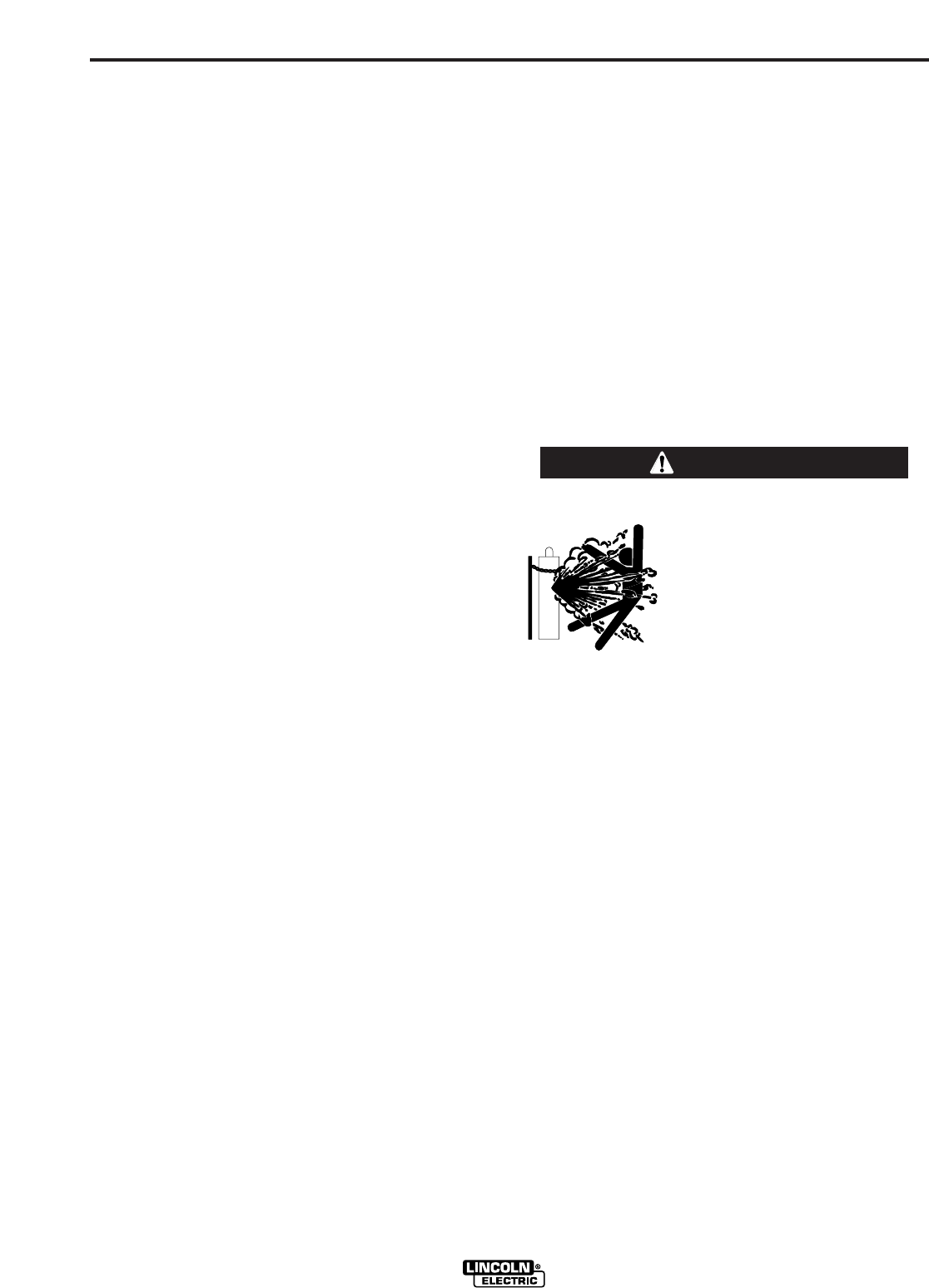
A-5
INSTALLATION
PRO-CUT 80
A-5
GAS INPUT CONNECTIONS
Supply the PRO-CUT 80 with clean compressed air or
nitrogen.
