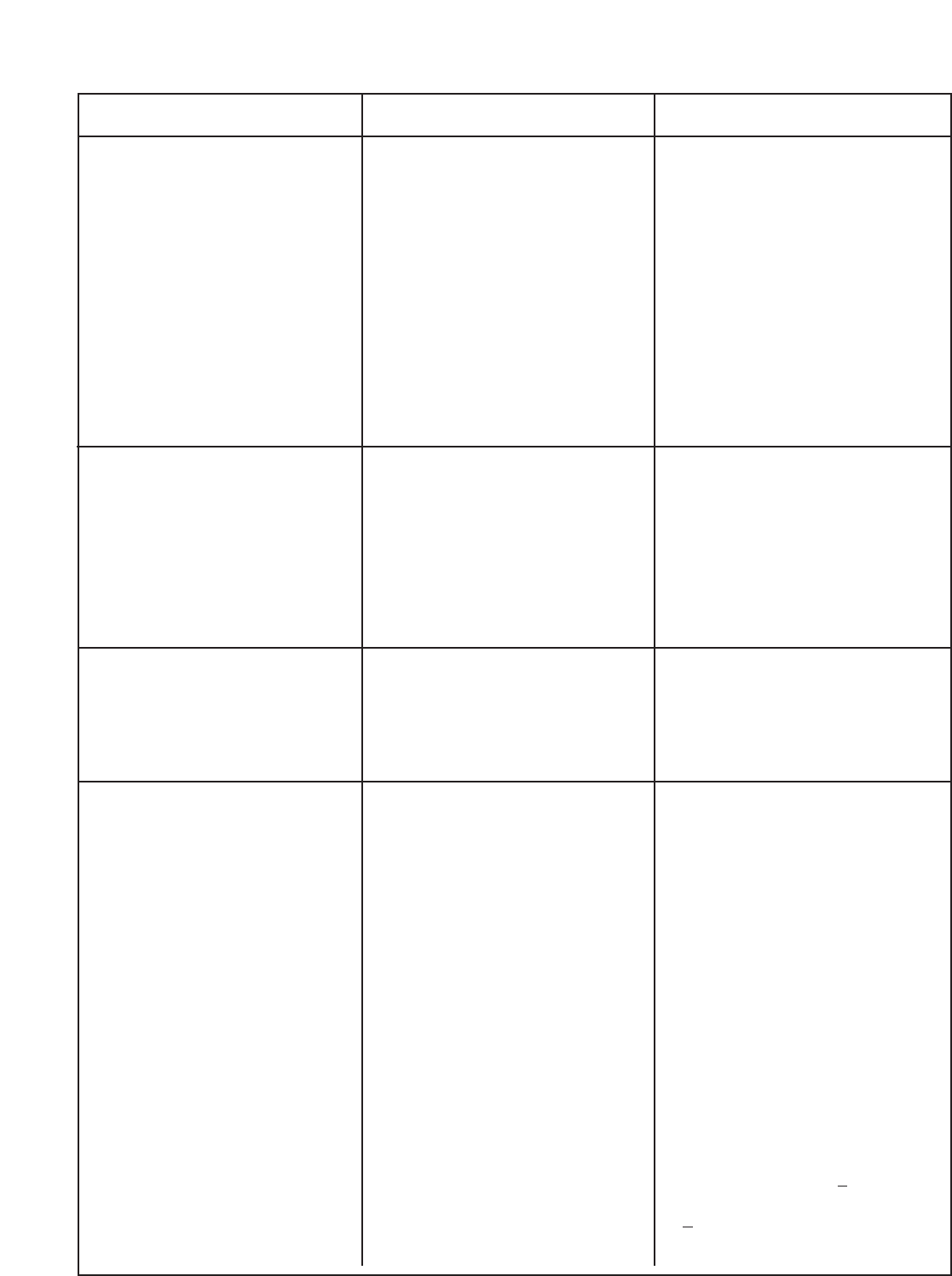
PROBLEMS
PROBLEM
3. Poor arc striking with sticking or
“blast-offs”, weld porosity,
narrow and ropy looking bead,
or electrode stubbing into plate
while welding.
4. Tip seizes in diffuser.
5. Unit shuts off while welding and
“HXX” appears on display.
6. Drive roll does not turn although
arc voltage is present and
solenoid is on.
POSSIBLE CAUSE
a. Improper procedures or
techniques.
b. Improper gas shielding.
a. Tip overheating due to prolonged
or excessive high current and/or
duty cycle welding.
a. See Problem 1.
b. Defective wire feed motor or
gearbox.
a. Defective Wire Feed Unit to
Control box cable or harnessing.
b. Defective wire feed motor or
control PC board.
WHATTODO
a. See “Gas Metal Arc Welding
Guide” (GS-100).
b. Clean gas nozzle. Make certain
that gas diffuser is not empty or
turned off. Make certain gas flow
rate is proper.
Remove gun liner and check
rubber seal for any sign of
deterioration or damage. Be sure
set screw in brass connector is in
place and tightened against the
liner bushing.
a. Do not exceed current and duty
cycle rating of gun.
A light application of high
temperature antiseize lubricant
(such as Lincoln E2607 Graphite
Grease) may be applied to tip
threads.
a. Correct problems causing motor
overload.
b. Replace.
a. Remove Wire Feed Unit to
Control Box Cable and Check A
to A and B to B for continuity. If
there is no continuity in either or
both cases, replace cable.
Otherwise, check Harnessing
from A and B of MS connector on
control box to control board and
A and B at Wire Feed Unit MS
connector to Motor leads for
continuity. If harnessing is O.K.
proceed to b.
b. Set Run-In speed to maximum.
Disconnect wire drive plug P5
from PC board. Measure voltage
across pin 1(+) of J5 and pin 2 (-)
of J5 on PC board with trigger
closed. If voltage is >
24V DC,
then replace motor assembly. If
< 24V DC, replace Control PC
board (see Procedure for
Replacing PC Boards).
– 30 –