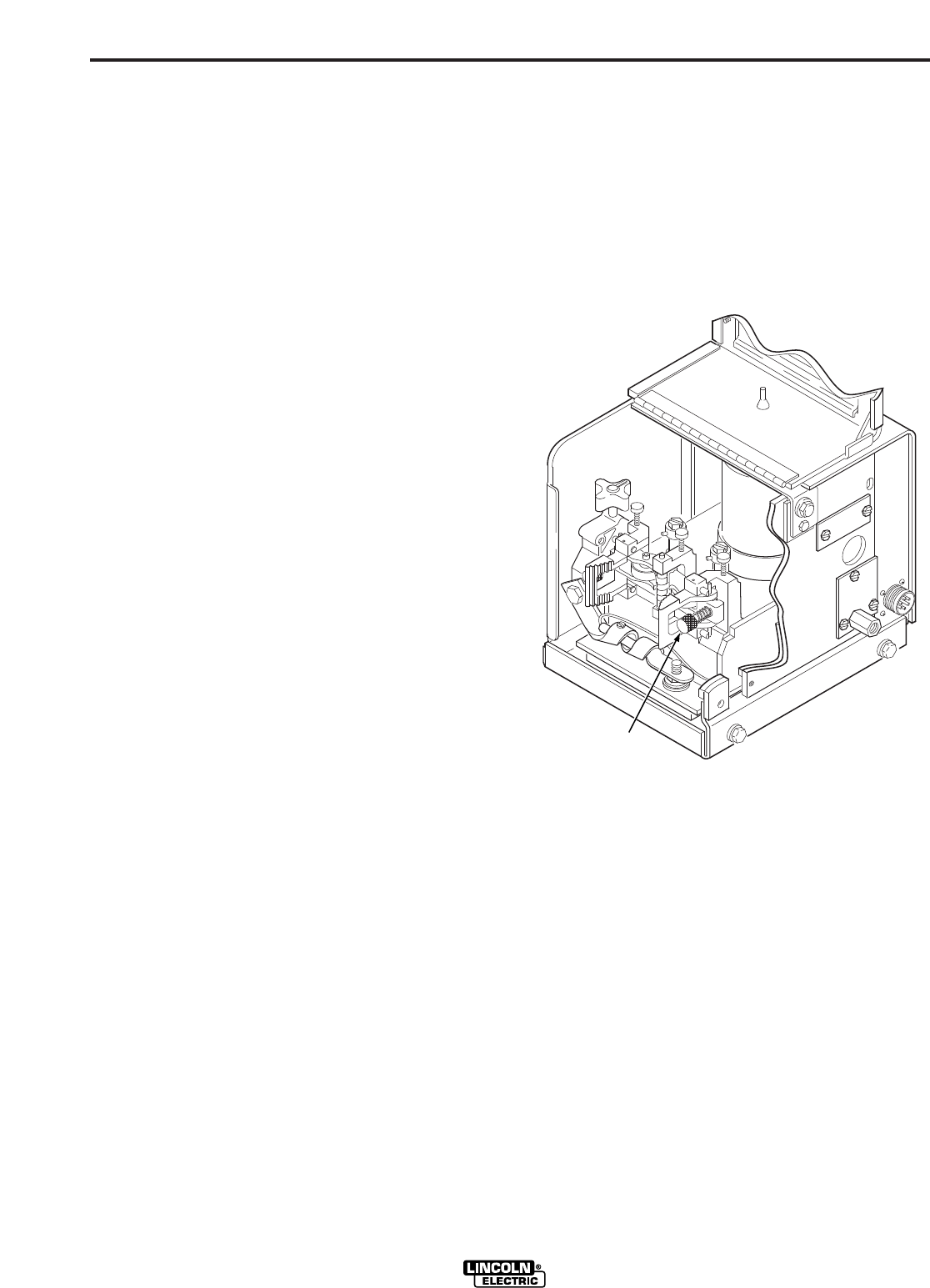
B-7
OPERATION
B-7
IDLE ROLL PRESSURE SETTING
The idle roll pressure is set at the factory. Two-roll
feeders are set with the pressure adjustment knob
backed out two turns from full pressure, and four-roll
feeders are set backed out three turns. This is an
approximate setting. For small wire sizes and
aluminum wire the optimum idle roll pressure varies
with type of wire, surface condition, lubrication, and
hardness. The optimum idle roll setting can be
determined as follows:
Two-roll wire feeders:
1. Press the end of the gun against a solid object
that is electrically isolated from the welder output
and press the trigger for several seconds.
2. If the wire “birdnests”, jams, or breaks at the drive
roll, the idle roll pressure is set too high. Back the
pressure adjustment knob, Figure B.4, out 1/2
turn. Run new wire through the gun and repeat
step 1.
3. If the only result is drive roll slippage, loosen the
gun cable clamping screw on the conductor block
and pull the gun cable forward about six inches.
There should be a slight waviness in the exposed
wire. If there is no waviness, the pressure is too
low. Increase the pressure setting 1/4 turn. Lock
the gun cable in place and repeat steps 1 and 2.
Four-roll wire feeders:
1. Release the incoming idle roll and perform the
pressure setting procedure for two roll feeders to
set outgoing idle roll pressure.
2. After outgoing pressure is set, determine how
many turns away from full pressure the setting is.
3. Set both idle roll tensions to this setting. Engage
both idle rolls before welding. For most
applications, best wire feeding will occur when
both idle roll pressures are set the same.
FIGURE B.4 – IDLE ROLL PRESSURE SETTING.
LN-742 & LN-742H
PRESSURE
ADJUSTMENT
KNOB