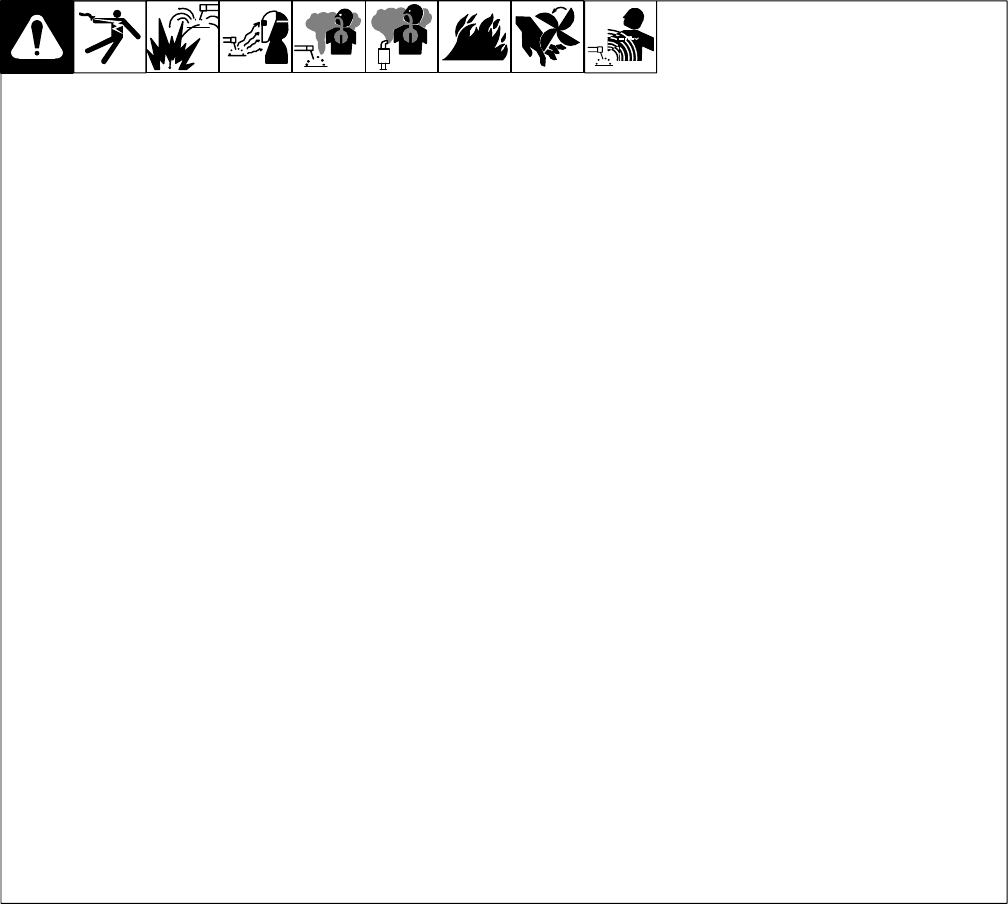
OM-474 Page 19
5-2. Description Of Front Panel Controls (See Section 5-1)
.
This unit has a max OCV control circuit
that resets Amperage/Voltage Adjust
Control R1 to maximum when the arc
breaks. When an arc is struck, weld out-
put control returns to the R1 front panel or
combination front panel/remote control
setting. The Amperage/Voltage Adjust
control adjusts amperage only when
constant current (CC) welding and does
not adjust open-circuit voltage. The max
OCV control circuit does not function
when constant voltage (CV) welding
(optional).
1 Ampere Range Switch
Y Do not switch under load.
Use switch to select weld amperage range.
For most welding applications, use lowest am-
perage range possible to help prevent arc out-
ages. When using MIG (CV) mode (optional),
place switch in maximum position.
2 Amperage/Voltage Adjust Control
Control adjusts amperage within range se-
lected by Ampere Range switch. Weld output
would be 148 A DC with controls set as shown
(50% of 85 to 210 A).
3 Amperage/Voltage Adjust Switch
(Optional)
Use switch to select front panel or remote am-
perage control (see Section 5-3).
For front panel control, place switch in Panel
position. For remote control, place switch in
Remote position and connect remote control
to Remote 14 receptacle RC3 or terminal strip
3T.
4 Output (Electrode) Control Switch
(Optional)
Use switch to control remote contactor con-
nected to receptacle RC3 or terminal strip 3T
(see Sections 4-7 and 4-8).
Y Weld output terminals are energized
when Output (Electrode) switch is On
(Hot) and engine is running.
For weld output, place switch in the On (Hot)
position. Open-circuit voltage is present at the
weld output terminals whenever engine is
running.
For remote output control, place switch in Re-
mote position. Open-circuit voltage is present
at the weld output terminals when remote con-
tactor switch is closed.
5 Process Switch (Optional)
Use switch to select Stick or MIG (CV) weld
output. Use Stick for Stick (SMAW) welding.
Use MIG (CV) for wire feed processes (MIG,
FCAW). If using MIG (CV), place Ampere
Range switch in maximum position. To en-
sure wire feeder reliability and improve arc
starting, unit does not run at idle speed
when operated in MIG (CV) mode.
. Place Process switch in Stick position
when using optional auxiliary power plant.
6 DC Voltmeter (Optional)
7 DC Ammeter (Optional)
8 Magnetic Shutdown Switch
Use switch during start-up to bypass engine
shutdown system. System stops engine if oil
pressure is too low or coolant temperature is
too high.
9 Glow Plug Time Table
Use table to find correct glow plug operating
time for different temperatures.
10 Engine Control Switch
Use switch to start engine, operate glow
plugs, select engine speed, and stop engine.
In Run position, engine runs at weld/power
speed. In Run/Idle position, engine runs at idle
speed at no load and weld speed with load ap-
plied. Turn to run position if using optional aux-
iliary power plant.
To Start: turn Engine Control switch to Start
while pressing Shutdown switch. Release En-
gine Control switch when engine starts, then
release Shutdown.
. If the engine does not start, let engine
come to a complete stop before attempt-
ing restart.
To Stop: turn Engine Control switch to Off
position.
11 Engine Hour Meter
12 Polarity And AC Selector Switch
(Optional)
Y Do not switch under load.
13 Battery Charging Warning Light
Light goes on if battery is not charging.
14 Low Oil Pressure/High Engine Tempera-
ture Warning Light
Light goes on if oil pressure is low or coolant
temperature is high.
Y Stop engine and fix trouble if either
warning light goes on.
15 Fuel Gauge
16 Engine Temperature Gauge (Optional)
Normal temperature is 180 - 200° F (81 - 93°
C). Stop engine if temperature exceeds 240°
F (116° C).
17 Engine Oil Pressure Gauge (Optional)
Normal pressure is 40 psi (276 kPa). Stop en-
gine if pressure is below 8 psi (55 kPa).