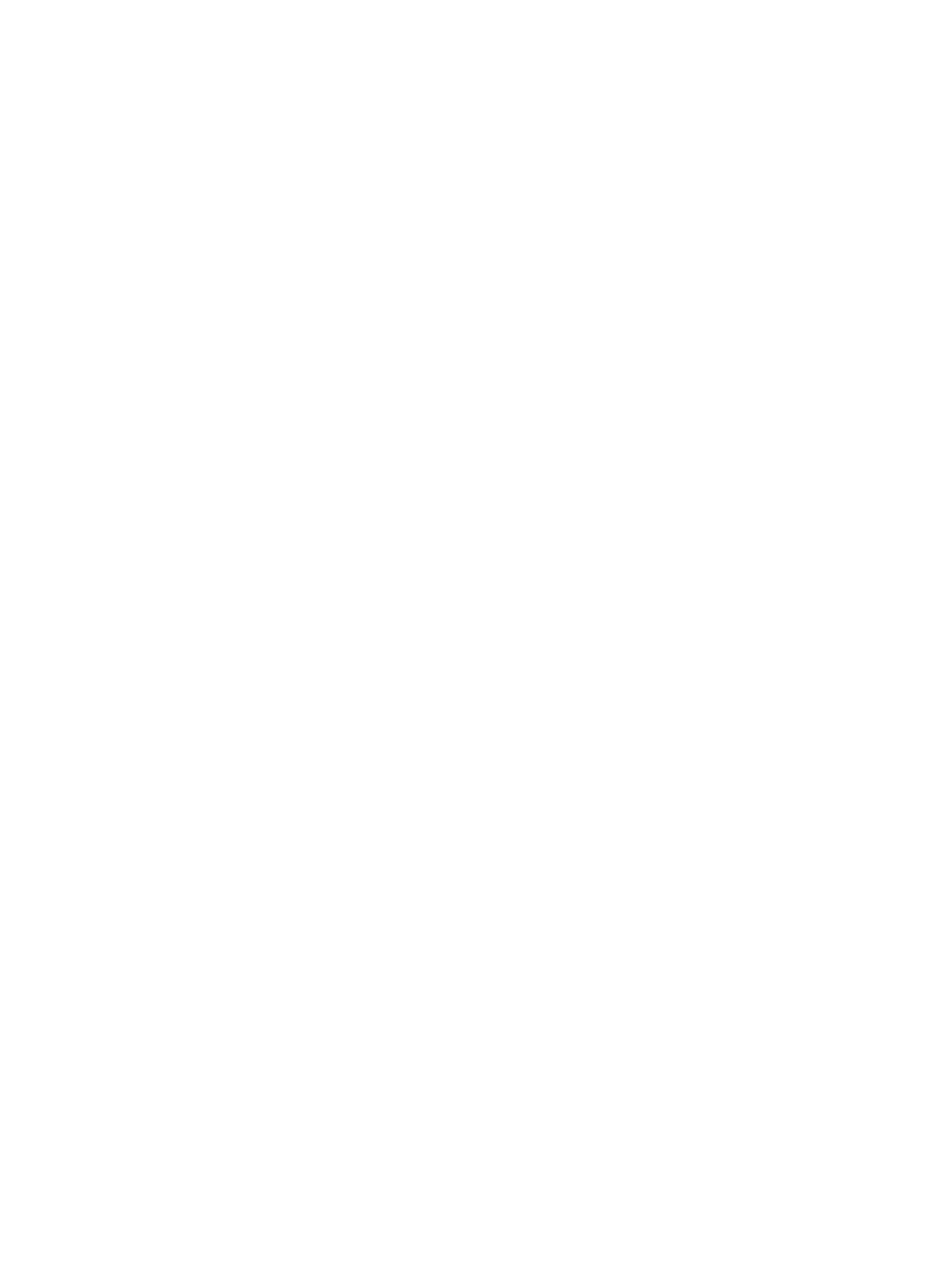
PRODUCT DESCRIPTION
The PRO-CUT
®
60 is a constant current, single range,
continuous control plasma cutting system. It provides
excellent starting characteristics, cutting visibility and
arc stability. The torch has a patented safety mecha-
nism which insures that the consumables are in place
before cutting or gouging. This is extremely important
due to the high voltages involved.
The PRO-CUT 60 comes standard with air regulator,
coarse air filter, oil coalescing filter, and pressure
gauge. The Pro-Cut 60 comes ready to use with the
torch attached. Machines equipped with handheld
torches are available with either 25 ft. (7.6m) or 50 ft.
(15.2m) torch cable. The undercarriage is standard
and is shipped assembled except for the handle. The
machine is capable of cutting with nitrogen or air.
Nitrogen is used to cut aluminum and other nonfer-
rous metals.
The PRO-CUT is controlled by a microprocessor-
based system. The machine performs rudimentary
self troubleshooting when powered up, which aids in
field servicing.
– 8 –
PREHEAT TEMPERATURE FOR
PLASMA CUTTING
Preheat temperature control is recommended for opti-
mum mechanical properties, crack resistance and
hardness control. This is particularly important on
high alloy steels and heat treated aluminum. Job con-
ditions, prevailing codes, alloy level, and other consid-
erations may also require preheat temperature con-
trol. The following minimum preheat temperature is
recommended as a starting point. Higher tempera-
tures may be used as required by the job conditions
and/or prevailing codes. If cracking or excessive
hardness occurs on the cut face, higher preheat tem-
perature may be required. The recommended mini-
mum preheat temperature for plate thickness up to 1/2
inch (12.7m) is 70 (°F) (21.1°C).
USER RESPONSIBILITY
Because design, fabrication, erection and cutting vari-
ables affect the results obtained in applying this type
of information, the serviceability of a product or struc-
ture is the responsibility of the user. Variation such as
plate chemistry, plate surface condition (oil, scale),
plate thickness, preheat, quench, gas type, gas flow
rate and equipment may produce results different than
those expected. Some adjustments to procedures
may be necessary to compensate for unique individ-
ual conditions. Test all procedures duplicating actual
field conditions.