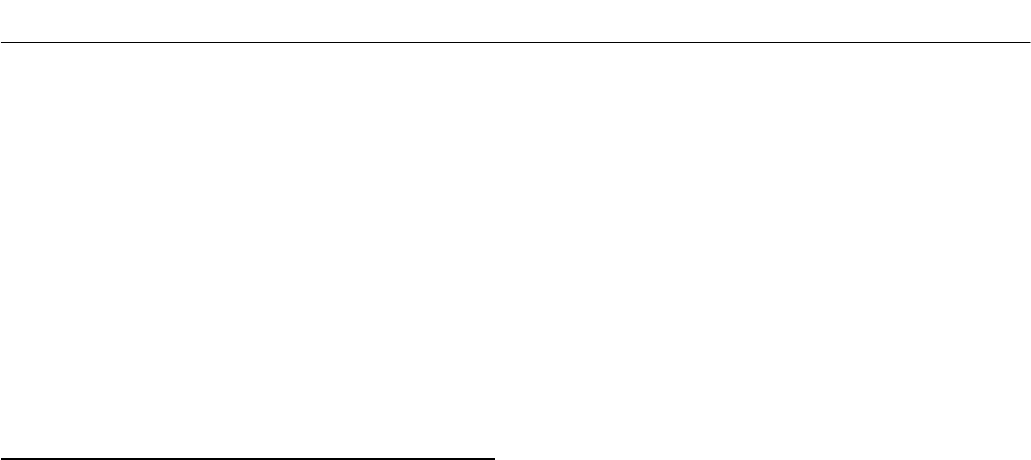
31OPERATING INSTRUCTIONS – INTELLISYS OPTION
SSR UP6 40, SSR UP6 50PE, SSR UP6 50PEI, HF50–PE,
EP50–PE, HP50–PE, HXP50–PE
27 POWER L.E.D.
This will illuminate when the 8V controller supply is available.
28 AUTOMATIC RESTART L.E.D.
This will illuminate when the machine has shutdown due to low air
demand. The compressor will restart and load automatically as soon
as the demand for air resumes.
DISPLAY MESSAGES
When the compressor is running normally, the display will indicate
the package discharge pressure and illuminate the corresponding
L.E.D. [1]. An arrow will also appear in the far right of the display
indicating pressure band selection. Pressing display select [19] will
change the display value and the corresponding L.E.D. will illuminate.
The controller monitors all aspects of the compressor while running and
will display warnings or in severe conditions execute an emergency
stop and display alarm conditions.
MACHINE CONTROL MODES
CAPACITY CONTROL
The compressor is designed to work with two types of capacity
control, to suit the individual plant requirements. These controls are:–
A. On line – Off line. (Fitted as standard)
B. On line – Off line, with Upper Range Modulation. (Optional extra)
Either is available by selection at the control panel.
ON LINE – OFF LINE CONTROL
For applications that require a widely varying air demand, this mode
of control will deliver air at full capacity or zero capacity with low
receiver pressure.
This mode of operation is controlled by the pressure transducer
responding to changes in plant air pressure. This sensor energizes
the load solenoid valve which in turn operates the venting valve
(blowdown) and the closing of the atmospheric vent opening in the
air inlet valve.
The compressor then delivers full capacity air to the plant system.
If the air pressure in this system rises to the upper set point of the
pressure setting, the load solenoid valve is de–energized allowing the
inlet valve to close. At the same time, the venting valve opens allowing
the receiver pressure to drop.
The pressure setting has a range of 12 psi (0.83 bar) between its
upper and lower set points.The upper set point is set at 3 psi (0.2 bar)
above the compressor rated discharge pressure.
UPPER RANGE MODULATION CONTROL (Optional Extra)
For plants having a relatively high and constant air demand, Upper
Range Modulation is the recommended mode of control.
Upper range modulation retains the features of On line – Off line
control but provides the throttling of the inlet air flow as the line pressure
rises to the upper set point of the off–line pressure setting.
By bleeding off a small amount from the regulator valve, which
energises the Modulate Solenoid Valve, a reduction in the air signal to
the pneumatic cylinder on the inlet valve allows the cylinder to ‘trim’ the
inlet valve position as dictated by changing line pressure. Modulation
begins when the compressor reaches about 94% of the rated line
pressure and is factory set to modulate down to approximately 70% of
rated capacity.
If the air demand decreases to a level below the 70% modulated
output, the line pressure will increase slightly to the upper limit of the
pressure setting, when the compressor then changes to the Off line
control position and operates with the receiver vented.
CONTROLLER WARNING MESSAGES
In the event of a warning, the controller will display a message and
the alarm L.E.D. [10] will flash. The warning message will alternate with
the normal display every 4 seconds, the compressor will continue to run
but the fault should be rectified as soon as possible. The arrow keys
[23] should be used to index the display for any additional warning
messages. A warning message may be reset by depressing set [21]
once.
NOTE:
The warning will recur if the fault has not been rectified. The
following warning messages may be displayed:
COOLANT FILTER (OPTIONAL)
The pressure differential across the coolant filter exceeds 15 psi (1
bar)
.
AIR FILTER
The air filter is dirty or blocked and should be replaced.
SEPARATOR ELEMENT
The separator element is dirty or blocked and should be replaced.
AIREND TEMPERATURE
The airend temperature reaches 97% of the high airend
temperature set point (i.e. 223°F (106°C)).
CONTROLLER ALARMS
In the event of an alarm, the controller will execute an emergency
stop, the alarm L.E.D. [10] will illuminate and an alarm message will be
displayed. The arrow keys [23] should be used to index the display for
any additional alarm messages. An alarm is reset by depressing set
[21] twice within a 3 second period after the fault has been rectified. The
compressor will restart only when all alarm conditions have been
rectified. The following alarm messages may be displayed (For fault
correction see the Fault Finding section):
STARTER FAULT
The contactor sequence during start or stop is incorrect.
AIREND TEMPERATURE
The airend discharge temperature is above the high temperature
set point.
MOTOR OVERLOAD
The motor overload contacts are open. The motor overload must be
reset before the controller can be reset.
REVERSE ROTATION
No sump pressure is detected after the first 2 seconds of running.
Isolate the machine and reverse the mains supply connections before
resuming.
OVER PRESSURE
The line pressure is 15 psi (1 bar) greater than the rated discharge
pressure.
TEMPERATURE SENSOR 1
The airend temperature sensor/ connecting cable has failed.
TEMPERATURE SENSOR 2
The separator tank temperature sensor/connecting cable has
failed.
PRESSURE SENSOR
Indicates pressure transducer failure / connecting cable fault.
http://air.ingersollrand.com