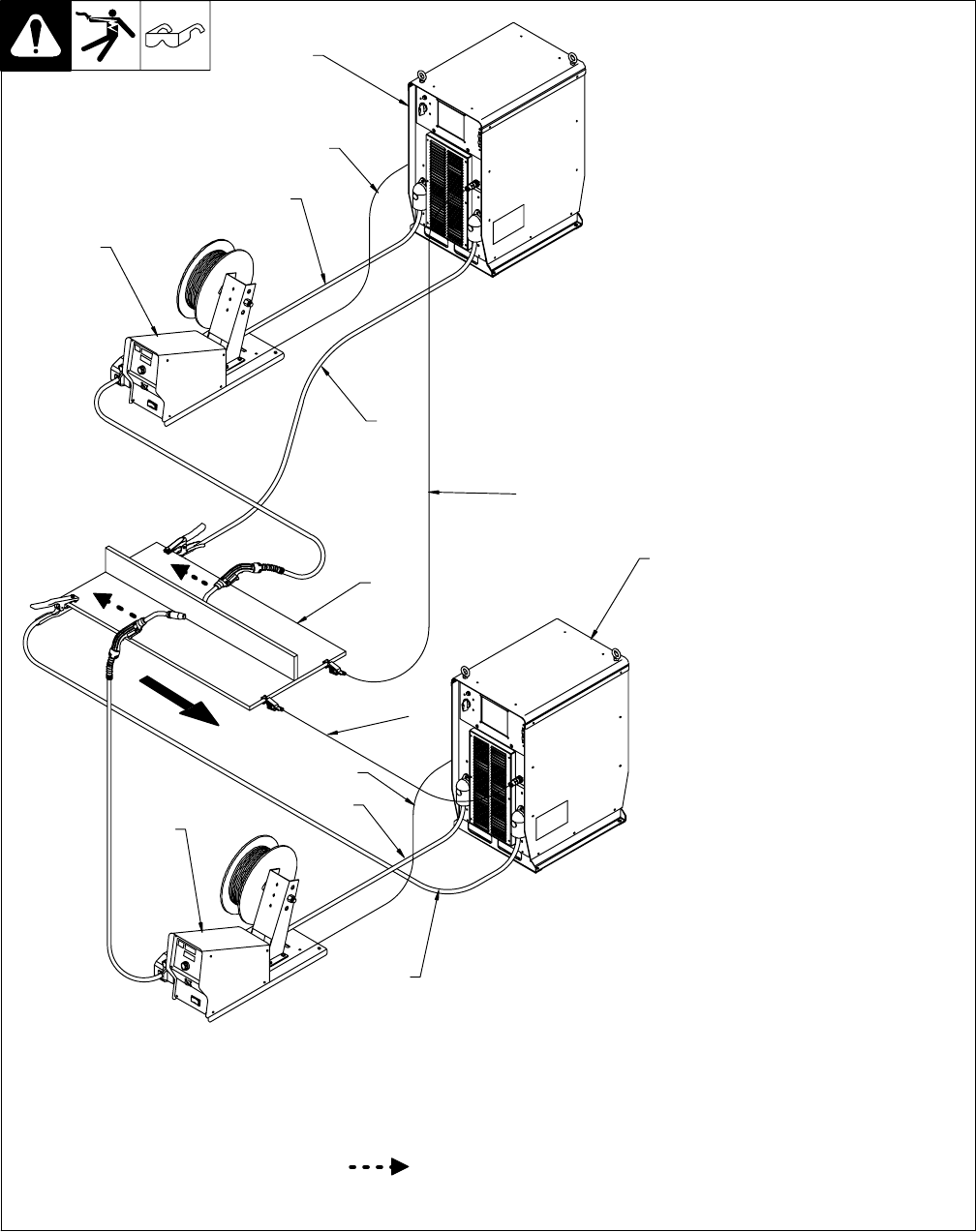
OM-220 389 Page 24
. Welding on a single workpiece using multiple welding power sources can cause arc blow and arc impedance to develop or intensify.
Ref. 804 459-A
1 Welding Power Source
2 Electrode Cable
3 Feeder Cable
4 Work Cable
5 Voltage Sensing Lead
6 Wire Feeder
7 Workpiece
Each welding power source should
have a separate work cable connection
to the workpiece. Do not stack or join
work cables together at the workpiece.
This is very important for pulse welding
applications.
It is important to connect the voltage
sensing lead as near to the weld as
possible, but not in the return current
path.
Connect voltage sensing lead at the end
of the weld joint.
The direction of the welding path should
be away from the work cable
connections.
Connect work clamp at the beginning of
the weld joint.
Each welding gun should have its own
source of shielding gas. Use a separate
shielding gas regulator and shielding
gas connection for each welding gun.
Arc blow is the deflection of a welding
arc from its normal path due to magnetic
forces. It will adversely affect the
appearance of a weld, cause excessive
spatter, and impair the quality of a weld.
Arc blow occurs primarily during the
welding of steel or ferromagnetic
metals. Weld current will take the path of
least resistance, but not always the
most direct path through the workpiece
to the work lead connection. The most
intense magnet force will be around the
arc due to a difference in resistance for
the magnetic path in the base metal.
The work clamp connection is important
and should be placed at the starting
point of a weld. It is recommended to
have as short of an arc as possible so
that there is less of an arc for the
magnetic forces to control. Conditions
affecting the magnetic force acting on
the arc vary so widely that the reference
here is only about cabling connections
and arc preferences.
5-4. Using Multiple Welding Power Sources
Gun
Travel
Current Flow Path
1
2
3
4
5
6
7
5
6
4
1
3
2