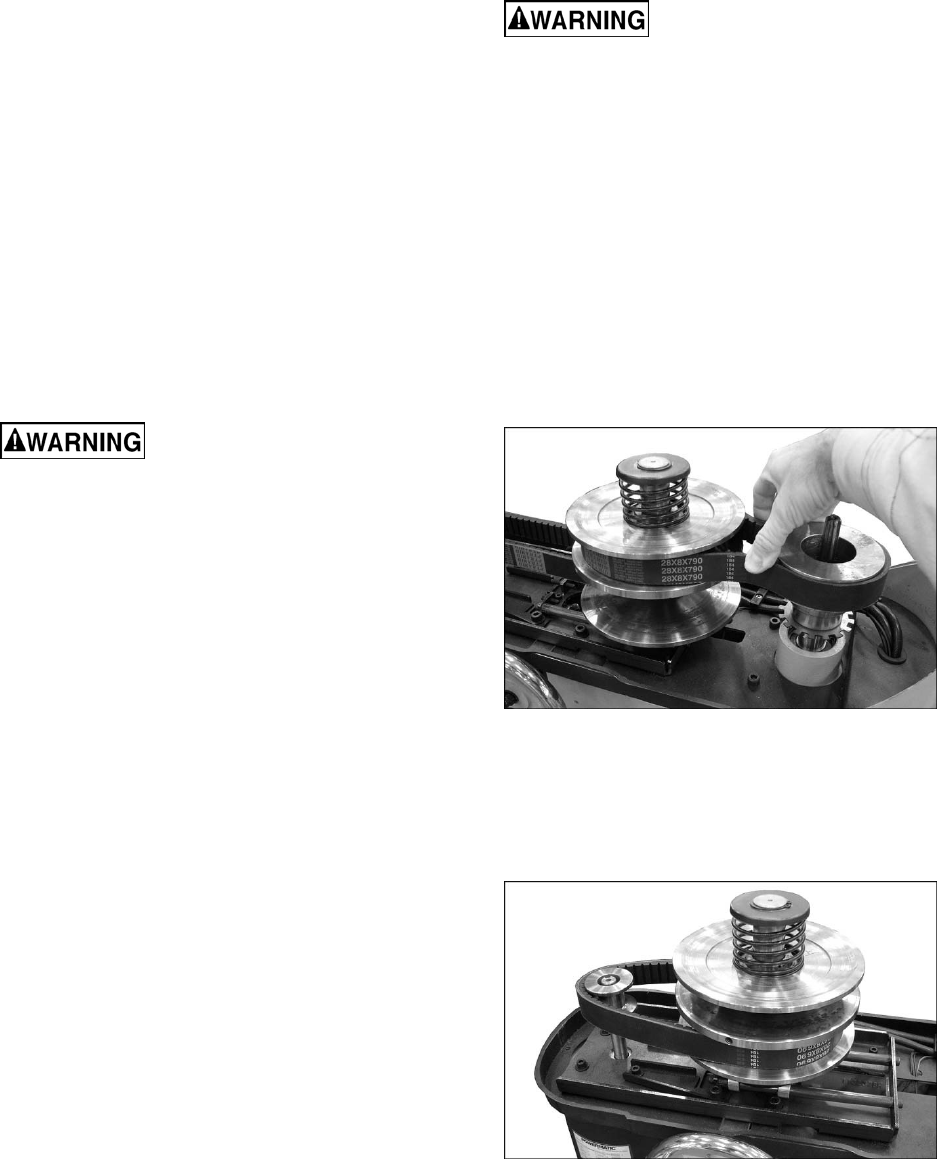
16
10.3 General Inspection
Before each operation of your Model 2800B drill
press, make a habit of checking that all locking
handles, set screws, bolts, etc., are tight on the
table and head. Confirm that drill bit is securely
inserted inside chuck jaws.
Clear all items, such as tools and rags, away from
machine.
Before attempting regular work, get the feel of the
drill press by practicing on scrap material. For best
results, always use sharp bits and proper feed
rates.
10.4 Setting rotation speed
There are several factors which determine the best
speed to use in any drill press operation, such as
kind of material being worked, size of hole, type of
drill, and quality of cut desired.
A general rule of thumb is, the smaller the drill, the
greater the required RPMs. And the speed should
be faster for soft materials and slower for harder
materials.
11.0 Maintenance
Before doing maintenance on
the machine, disconnect it from electrical
supply by pulling out the plug or switching off
the main switch. Failure to comply may cause
serious injury.
After each use, clean sawdust from the table with a
brush (do not use your hands).
Periodically apply a light film of oil to the quill and
column. This will reduce wear, prevent rust and
assure ease of operation.
It is good maintenance practice to periodically
clean the pulleys with a non-penetrating lubricant,
such as WD-40
®
, wipe off any excess, then apply a
light oil to the pulley shafts. NOTE: Do not use
graphite- or silicone-based lubricants.
Apply grease to the rack on the column.
Check that bolts are tight and electrical cords are in
good condition.
Belts should be in good condition with no signs of
cracks, frays or deterioration.
Bearings on the drill press are self-contained and
permanently lubricated; no further lubrication is
needed.
Exposed metal surfaces of table and base should
be kept clean and free of rust. Protective sprays or
paste wax are available from most hardware
stores. Note: Avoid wax that contains silicone or
other synthetic ingredients; these materials can
find their way into lumber and make staining and
finishing difficult.
The quill return spring should receive SAE 20 oil
once yearly. Apply the oil beneath the coil spring
cover (L, Figure 20) using a squirt can.
11.1 Belt replacement
Referring to Figures 26 and 27:
If future replacement of belts is needed, proceed
as follows:
This procedure requires
operating machine with pulley cover removed.
Keep hands away from moving belts and
pulleys.
1. Remove pulley cover using a long shaft
screwdriver.
2. Turn on drill press and increase speed (rotate
handwheel clockwise) to maximum, to bring
center pulley as far toward spindle pulley as
possible.
3. Shut off drill press and disconnect from
power.
4. Firmly squeeze center section of upper belt to
slacken tension. See Figure 26. If needed, pull
on belt away from center pulley to further
slacken.
Figure 26
5. Remove upper belt from around pulleys.
6. Reconnect to power, turn on drill press and
rotate handwheel counterclockwise until center
pulley is as close to motor pulley as possible.
See Figure 27.
Figure 27