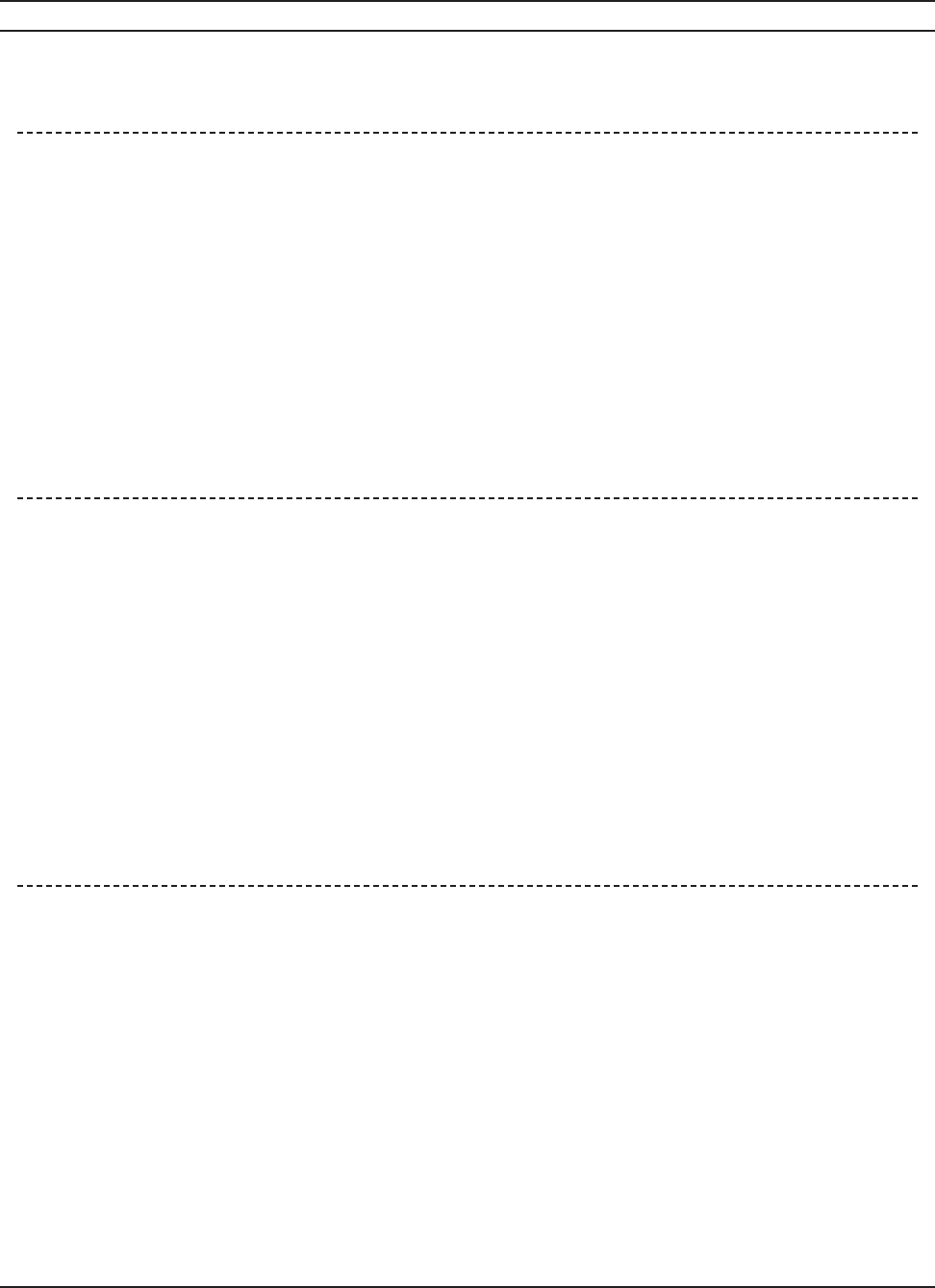
IMPORTANT!
Be CERTAIN to shut off the Welder, disconnect it from power, and discharge the torch to
ground before adjusting, cleaning, or repairing the unit.
SKU 55525 For technical questions, please call 1-800-444-3353. Page 31
If the steps above do not solve the problem or if the repairs involved are too
complex, contact a qualified technician.
TROUBLESHOOTING
Wire feed motor runs but wire does not feed properly
POSSIBLE CAUSES AND SOLUTIONS
Insufficient wire feed pressure:
Increase wire feed pressure properly - follow instructions on page 12-13.
Incorrect wire feed roll size:
Replace with the proper one - follow the Wire Settings instructions on page 14.
Damaged torch, cable, or liner assembly:
Have a qualified technician inspect these parts and replace as necessary.
1.
2.
3.
Wire creates a bird’s nest During operation
POSSIBLE CAUSES AND SOLUTIONS
Excess wire feed pressure:
Adjust wire feed pressure properly - follow instructions on page 12-13.
Incorrect contact tip size:
Replace with the proper tip for the wire size used.
Gun end not inserted into drive housing properly:
Loosen gun securing bolt and push gun end into housing just enough so that it does
not touch wire feed mechanism.
Damaged liner:
Have a qualified technician inspect and repair/replace as necessary.
1.
2.
3.
4.
Welding arc not stable
POSSIBLE CAUSES AND SOLUTIONS
Wire not feeding properly:
See first Troubleshooting section above.
Incorrect contact tip size:
Replace with the proper tip for the wire size used.
Incorrect wire feed speed:
Adjust wire feed speed to achieve a more stable arc.
Loose torch cable or ground cable:
Check to ensure that all connections are tight.
Damaged torch or loose connection within torch:
Have a qualified technician inspect and repair/replace as necessary.
1.
2.
3.
4.
5.