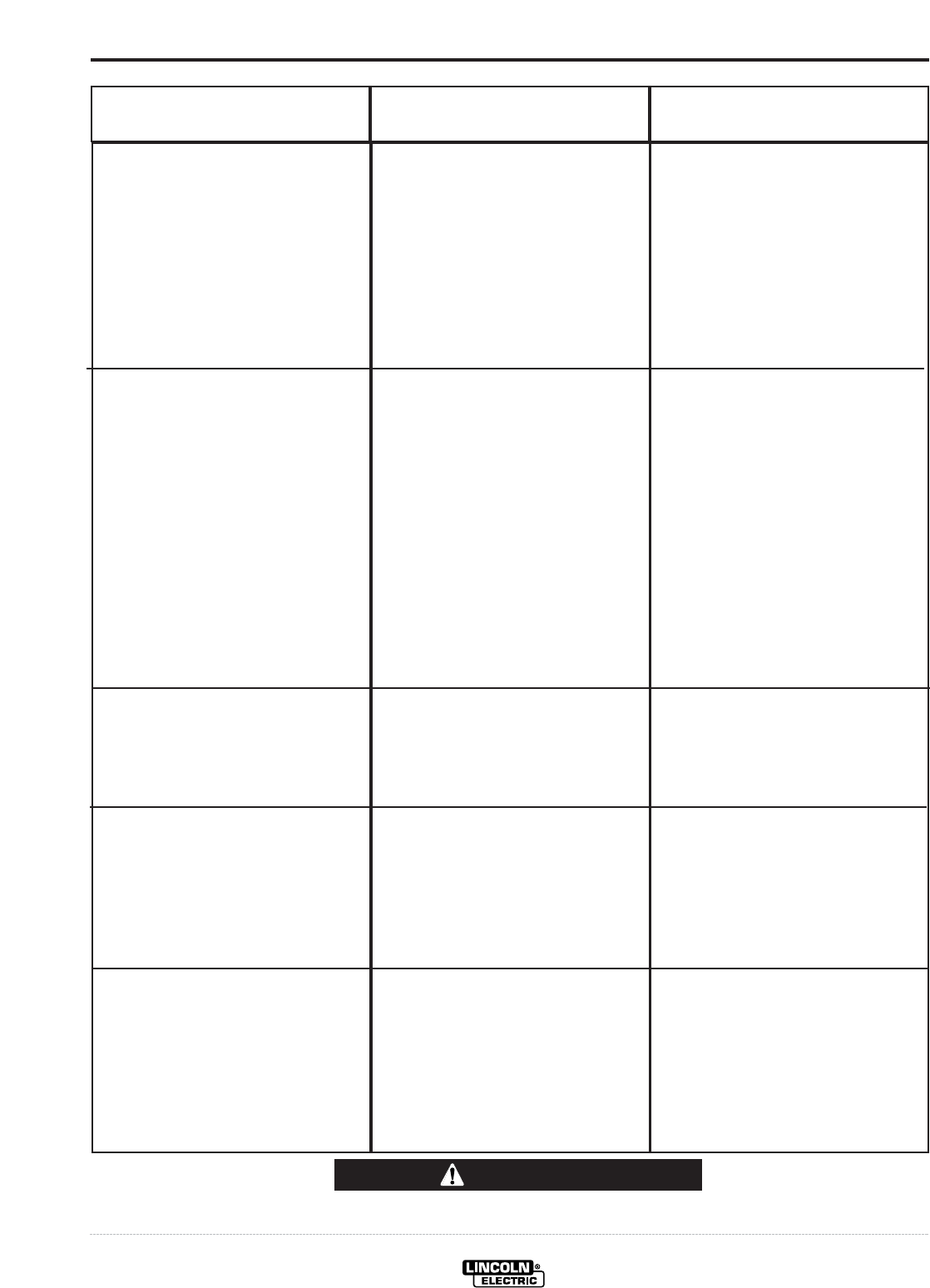
D-2
TROUBLESHOOTING
D-2
800 AMP TANDEM MIG TORCH
Observe all Safety Guidelines detailed throughout this manual
If for any reason you do not understand the test procedures or are unable to perform the tests/repairs safely, contact your
Local Lincoln Authorized Field Service Facility for technical troubleshooting assistance before you proceed.
CAUTION
PROBLEMS
(SYMPTOMS)
POSSIBLE
CAUSE
RECOMMENDED
COURSE OF ACTION
The drive rolls turn, but wire will
not feed or wire feeding is rough.
Porosity in the weld.
There is arcing in the nozzle.
The welding arc is inconsistent.
Inconsistent wire feeding.
1. Torch cable is kinked and /or twisted.
2. Wire jammed in torch or cable.
3. Incorrect or worn drive rolls and guide
tubes.
4. Partially flashed, melted or improper
contact tip size.
1. Welding surface is contaminated.
2. Insufficient gas coverage.
3. Excessive arc length.
4. Inoperative gas solenoid.
5. Contaminated shielding gas.
6. Excessive use of anti-spatter fluid.
1. Spatter build-up is bridging between
the nozzle and the contact tips, or
from contact tip to contact tip.
2. The torch is not insulated from part
tooling or fixture.
1. Worn or loose contact tip.
2. Loose connection in current path.
3. The wire conduit or liner is dirty or
worn.
1. Loose, worn or incorrect drive rolls.
2. Torch cable kinked or liner worn.
3. Wire pay-off dispenser malfunction-
ing.
1. Keep cable assembly as straight as
possible. Inspect cable and replace if
necessary.
2. Check for any obstructions in cable
assembly. Check liner, replace if nec-
essary.
3. Be sure the wire diameter being used
matches the drive rolls and guide
tubes size.
4. Replace contact tip.
1. Remove dirt, oil, moisture, mill scale
and miscellaneous contamination
from part.
2. Check for sufficient shielding gas flow
form source, or restriction in gas line.
Check for drafts that may force
shielding gas from welding arc.
3. Check weld procedures, arc length
should generally be less than 1/4"
and steady.
4. Check solenoid operation.
5. Check for leaks in gas hoses and gas
hose connections.
6. Check amount of anti-spatter being
applied and accumulation in nozzle.
1. Remove spatter build-up on regular
basis. Adjust weld procedure to
reduce spatter.
2. Make sure torch is properly insulated.
1. Inspect contact tip, tighten and
replace if necessary.
2. Check electrode and work cable con-
nections. Check torch connections at
wire feeder, diffuser and goosenecks.
3. Clean liner and conduit. Replace if
necessary.
1. Inspect drive rolls, tighten, clean or
replace as necessary.
2. Check cable for severe bends or
kinking. Check, and clean liner as
neccesary.
3. Check dispenser, make sure moving
parts are free from obstruction and
welding wire is properly routed.