiring
very good cosmetic appearance with low heat input
and low spatter. TIG welding uses a tungsten elec-
trode which delivers electrical current to the work
piece by way of an electric arc. Unlike stick welding in
which the electrode is consumed in the arc, the tung-
sten electrode is not consumed. Instead filler metal is
added to the weld by manually dipping a filler rod into
the weld puddle. TIG welding requires a higher skill
level than stick welding and practice is required to
master the technique. For best results a TIG welding
class is suggested or obtaining a book on how to TIG
weld.
($&M%
TIG welding also requires 100% Argon shielding gas
to shield the arc, preventing porosity in the weld. This
is different than stick welding which has a coating on
the electrode to produce its own shielding. In addition,
a gas regulator, a manual gas valve TIG torch, torch
parts kit, torch adapter and filler metal are required.
Refer to the accessories section of this manual for an
appropriate optional TIG torch, parts kit and torch
adapter. A gas regulator, filler metal and a bottle of
shielding gas are readily available from a welding gas
distributor.
See Figure B.7 shows the basic TIG welding setup:
'$