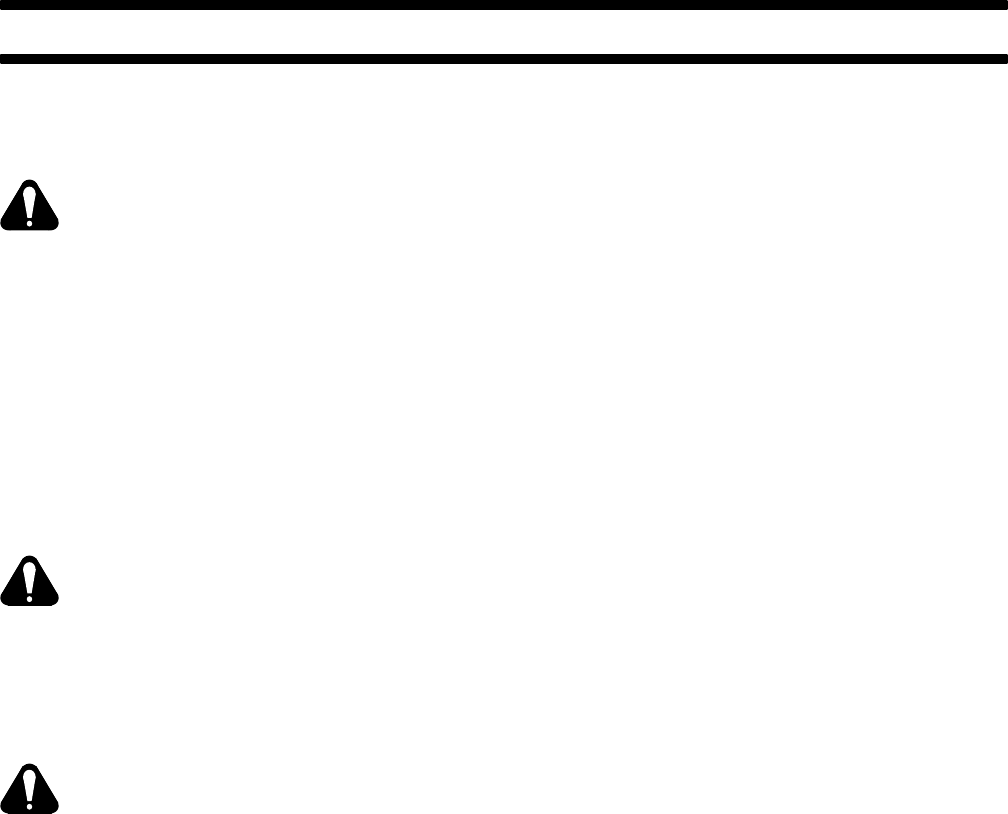
OM-533 Page 8
SECTION 5 – MAINTENANCE & TROUBLESHOOTING
5-1. MAINTENANCE
Usage
and shop conditions will determine the frequency
and
type of maintenance. Inspect equipment as follows:
WARNING: ELECTRIC SHOCK can kill.
•
Do not touch live electrical parts.
•
Shut down welding power source, and dis-
connect
remote control before inspecting, main
-
taining, or servicing unit. Power to the remote
control
should be disconnected before
attempt
-
ing repair or replacement of internal compo-
nents.
1. Inspect interconnecting cord for damage to or
breaks in the insulation jacket, particularly at the
plugs. Repair or replace cord as necessary.
2. Remove
grease
and grime from components; mois
-
ture from electrical parts and cable.
5-2. TROUBLESHOOTING
WARNING: ELECTRIC SHOCK can kill.
•
Do not touch live electrical parts.
•
Shut down welding power source, and dis-
connect
remote control before inspecting, main
-
taining, or servicing unit. Power to the remote
control
should be disconnected before
attempt
-
ing repair or replacement of internal compo-
nents.
CAUTION: ELECTROSTATIC DISCHARGE
(ESD) can damage circuit boards.
•
Put on properly grounded wrist strap BE-
FORE handling circuit boards.
•
Transport circuit boards in proper static-
shielding carriers or packages.
•
Perform
work only at a static-safe work area.
INCORRECT INSTALLATION or misaligned
plugs can damage circuit board.
•
Be sure that plugs are properly installed and
aligned.
EXCESSIVE PRESSURE can break circuit
board.
•
Use
only minimal pressure and gentle move
-
ment when disconnecting or connecting board
plugs and removing or installing board.
A. General
It is assumed that proper installation has been made,
according
to
Section 2 of this manual, and that the unit
has been functioning properly until trouble developed.
B. Troubleshooting
Troubleshooting to be performed only by qualified per-
sons.
The following information is supplied to diagnose and
provide
remedies for some of the troubles that may
de
-
velop
in
this unit. Check welding power source Owner
’s
Manual
for possible problems caused
by welding power
source malfunctions.
Use this information in conjunction with the circuit dia-
gram while performing troubleshooting procedures. If
the trouble is not remedied after performing these pro-
cedures, the nearest Factory Authorized Service Sta-
tion/Service Distribuitor should be contacted. In all
cases of equipment malfunction, the manufacturer’s
recommendations should be strictly followed.
Problems with this unit fall into four categories:
1. Front panel components
2. Circuit board PC5
3. Interconnecting cable
4. Welding power source.
If everything on the remote control functions except a
particular
switch, meter
, or control, the problem can be
attributed to a broken component. Replace the broken
component.
If
the problem is still present,
replace PC5. If the remote
control
is entirely non-functional, replace
PC5. If erratic
conditions occur and the welding power source was
working properly, replace PC5.
A
break in the
interconnecting cable can interrupt power
or
command signal between welding power source
and
remote
control. Replace interconnecting cable
if lack of
continuity is suspected.
Printed circuit board PC1 in the welding power source
sends
and receives signals from the remote control. If
all
other components of the system are functioning, re-
place welding power source PC1 according to instruc-
tions in welding power source Owner’s Manual.