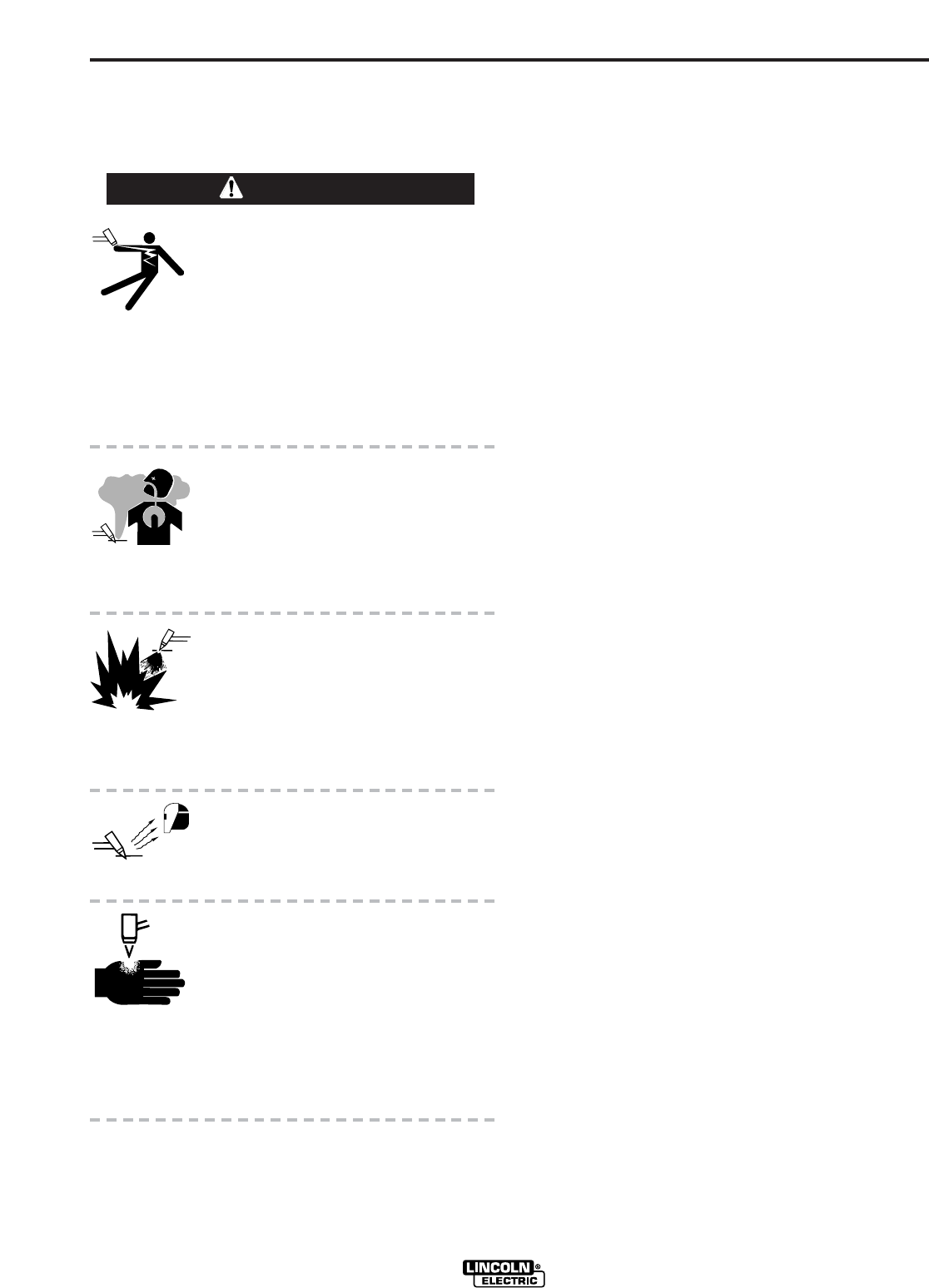
B-1
OPERATION
PRO-CUT 80
B-1
Read and understand this entire section before oper-
ating the machine.
SAFETY PRECAUTIONS
DESCRIPTION
The PRO-CUT 80 is a constant current, continuous con-
trol plasma cutting power source. It provides superior
and reliable starting characteristics, cutting visibility and
arc stability. When cutting expanded metal, the PRO-
CUT 80 out performs the competition due to its quick,
clean response to arc transfers. The power supply
design provides high transfer-to-cut distances which
makes pierce cutting more reliable and with less nozzle
wear. The control system has a safety mechanism to
insure that the nozzle and electrode are in place before
cutting or gouging. This is extremely important due to the
high voltages involved.
The PRO-CUT 80 comes standard with an air regulator,
coarse air filter, and pressure gauge. There are six differ-
ent torch and cable systems to choose from: hand-held
torch with 25'(7.6m) or 50'(15.2) cable, machine and
robotic torch both with 25'(7.6m) and 50'(15.2) cable.
Consumables are included so that cutting can begin right
out of the box. Consumables can also be ordered as indi-
vidual packages.
The PRO-CUT 80 initiates the plasma arc with a simple,
yet reliable, touch start mechanism. This system elimi-
nates many of the failure problems associated with hi-fre-
quency start systems. The PRO-CUT 80 is capable of
cutting with nitrogen or air.
The PRO-CUT 80 is controlled by a microprocessor-
based control board. The machine performs rudimentary
self troubleshooting when powered up which aids in field
servicing.
NOTE: All P.C. boards are protected by a moisture resis-
tant coating. When the plasma cutter is operated, this
coating will "bake off" of certain power resistors that nor-
mally operate at high temperatures emitting some smoke
and odor for a short time. These resistors and the P.C.
board beneath them may become darkened. This is a
normal occurrence and does not damage the component
or affect the machine performance.
PREHEAT TEMPERATURE FOR
PLASMA CUTTING
Preheat temperature control is not necessary in most
applications when plasma arc cutting or gouging. Preheat
temperature control may be necessary on high carbon
alloy steels and heat treated aluminum for crack resis-
tance and hardness control. Job conditions, prevailing
codes, alloy level, and other considerations may also
require preheat temperature control. The following mini-
mum preheat temperature is recommended as a starting
point. Higher temperatures may be used as required by
the job conditions and/or prevailing codes. If cracking or
excessive hardness occurs on the cut face, higher preheat
temperature may be required. The recommended mini-
mum preheat temperature for plate thickness up to 1/2"
(12.7mm) is 70°F (21.1°C).
ELECTRIC SHOCK
can kill.
• Do not touch electrically live parts
or electrode with skin or wet
clothing.
• Insulate yourself from work and
ground.
• Always wear dry insulating
gloves.
FUMES AND GASES
can be dangerous.
• Keep your head out of fumes.
• Use ventilation or exhaust to
remove fumes from breathing
zone.
WELDING, CUTTING and
GOUGING SPARKS
can cause fire or explosion
• Keep flammable material away.
• Do not weld, cut or gouge on
containers that have held combustibles.
Observe additional Safety Guidelines detailed in
the beginning of this manual.
WARNING
ARC RAYS
can burn.
• Wear eye, ear and body
protection.
PLASMA ARC
can injure
• Keep your body away from nozzle
and plasma arc.
• Operate the pilot arc with caution. The
pilot arc is capable of burning the
operator, others or even piercing
safety clothing.