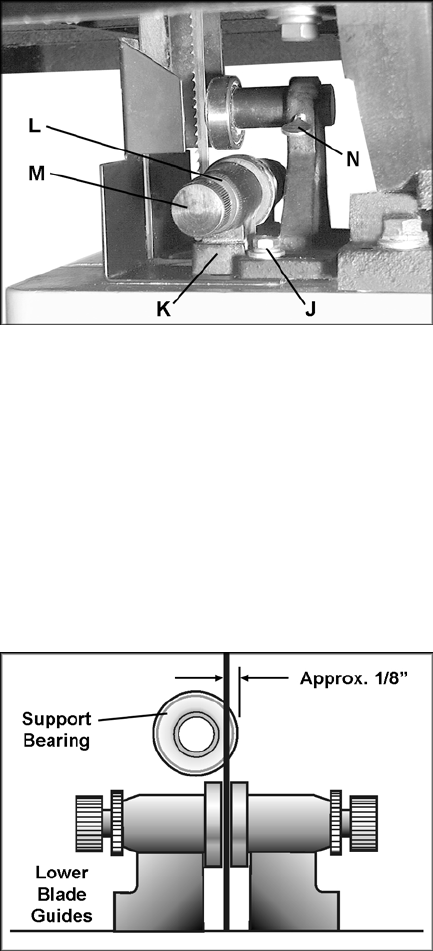
19
12. Adjust the support bearing until it lightly
contacts the dollar bill.
13. When support bearing adjustment is
complete, remove dollar bill and tighten nut
(E, Figure 19).
Lower Blade Guides and Lower
Support Bearing
1. Disconnect machine from power source.
2. Blade must already be tensioned and
tracking properly.
3. Loosen two hex cap screws (J, Figure 20).
4. Adjust the guide bracket (K, Figure 20) so
that the front of the guide wheels are just
behind the blade’s gullet (curved area at the
base of the tooth).
5. Tighten the two hex cap screws (J, Figure
20).
6. Loosen lock ring (L, Figure 20) on the guide
wheel assembly.
7. Rotate the knob (M, Figure 20) until the
guide wheel rests lightly against the blade.
Do not force the guide wheel against the
side of the blade.
8. Tighten the lock ring (L, Figure 20).
9. Repeat this adjustment for the guide wheel
on the opposite side.
10. Loosen thumb screw (N, Figure 20).
11. Slide the shaft of the support bearing until
the space between the support bearing and
the back edge of the blade is approximately
1/64”. A convenient way to achieve this
spacing is by placing a dollar bill folded
twice (four thicknesses of a dollar bill is
approximately 1/64”) between blade and
support bearing.
12. Adjust the support bearing until it lightly
contacts the dollar bill.
13. The bearing holder on the shaft is eccentric.
Rotate the support bearing until the back
edge of the blade overlaps the front face of
the support bearing by approximately 1/8”.
See Figure 21.
14. When adjustments to the support bearing
are complete, tighten thumb screw (N,
Figure 20).
Figure 20
Figure 21