• Supply pressure must be between 80 psi(5.6kg/cm
2
)
and 120 psi(8.4kg/cm
2
).
• Pressure gage, located on the front of the machine,
should be set to approximately 70 psi(4.9kg/cm
2
) for
a 25ft.(7.6m) torch and 75 psi(5.3kg/cm
2
) for a 50
ft.(15.2m) torch while gas is flowing (purging or cut-
ting).
• Flow rate should be approximately 8.0 cfm (227
I/min.).
NOTE: Oil in the air supply to the PRO-CUT 80 can
cause severe problems. Use only a clean air
supply.
• Connect the gas supply to the PRO-CUT 80 regula-
tor.
• Compressed gas should be supplied to the fitting
connection mounted on the filter at the rear of the
machine. If necessary, this fitting can be removed
allowing plumbing access through the 1/4” NPT input
port on the filter body.
• If compressed air is being used, it is highly recom-
mended that an inline prefilter be installed in the air
supply line ahead of the air connection to the PRO-
CUT’s coalescing filter. While the coalescing filter is
used to remove small amounts of oil and water
aerosol particles from the air supply line, the prefilter
can be used to remove larger particulates before
they reach the coalescing filter element. This will
prolong the life of the coalescing filter element by up
to six times what it would be without the prefilter, and
in turn, prolong the life of the PRO-CUT torch and
consumables as well.
• A standard nominal 5 micron inline prefilter is recom-
mended; however, for optimum performance, select
a prefilter with a 3 micron absolute rating. If these fil-
ter ratings are unavailable, anything with a rating
less than, or equal to, 20 micron would be accept-
able to use. In line filter elements will generally filter
the air with little restriction to the airflow until the ele-
ment is about 75 % contaminated. After this point,
there will be a noticeable pressure drop in the line.
Filter elements should be replaced when a pressure
drop of 8-10psi(.56-.70kg/cm
2
) is indicated; however,
for optimum performance of the PRO-CUT, the filter
element should be replaced at or before the pres-
sure drop reaches 8 psi(.56kg/cm
2
). Be sure to
select a prefilter that will accommodate the neces-
sary flow rating for the PRO-CUT as specified in the
Installation section of this instruction manual under
the Gas Input Connections heading.
• While it is recommended that an in line prefilter be
placed ahead of each PRO-CUT that may be
installed in a shared air supply line, one large inline
prefilter may instead be used to accommodate sev-
eral PRO-CUTs simultaneously. If a shared prefilter
is desired, it must be rated to provide the necessary
flow rate, as specified, to ensure proper operation of
each of the PRO-CUTs sharing a connection.
NOTE: When using nitrogen gas from a cylinder, the
cylinder must have a pressure regulator.
• Maximum psi from nitrogen gas cylinder to PRO-
CUT 80 regulator should never exceed 120
psi(8.4kg/cm
2
).
• Install a hose between the nitrogen gas cylinder reg-
ulator and the PRO-CUT 80 gas inlet.
• CYLINDER could explode if
damaged.
• Keep cylinder upright and
chained to a fixed support.
• Keep cylinder away from areas
where it could be damaged.
• Never lift machine with cylinder
attached.
• Never allow the cutting torch to touch the cylin-
der.
• Keep cylinder away from live electrical parts.
• Maximum inlet pressure 120 psi(8.4kg/cm
2
).
__________________
OUTPUT CONNECTIONS
Torch Connection
The Pro-Cut 80 is sent from the factory with a PCT 80
cutting torch. Additional cutting torches can be
ordered from the K1571 series. Hand-held and mech-
anized torches come with 25'(7.6m) or 50’(15.2m)
cables.
All torches are connected to the Pro-Cut with a quick
connect on the case front for easy change over. This
feature is excellent for changing between a hand cut-
ting torch and a mechanized torch.
For more information on the torch and its components,
refer to the PCT80 Operator’s Manual (IM588 latest
version).
WARNING