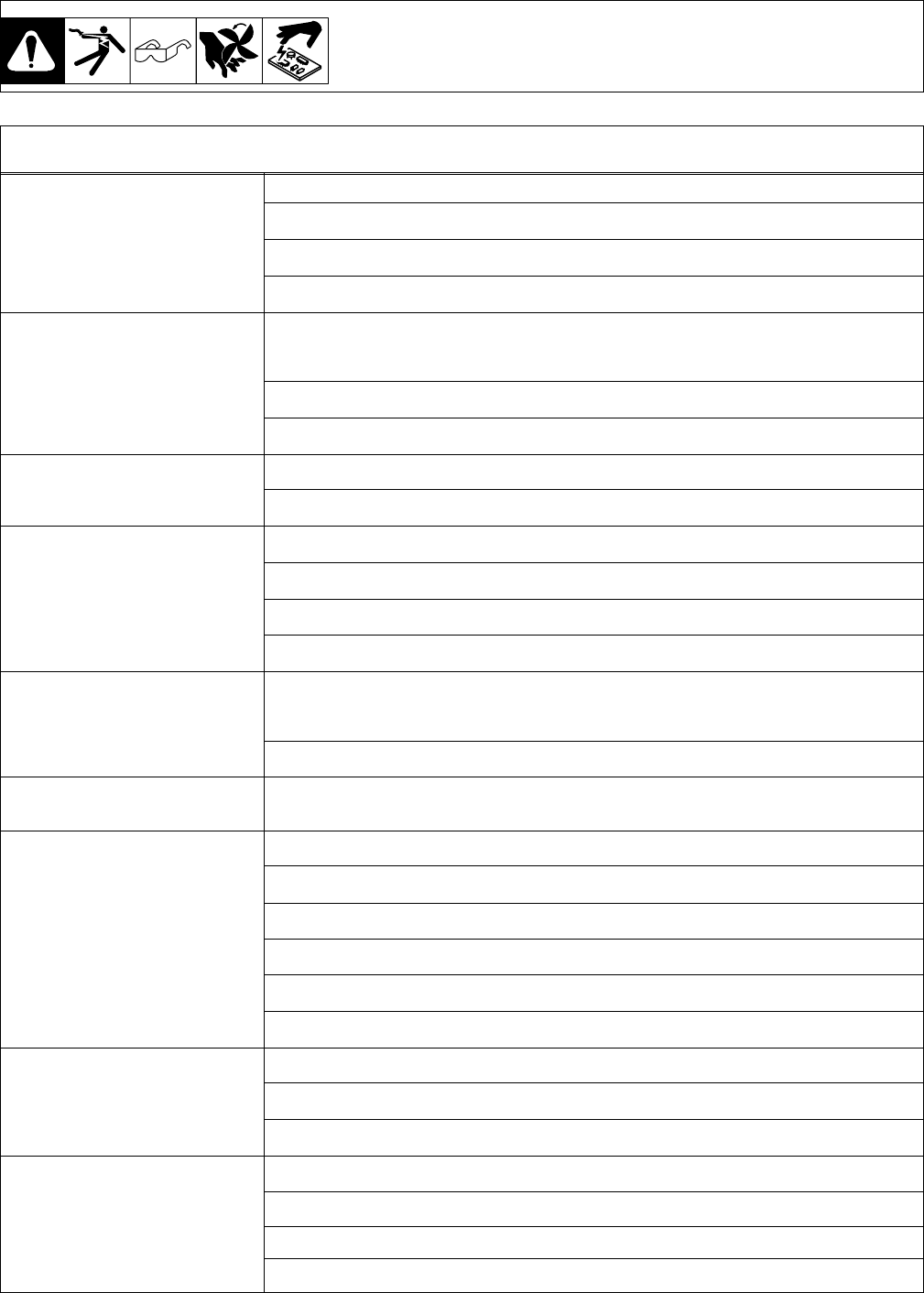
OM-356 Page 37
5-5. Troubleshooting
NOTE: The remedies listed below are recommendations only. If these remedies do not fix
the trouble with your unit, have a Factory Authorized Service Agent check unit.
There are not user serviceable parts inside unit.
Refer to Section 5-4 for any Help (HLP) message displayed on voltmeter/ammeter.
Trouble Remedy
No weld output; unit completely
Place line disconnect switch in On position (see Section 3-10).
inoperative.
Check and replace line fuse(s), if necessary (see Section 3-10).
Check for proper input power connections (see Section 3-10).
Check for proper jumper link position (see Section 3-10).
No weld output; unit on. If using remote control, place Output control in Remote 14 position, and make sure remote control is
connected to Remote 14 receptacle. If remote is not being used, place Output control in On position
(see Section 4-1).
Check, repair, or replace remote control.
Have Factory Authorized Service Agent check unit.
Unit provides only maximum or
Make sure Amperage control is in proper position (see Section 4-1).
minimum weld output.
Have Factory Authorized Service Agent check unit.
Erratic or improper weld output. Use proper size and type of weld cable (see Section 3-6).
Clean and tighten all weld connections.
Check position of Output Selector control (see Section Figure 4-1).
If using remote control, check position of Amperage Adjustment control (see Section 4-1).
No control of weld output. If using remote control, place Output control in Remote 14 position, and make sure remote control is
connected to Remote 14 receptacle. If remote is not being used, place Output control in On position
(see Section 4-1).
Make sure Amperage switch is in proper position (see Section 4-1).
No output from duplex receptacle RC2
and no high frequency.
Reset circuit breaker CB1 (see Section 5-2).
Lack of high frequency; difficulty in
Reset circuit breaker CB1 (see Section 5-2).
starting GTAW arc.
Select proper size tungsten.
Check High Frequency Intensity control setting (see Figure 4-1).
Be sure torch cable is not close to any grounded metal.
Check cables and torch for cracked insulation or bad connections. Repair or replace.
Check spark gaps (see Section 5-3).
Wandering arc – poor control of
Reduce gas flow rate.
direction of arc.
Select proper size tungsten.
Properly prepare tungsten.
Tungsten electrode oxidizing and not
Shield weld zone from drafts.
remaining bright after conclusion of
weld.
Increase postflow time.
Check and tighten all gas fittings.
Properly prepare tungsten.