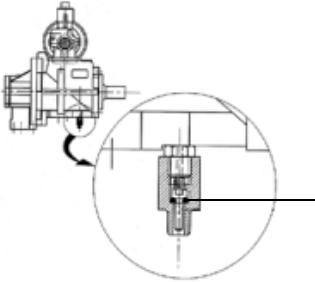
Chicago Pneumatic Compressors
62 305 258 65
01/2008
Page 22
D - Oil and air cooler
The aluminium oil and air cooler is a vital part in the CPVS system.
Please take care of this element. To prevent the nest of tubes from
being deformed or damaged, when assembling or disassembling
the radiator unions and hoses, the radiator sleeves' must be kept
rotating by means of a wrench. The outer surface of the nest of
tubes must always be kept clean in order to enable proper heat
transfer. In the event of a leak, the source of the leak must be
detected. In order to do this:
- Stop the CPVS.
- Clean the greasy areas.
- Look for leaks using conventional means (soap solution, …).
Pressurized shutdown retains the pressure in the machine circuit
for a few moments so that any leak can be more easily located.
E - Oil separator (see B Section 1)
The oil separator's lifespan depends on the cleanliness of the air
coming into the compressor, on regular oil filter changes, on the qua-
lity of the oil used, on the attention with which the oil tank condensate
drains are carried out and on the ambient temperature of the room.
(see notice on the electronic plate for resetting the time).
Check the cleanliness of the pipe that returns the oil to be aspired
(transparent) to prevent the injector from becoming blocked and
to ensure that the oil recovered can pass through easily.
Excessive oil consumption
The presence of excess oil in the discharge air, a rapid drop in
level show a probable deterioration in the oil separator that must
be changed.
The unit must first be checked to make sure that there is no oil
loss and that the oil return is working properly.
Changing the oil separator
Dismantle all the piping connected to the tank's upper flange (air
discharge, regulation system supply, and oil return). Undo the
screws that hold the tank cover and remove it.
- If the old oil separator musty be remounted, use new seals.
- Be very careful during installation of the oil separator so as to
avoid possible damage.
- The new oil separator is delivered with its two seals on either
side of the flange.
- Slight undulations in the flange will flatten out when the screws
are tightened.
- Apply a 6 mkg torque.
- Replace the oil return tube correctly so it touches the bottom of
the oil separator.
F - Oil return pipe (see fig. 20)
Placed under the compressor
• Dismantle the body of the anti-oil return pipe.
• Lift the anti-oil return pipe.
• Check the state of the o-ring (rep. 64).
• Reassemble.
Fig. 20 - Oil return pipe
G - Draining condensation water
(see B Section 1)
Condensation water prevents proper lubrication. The resulting
substantial wear leads to a reduction in the lifespan of the CPVS. It is
therefore essential to drain condensation water.
Draining of condensates in the oil circuit (see fig. 19) :
Draining will only take place at least 12 hours after the CPVS has
been shut down. It can be carried out for example on the morning
of the start-up.
To do this :
- Slowly open the oil change tap and let the water escape.
- When the oil appears, close the valve immediately to avoid any
loss.
- Refill with oil if necessary.
H - Temperature safety tests
(See instructions electronic board).
IF THE SENSOR IS NOT WORKING, IT MUST BE
CHANGED.
I - Refastening electric connections
A loosening of the electric power cables leads to the contactors
ove-rheating which can lead to their destruction.
Periodic refastening is therefore necessary at the star and triangle
line contactor arrivals and departures. (see Maintenance Table).
All electric power supply to the machine must be cut off before
opening the electric cabinet.
J - Decommissioning the compressor at
the end of its useful life (see B Section 1)
1. Stop the compressor and close the air outlet valve.
2. Unplug the compressor from the electric supply.
3. Decompress the compressor : unplug the 4/6 piping on the
oil separator cover.
4. Close and decompress the section of the air network which
is linked to the exit valve. Disconnect from the compressed
air exit pipe from the air network.
5. Empty the circuits of oil and condensates.
6. Disconnect the compressor condensate piping from the
condensate draining system.
64