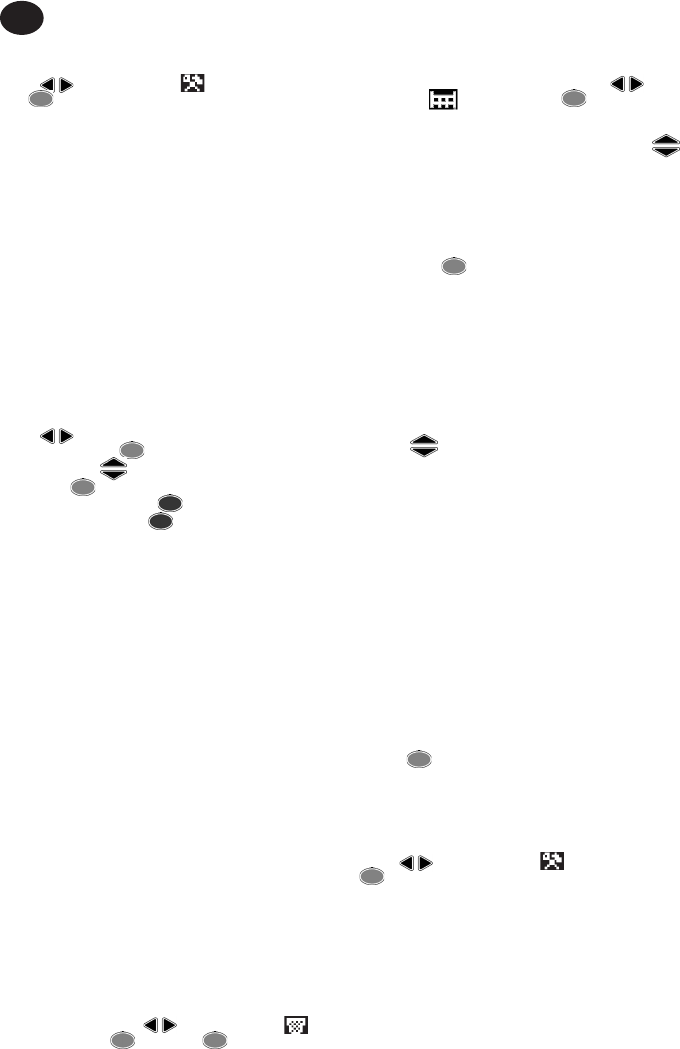
EN-9 04581922_ed4
EN
Torque Control Setup Menu:
Use the keys to highlight the Setup Icon and
press ENTER to access the Torque Setup Menu. This menu
allows the operator to change:
Samples - 1 to 30
Subgroups - 1 to 50
Units - lbin, lbft, Ncm, Nm, kgcm, kgm, ozin
Direction - Right or Left
Cycle End Time - 0.1s, 0.2s, 0.5s, 1.0s, 2.0s, 5.0s, 10.0s
Torque Threshold - 5% to 90% of tool’s maximum torque rating
Torque LSL - Torque Threshold +.01 to 100% of max -.01
Torque USL - Torque USL +.01 to 100% of max
Angle LSL - 0 degrees to Angle USL - 1
Angle USL - 1 to 3000 degrees
Trace Saved? - Yes or No
Cont. Output - Yes or No
Auto Print - Yes or No
Use the keys to scroll through the menu options (displayed
1 per screen), and press ENTER to edit. Menu options are
edited by using the keys to scroll through the options and
then pressing ENTER.
To exit without changing, press ESCAPE.
To exit from any screen, press ESCAPE.
Cycle End Time
When the applied torque is removed, the wrench does not
immediately store the data. Instead it waits for the Cycle End Time
to count down to zero. This allows time for the operator to adjust
grip or ratchet the wrench. The Cycle End Time can be altered in
Torque Control Mode Setup.
Auto Print
The Auto Print feature allows the wrench to directly output
measurements to a printer or PC as they are taken. The information
appears as a single line of text showing the: date, time, peak
torque, torque compared to specications, peak angle, angle
compared to specications, and direction of fastening. The
formatting and spacing will be dierent based upon the number of
columns the operator has chosen under Printer Setup.
Continuous Output
Setting the Cont. Output to “Yes” in peak measurement modes
causes the wrench to output fastener torque on a
second- by- second basis. This output can be sent to either a printer
or a PC using the supplied RS232 cable.
Trace saved?
Set “Trace saved?” to yes after a reading, to store it in the Expert
Wrench memory. A trace includes information about the
conguration used to take the reading as well as a table of torque
and angle values. The traces can be uploaded to a PC using the PC
Comms software (sold separately). Up to 10 traces can be saved
in memory.
Canceling a Reading
To discard a reading, use the keys to highlight the
Cancel Icon and press ENTER. Press ENTER again to
conrm when prompted ‘Cancel reading?’
View Statistics
To view statistics about previous readings, use the keys to
highlight the Stats Icon and press ENTER. This brings
you to a table of calculated values for Mean X, R, σ, Cp, Cpk, Cm,
Cmk, CAM derived from the recorded torque and angle data.
Dierent pages of the table can be viewed by pressing the
keys.
Angle Control
Angle Control mode monitors the nal tightening angle of a
fastener from a preset threshold torque and signals the operator
to stop tightening once that angle is within a specied range. To
access Angle Control mode, scroll to Angle Control in the Main
Menu and press ENTER. The screen will immediately display
the word “WAIT” and both LEDs will turn red. During this time the
wrench is zeroing the angle sensor. Hold the wrench still until a
single LED is lit yellow to proceed.
The default display shows torque units in large bold numbers in
the center of the screen, with angle data (as indicated by the angle
symbol on the left) above in a smaller font. The current torque units
are displayed alongside the torque data. The bottom left corner of
the screen says “ANGLE” to indicate the current tightening mode.
The bottom right hand corner shows the current cycle number/
total number of samples.
Using the keys, two other displays can be accessed. One
shows the angle data in larger font with the torque data smaller in
the middle. The other shows both torque and angle in small font,
with current subgroup/total subgroups on the bottom.
Tighten the fastener at a moderate speed using a steady pull
on the wrench handle. As the wrench is pulled, the LEDs will
change color to represent various conditions. Both LEDs will turn
solid green when the lower angle limit is passed. Both LEDs will
turn solid red when the upper torque limit is passed. When the
measurement is nished the wrench will beep and both LEDs will
start ashing.
The ashing LEDs give a quick analysis of the completed
tightening. The top LED represents the relative torque value. It will
ash yellow if the torque is below the specied range, green if it is
within, and red if it is above. In a similar fashion the lower LED will
ash to indicate whether the resultant angle was below, within,
or above the specied range. There are also arrows that appear to
the right of the torque and angle values. An upward arrow means
that the given value is above the specied range, and a downward
value means that it is below the range.
Press the ENTER key to zeroing the angle sensor for the next
reading.
Note: The previous results will remain on the display until the next
reading is taken.
Angle Control Setup Menu:
Use the keys to highlight the Setup Icon and press
ENTER to access the Angle Setup Menu. This menu allows the
operator to change:
Samples - 1 to 30
Subgroups - 1 to 50
Units - lbin, lbft, Ncm, Nm, kgcm, kgm, ozin
Direction - Right or Left
Cycle End Time - 0.1s, 0.2s, 0.5s, 1.0s, 2.0s, 5.0s, 10.0s
Torque Threshold - 5% to 90% of tool’s maximum torque rating
Torque LSL - Torque Threshold +.01 to 100% of max -.01
Torque USL - Torque USL +.01 to 100% of max.