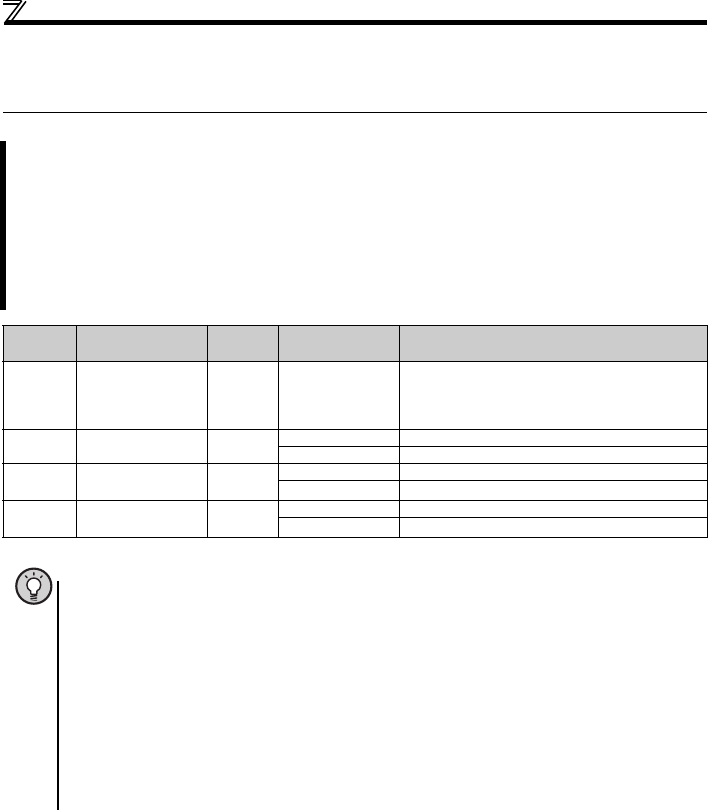
30
Acquiring large starting torque and low speed torque (Advanced magnetic flux vector control, General-purpose magnetic flux vector control) (Pr. 71, Pr. 80, Pr. 81, Pr. 800)
5.3 Acquiring large starting torque and low speed torque
(Advanced magnetic flux vector control
, General-purpose
magnetic flux vector control
) (Pr. 71, Pr. 80, Pr. 81, Pr. 800)
Advanced magnetic flux vector control can be selected by setting the capacity, poles and type of the motor used in Pr.
80 and Pr. 81.
Advanced magnetic flux vector control, General-purpose magnetic flux vector control?
The low speed torque can be improved by providing voltage compensation to flow a motor current which meets the
load torque. Output frequency compensation (slip compensation) is made so that the motor actual speed
approximates a speed command value. Effective when load fluctuates drastically, etc.
General-purpose magnetic flux vector control is the same function as it is for the FR-E500 series. Select this control
when operation characteristics as similar as possible are required when replacing from the FR-E500 series. For other
cases, select Advanced magnetic flux vector control.
Parameter
Number
Name
Initial
Value
Setting Range Description
71 Applied motor
0
0,1, 3 to 6,
13 to 16, 23, 24
40, 43, 44
50, 53, 54
By selecting a standard motor or constant-torque motor,
thermal characteristic and motor constants of each motor
are set.
80 Motor capacity
9999
0.1 to 15kW Set the applied motor capacity.
9999 V/F control
81
Number of motor
poles
9999
2, 4, 6, 8, 10 Set the number of motor poles.
9999 V/F control
800
Control method
selection
20
20 Advanced magnetic flux vector control
30 General-purpose magnetic flux vector control
Set a value other than "9999" in Pr. 80 and Pr. 81.
POINT
If the following conditions are not satisfied, select V/F control since malfunction such as insufficient torque and
uneven rotation may occur.
The motor capacity should be equal to or one rank lower than the inverter capacity. (Note that the capacity
should be 0.1kW or higher.)
Motor to be used is any of Mitsubishi standard motor (SF-JR 0.2kW or more), high efficiency motor (SF-HR
0.2kW or more) or Mitsubishi constant-torque motor (SF-JRCA four-pole, SF-HRCA 0.2kW to 15kW). When
using a motor other than the above (other manufacturer's motor), perform offline auto tuning without fail.
Single-motor operation (one motor run by one inverter) should be performed.
The wiring length from inverter to motor should be within 30m. (Perform offline auto tuning in the state where
wiring work is performed when the wiring length exceeds 30m.)
Permissible wiring length between inverter and motor differs according to the inverter capacity and setting value
of Pr. 72 PWM frequency selection (carrier frequency). Refer to page 14 for the permissible wiring length.