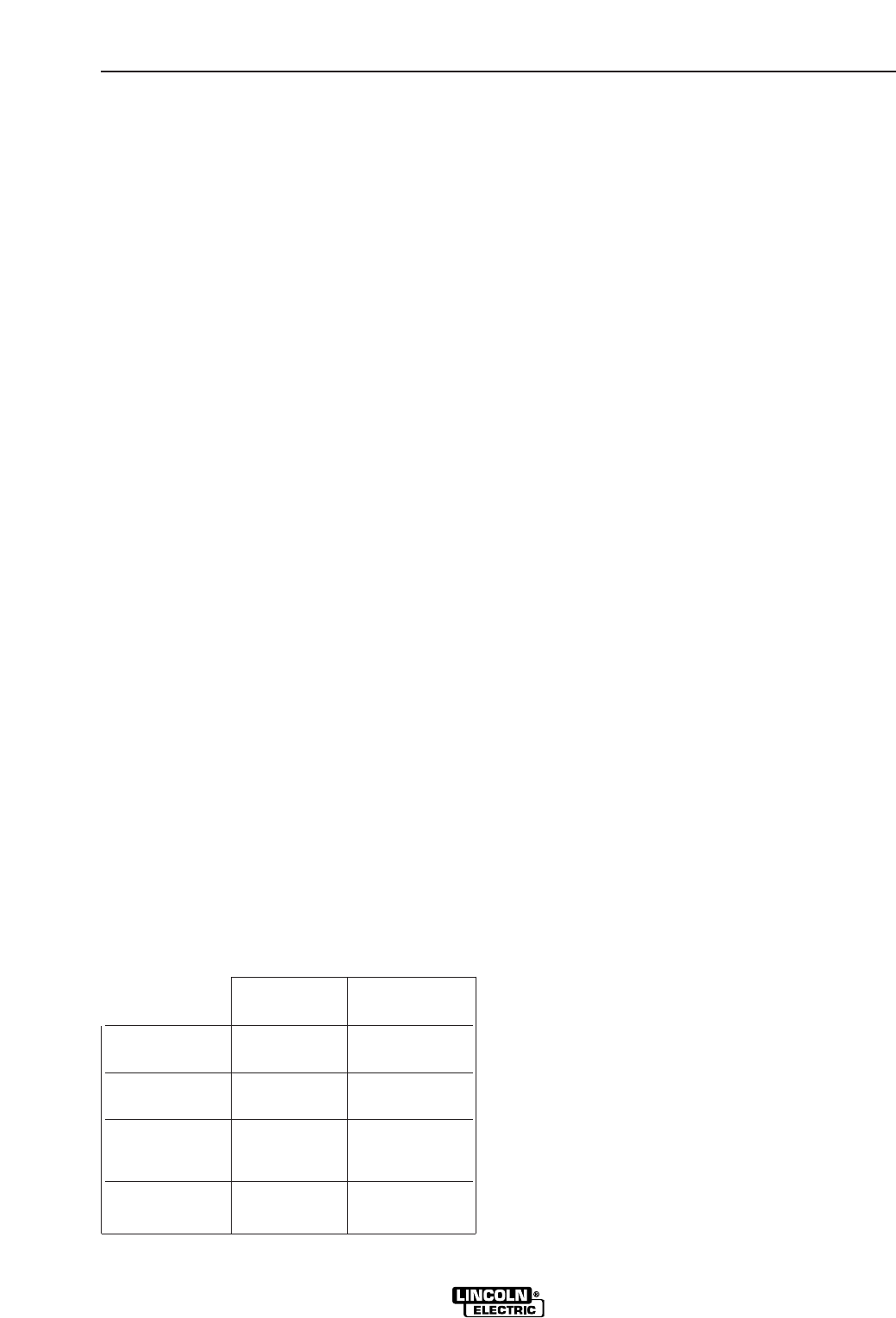
B-6 OPERATION B-6
Vantage 500 CUMMINS
BREAK-IN PERIOD
The engine used to supply power for your welder is a heavy duty,
industrial engine. It is designed and built for rugged use. It is very
normal for any engine to use small quantities of oil until the break-
in is accomplished. Check the oil level twice a day during the
break-in period. In general this takes 50 to 100 hours of
operation.
IMPORTANT
IN ORDER T
O ACCOMPLISH THIS BREAK-IN, THE UNIT
SHOULD BE SUBJECTED TO HEAVY LOADS, WITHIN THE
RATING OF THE MACHINE. AVOID LONG IDLE RUNNING
PERIODS.
