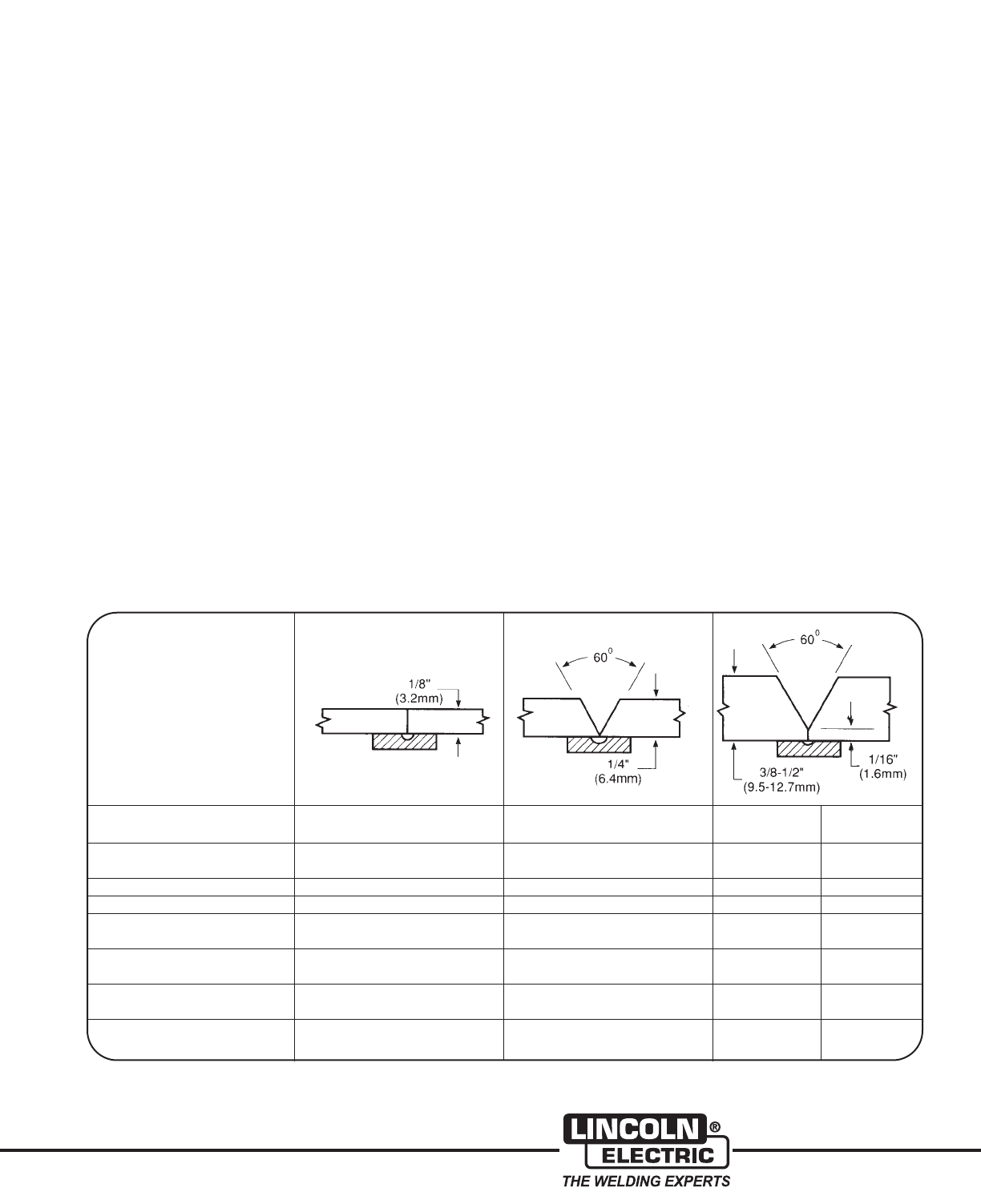
29
inch, but usually less than 1/16 inch,
are used with relatively high currents
to create the spray arc transfer. A
current of approximately 300-350
amperes is required for a 1/16"
electrode, depending on the shield -
ing gas and type of stainless wire
being used. The degree of spatter is
dependent upon the composition
and flow rate of the shielding gas,
wire feed speed and the characteris -
tics of the welding power supply.
DCEP is used for most stainless steel
GMA welding and an argon 1 or
2%-oxygen gas mixture is recom -
mend ed. Suggested procedures for
GMA welding 200 and 300 series
stainless steels in the spray transfer
mode are given in Figure 15.
On square butt welds, a backup strip
should be used to prevent weld
metal drop-through. When fitup is
poor or copper backing cannot be
used, drop-through may be
minimized by shortcircuiting transfer
welding the first pass.
When welding with the semiauto -
matic gun, forehand (“pushing”)
techniques are beneficial. Although
the operator’s hand is exposed to
more radiated heat, better visibility is
obtained.
For welding plate 1/4 inch and
thicker, the gun should be moved
back and forth in the direction of the
joint and at the same time moved
slightly from side to side. On thinner
metal, however, only back and forth
motion along the joint is used. The
more economical shortcircuiting
trans fer process for thinner material
should be employed in the overhead
and horizontal position for at least
the root and first passes. Although
some operators use a short digging
spray arc to control the puddle, the
weld may be abnormally porous.
Power supply units with slope,
voltage and inductance controls are
recommended for the welding of
stainless steel with shortcircuiting
transfer. Inductance, in particular,
plays an important part in obtaining
proper puddle fluidity.
The shielding gas often recommend -
ed for shortcircuiting welding of
stainless steel contains 90% helium,
7.5% argon and 2.5% carbon
dioxide. The gas gives the most
desirable bead contour while keeping
the CO
2
level low enough so that is
does not influence the corrosion
resistance of the metal. High
inductance in the power supply
output is beneficial when using this
gas mixture.
Single pass welds may also be made
using argon-oxygen and argon-CO
2
gas mixes. However, arc voltage for
steady shortcircuiting transfer may be
as much as 6 volts lower than for the
helium based gas. The colder arc
may lead to lack of fusion defects.
The CO
2
in the shielding gas will
affect the corrosion resistance of
multipass welds made with
shortcircuiting transfer due to carbon
pickup.
Wire extension or stickout should be
kept as short as possible. Backhand
welding is usually easier on fillet
Gas-Argon + 1% Oxygen.
Gas flow 35 cfh.
(16.5L/min.)
Plate Thickness (in.) 1/8 1/4 3/8 1/2
Plate Thickness mm. 3.2 6.4 9.5 12.7
Electrode Size in. 1/16 1/16 1/16 3/32
Electrode Size mm. 1.6 1.6 1.6 2.4
Pass 1224
Current DC(+) 225 275 300 325
Wire Feed Speed (ipm) 140 175 200 225
Wire Feed Speed mm/sec. 60 74 85 95
Arc Speed (ipm) 19 - 21 19 - 21 15 - 17 15 - 17
Arc Speed mm/sec. 8.0 - 8.9 8.0 - 8.9 6.3 - 7.2 6.3 - 7.2
Electrode Required (lb/ft) 0.075 0.189 0.272 0.495
Electrode Required kg./m 0.112 0.282 0.405 0.737
Total Time (hr/ft of weld) 0.010 0.020 0.025 0.050
Total Time hr/m of weld. 0.033 0.066 0.082 0.164
FIGURE 15 — Suggested procedures for GMAW of butt joints in 200 and 300 series stainless steels
using the spray arc transfer mode.