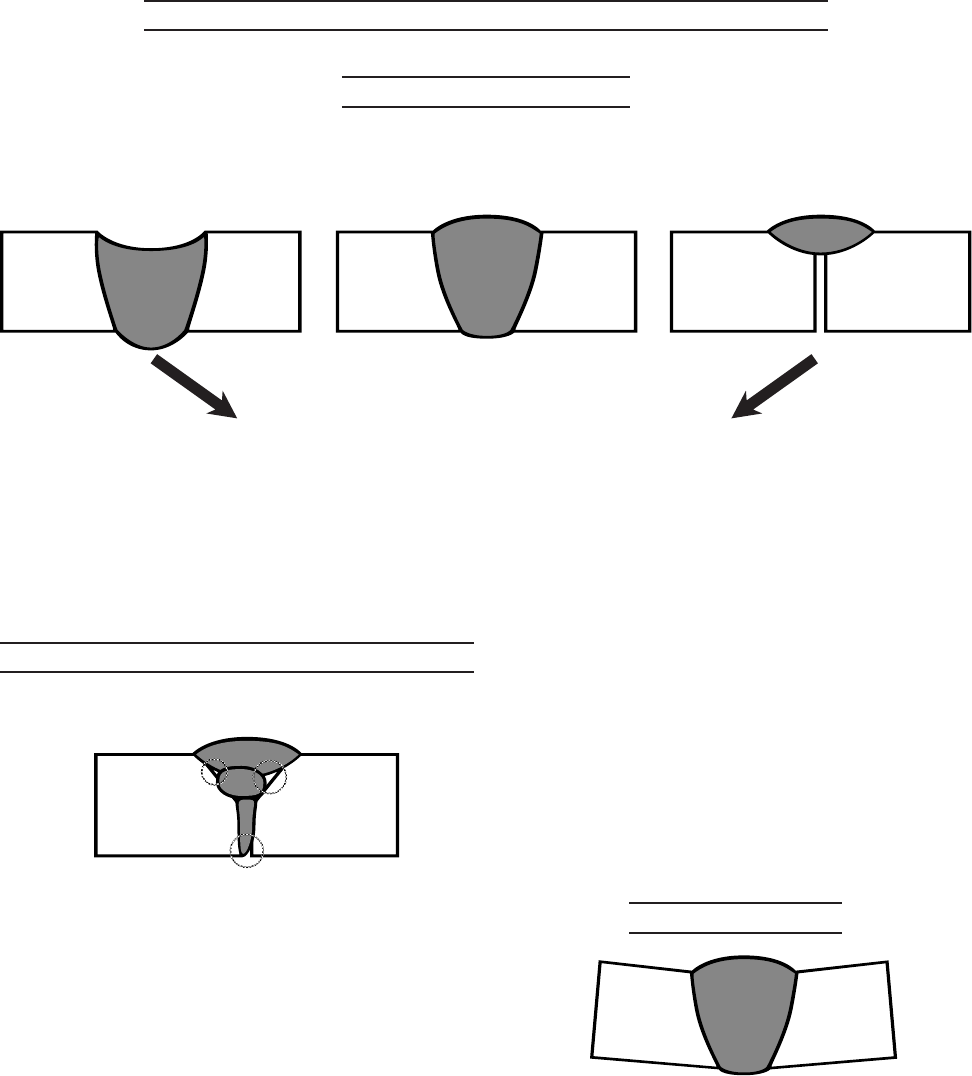
For technical questions, please call 1-800-444-3353;
Troubleshooting section at end of manual.
Page 19SKU 55167
WELD DIAGNOSIS
EXCESS OR BURN-THROUGH
Weld droops on top and
underneath, or falls through
entirely, making a hole.
PROPER
Weld is visible underneath and
bulges slightly on top.
INADEQUATE
Weld does not contact the joint
fully, just on the surface.
WELD PENETRATION
POSSIBLE CAUSES AND SOLUTIONS
1. Excessive material at weld:
Reduce wire feed speed.
2. Overheating:
Increase welding speed and ensure that
welding speed is kept steady.
POSSIBLE CAUSES AND SOLUTIONS
1. Workpieces too thick/close:
Joint design must allow weld to reach bot-
tom of groove and allow proper welding
procedures.
2. Incorrect welding technique:
Maintain
1
/
2
” or less stickout.
Keep arc on leading edge of weld pud-
dle.
Hold gun at proper angles as stated under
Holding The Torch on page 17.
3. Insufficient weld material:
Increase wire feed speed.
4. Insufficient weld heat:
Reduce Welding Speed.
CROSS SECTIONS
WELD NOT ADHERING PROPERLY
Gaps present between weld and previous bead or
between weld and workpiece. See areas below.
POSSIBLE CAUSES AND SOLUTIONS
1. Dirty workpiece:
Make certain that workpiece is clean and
free from oil, coatings, and other resi-
dues.
2. Insufficient weld material:
Increase wire feed speed.
3. Incorrect welding technique:
Place stringer bead at correct place in
joint.
Adjust workpiece position or weld angle to
permit proper welding to bottom of piece.
Pause briefly at sides when using a weave
bead.
Keep arc on leading edge of weld
puddle.
Hold gun at proper angles as stated under
Holding The Torch on page 17.
CROSS
SECTION
BEND AT JOINT
POSSIBLE CAUSES AND SOLUTIONS
1. Improper clamping:
Make sure that pieces are clamped se-
curely in place.
Make tack welds to help hold pieces.
2. Excessive heat:
Weld a small portion and allow to cool
before proceeding.
Reduce wire feed speed.
Increase weld speed.
CROSS
SECTION