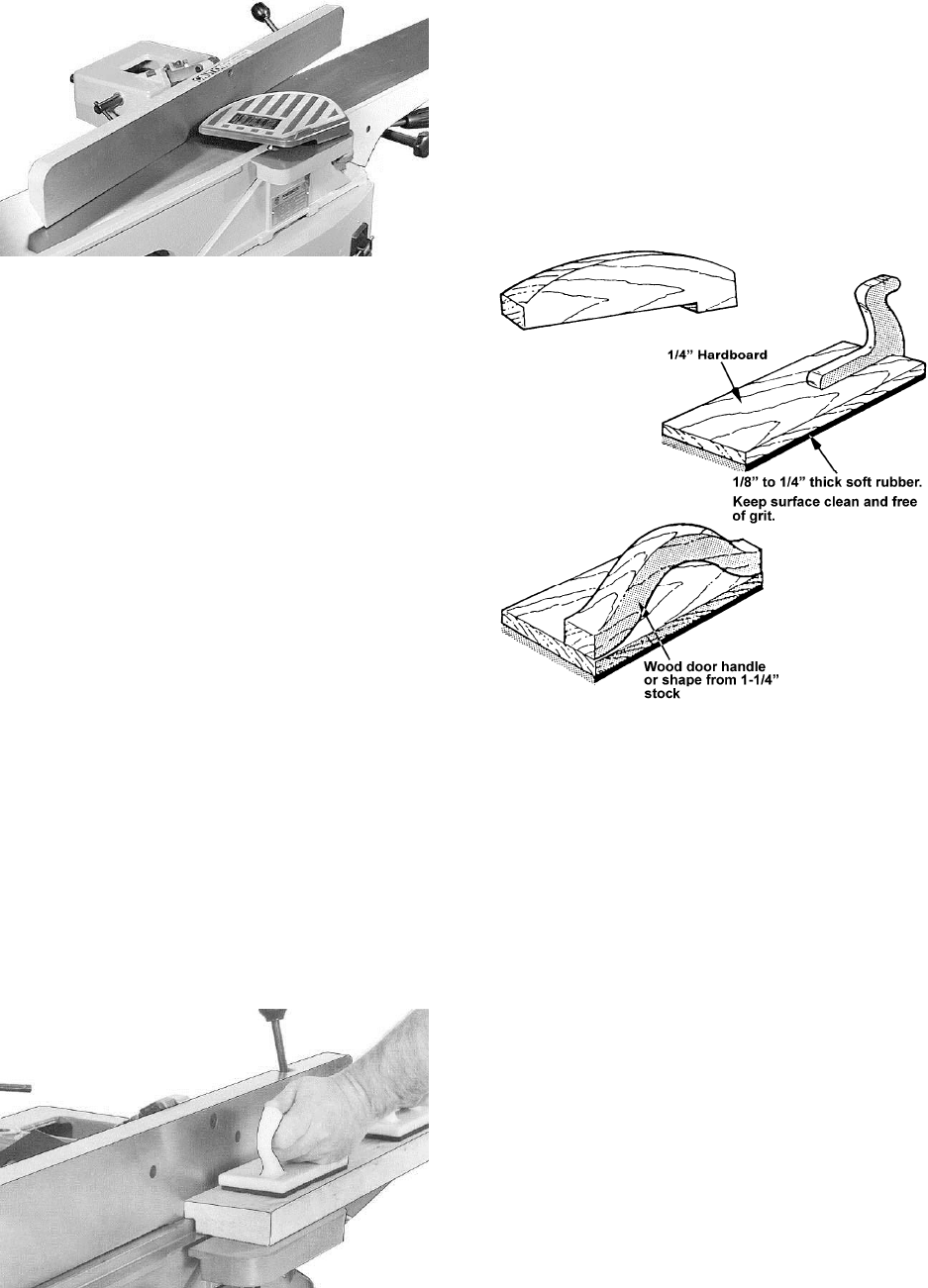
26
Figure 42
Rabbet Cuts (Straight Knife only)
IMPORTANT: Rabbeting can be done with the
straight knife cutterhead only; it is not applicable
with the helical cutterhead model.
A rabbet is a groove cut along the edge of a
board (Figure 43). It is usually made to accept
another board to form a strong, simple joint.
Note: The maximum rabbet depth is 1/2".
1. Unplug the jointer and remove the
cutterhead guard.
2. Loosen the fence and slide it to the
rabbeting edge. Set the fence to the desired
width of the rabbet and lock down.
3. Inspect stock for soundness and grain
direction.
4. Place stock on the infeed table and rabbet
table with the edge to be rabbeted firmly
against the fence.
5. Slowly and evenly feed stock through the
cutterhead.
6. Lower the infeed table 1/16" at a time and
make successive cuts until the desired
depth of rabbet is obtained.
7. Re-install the cutterhead guard when
finished with rabbeting operations.
Figure 43
Push Blocks
Push blocks are simple yet necessary tools to
assist the operator, especially when jointing thin
or short stock. Illustrated in Figure 44 are three
types of push blocks commonly used in jointing.
Push blocks may be obtained commercially or
easily constructed.
Note: The 54A Jointer is supplied with two push
blocks for feeding stock.
Figure 44
Maintenance
Blade Care
Blades are extremely sharp! Use caution
when cleaning or changing. Failure to
comply may cause serious injury!
When gum and pitch collect on the blades,
carefully remove with a strong solvent. Failure to
remove gum and pitch build up may result in
excessive friction, blade wear and overheating.
When blades become dull, turn them to the new
edge, or replace them.
Lubrication
Use a good grade of light grease on the
steel adjusting screws located in the raising
and lowering mechanisms of the work
tables.
Occasionally, apply a few drops of light
machine oil to the infeed/outfeed gibs. This
permits the tables to slide freely.
The cutterhead ball bearings are lifetime
lubricated and need no further care.