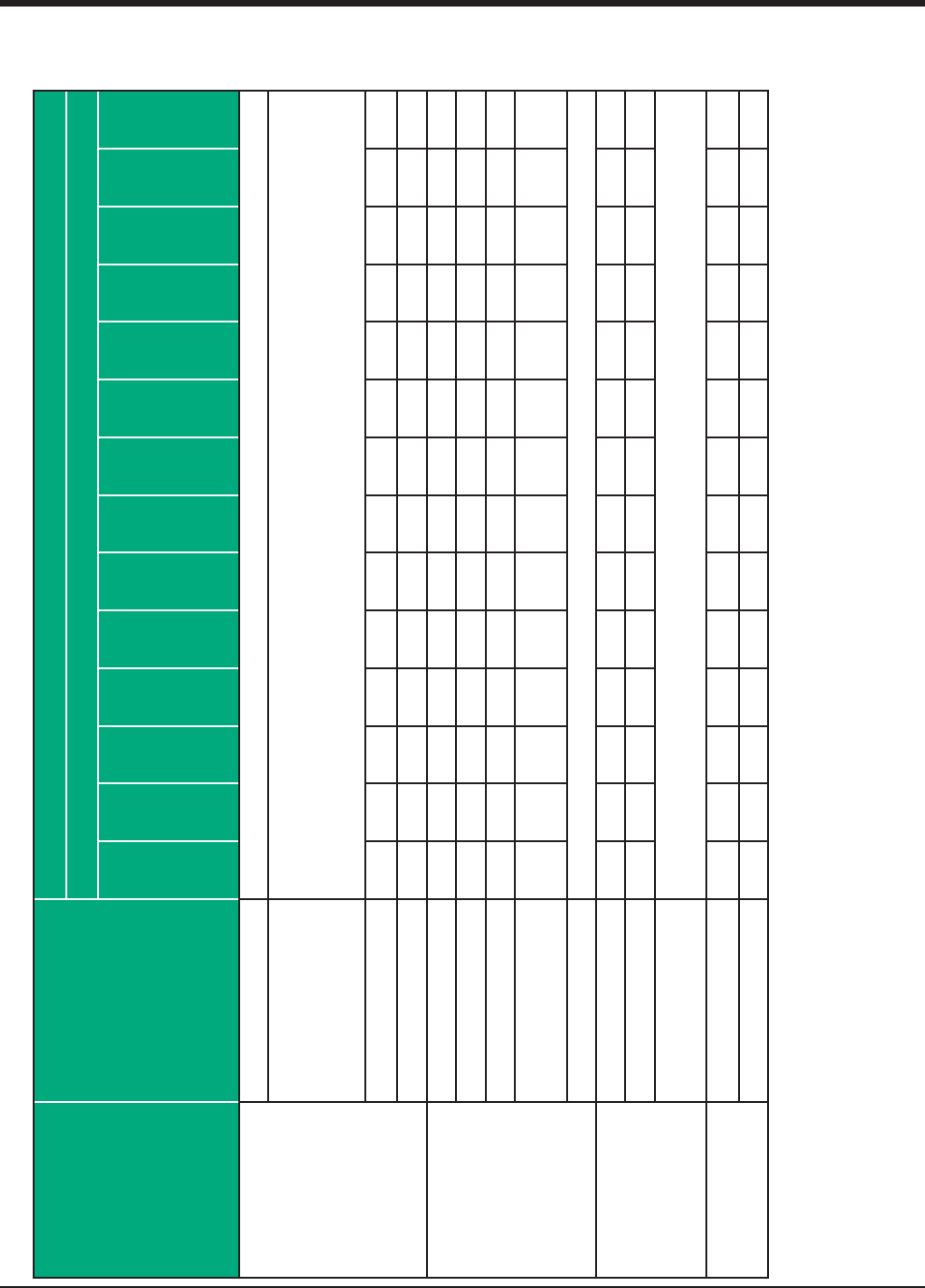
5 – 1
VSG/VSSG • Installation, Operation and Maintenance Manual •Vilter/Emerson • 35391SSG
Maintenance and Service Schedule
Follow this table for maintaining and servicing the compressor unit at hourly intervals.
Table 5-1. Maintenance/Service Schedule
Section 5 • Maintenance/Service
Group
Inspection/
Maintenance
(2)
Service Interval (Hours)
(
¹
)
(Based on dry clean gas)
200
2,500
5,000
10,000
15,000
20,000
25,000
30,000
35,000
40,000
45,000
50,000
55,000
60,000
Oil Circuit
Oil Change Replace oil based on oil analysis report or visual contamination.
Oil Analysis
Oil sampling is recommended every 2 to 3 months for the fi rst year. Thereafter, as required, increase
sampling time period if contamination of oil is unlikely or decrease sampling time period if contami-
nation of oil is evident. Take an oil sample any time during operation If there’s reason to believe that
the oil is contaminated. For additional information on oil, refer to Oil and Oil Flow operation.
Oil Filters
(3)
----R--R--R--R
Oil Strainer IIIIIIIIIIIIII
Compressor
Unit
Coalescing Filter ----R--R--R--R
Coalescing Drain Line IIIIIIIIIIIIII
Suction Screen I - - I - I - I - I - I - I
Coupling Alignment
and Integrity
IIIIIIIIIIIIII
Motor (Compressor) See Motor Manual for proper lubrication procedures and service intervals.
Control
Calibration
Transducers IIIIIIIIIIIIII
RTDs IIIIIIIIIIIIII
Slide Valve Motors
Slide valve calibration should be inspected monthly. Inspections can be performed through the
control panel. If a Non-Movement Alarm appears, calibrate immediately.
Compressor
(4) (5)
Compressor
(6)
-I-I-I-I-I-I-I
Bearings -------------I
I = Inspect S = Sampling R = Replace
(1) Vilter recommends that a Preventative Maintenance Program be developed by Vilter GC (Gas Compression) Service Center.
(2) Daily records should be kept on suction, discharge, oil pressures & temperatures, along with ensuring Temp Leaving Oil Separator is above Dew Point.
(3) Replace oil fi lters when pressure drop reaches 7 PSID (maximum allowable pressure drop is 15 PSID).
(4) The life of the compressor will be increased by purging the compressor unit with dry nitrogen or sweet, dry natural gas at shutdown.
(5) Header drains should periodically be drained for liquid build-up to prevent compressor damage, see Piping in Section 3.
(6) Inspections include: gate rotor inspection, backlash measurement, shelf clearance, end play measurement (main rotor & gate rotor), gate rotor fl oat, slide valve inspection.