ENGINE BREAK-IN
Lincoln Electric selects high quality, heavy-duty industrial engines
for the portable welding machines we offer. While it is normal to
see a small amount of crankcase oil consumption during initial
operation, excessive oil use, wetstacking (oil or tar like substance
at the exhaust port), or excessive smoke is not normal.
Larger machines with a capacity of 350 amperes and higher,
which are operated at low or no-load conditions for extended
periods of time are especially susceptible to the conditions
described above. To accomplish successful engine break-in,
most diesel-powered equipment needs only to be run at a
reasonably heavy load within the rating of the welder for some
period of time during the engine’s early life. However, if the
welder is subjected to extensive light loading, occasional
moderate to heavy loading of the engine may sometimes be
necessary. Caution must be observed in correctly loading a
diesel/generator unit.
1. Connect the welder output studs to a suitable
resistive load bank. Note that any attempt to short
the output studs by connecting the welding leads
together, direct shorting of the output studs, or
connecting the output leads to a length of steel will
result in catastrophic damage to the generator and
voids the warranty.
2. Set the welder controls for an output current and
voltage within the welder rating and duty cycle.
Note that any attempt to exceed the welder rating or
duty cycle for any period of time will result in
catastrophic damage to the generator and voids the
warranty.
3. Periodically shut off the engine and check the
crankcase oil level.
TYPICAL FUEL CONSUMPTION
Refer to Table B.2 for typical fuel consumption of the Vantage’
Engine for various operating scenarios.
WELDER OPERATION
DUTY CYCLE
Duty Cycle is the ratio of the uninterrupted on-load duration to 10
minutes. The total time period of one complete on-load and no-
load cycle is 10 minutes. For example, in the case of a 60% duty
cycle, load is applied continuously for 6 minutes followed by a no-
load period of 4 minutes.
STICK WELDING MODE
The Vantage can be used with a broad range of DC stick
electrodes.
The MODE switch provides two stick welding settings as follows:
CC-STICK MODE
The CC-STICK position of the MODE switch is designed for
horizontal, vertical-up and over head welding with all types of
electrodes, especially low hydrogen. The OUTPUT CONTROL
knob adjusts the full output range for stick welding.
The ARC CONTROL knob sets the short circuit (arc-force) current
during stick welding. Increasing the number from -10 (Soft) to +10
(Crisp) increases the short circuit current and prevents sticking of
the electrode to the plate while welding. This can also increase
spatter. It is recommended that the ARC CONTROL be set to the
minimum number without electrode sticking. Start with the knob
set at 0.
DOWNHILL PIPE MODE
This slope controlled setting is intended for “out-of-position” and
“down hill” pipe welding where the operator would like to control
the current level by changing the arc length. The OUTPUT
CONTROL knob adjusts the full output range for pipe welding.
The ARC CONTROL knob sets the short circuit current (arc-force)
during stick welding to adjust for a soft or a more forceful digging
arc (Crisp). Increasing the number from -10 (Soft) to +10 (Crisp)
increases the short circuit current which results in a more forceful
digging arc. Typically a forceful digging arc is preferred for root
and hot passes. A softer arc is preferred for fill and cap passes
where weld puddle control and deposition (“stacking” of iron) are
key to fast travel speeds. It is recommended that the ARC
CONTROL be set initially at 0.
TOUCH START TIG MODE
The Vantage can be used in a wide variety of DC TIG welding
applications.
The TOUCH START TIG setting of the MODE switch is for DC
TIG (Tungsten Inert Gas) welding. To initiate a weld, the
OUTPUT CONTROL knob is first set to the desired current and
the tungsten is touched to the work. During the time the tungsten
is touching the work there is very little voltage or current and, in
general, avoids tungsten contamination. Then, the tungsten is
gently lifted off the work in a rocking motion, which establishes the
arc.
To stop the arc, simply lift the TIG torch away from the work piece.
When the arc voltage reaches approximately 30 volts, the arc will
go out and the machine will automatically reset to the touch start
current level. The tungsten may then be retouched to the work
piece to restrike the arc. The arc may also be started and stopped
with an Amptrol or Arc Start Switch.
The ARC CONTROL is not active in the TIG mode.
Table B.2
Cummins B3.3 Engine Fuel Consumption
Cummins B3.3 Running Time for
56HP(42Kw) 25GAL.(94.6L)
@1800 RPM (Hours)
Low Idle - .45 Gal./hour 55.6
no load 1425 RPM (1.7 Lts./hour)
High Idle - .81 Gal./hour 30.9
no load 1900 RPM (3.1 Lts./hour)
DC CC Weld 1.88 Gal./hour 13.3
Output 500 (7.1 Lts./hour)
Amps @ 40 Volts
Auxiliary Power 1.23 Gal./hour 20.3
12,000 VA (4.7 Lts./hour)