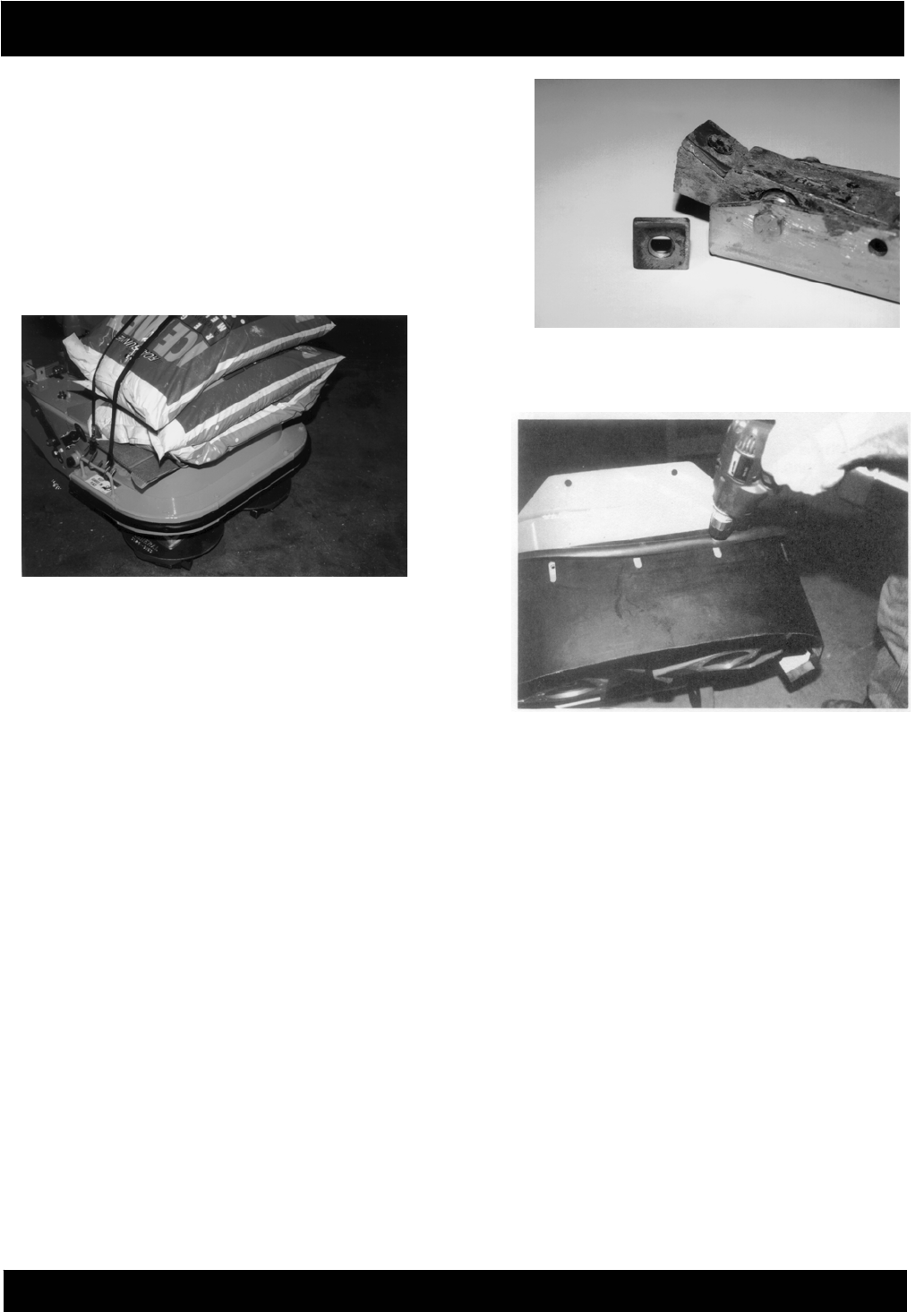
DFG-SERIES SURFACE GRINDERS OPERATION AND PARTS MANUAL REV #4 (05/28/09) PAGE 24
ASSEMBLY INSTRUCTIONS/OPERATIONS
of up to several hundred square feet per hour can be
realized. However, many thin film ( ie: 5 mill
thickness and thinner) urethane coatings present a
much more difficult removal problem. Since removal
rates are also directly affected by applied down
force, up to 300 lbs of external weight can be
applied to the SURFACE GRINDER to increase
productivity. Cement blocks or stacked bags of
cement make excellent weights and can be secured
with "bungy" cords or other means with the provided
holes in the top cover. FIGURE 17.
FIGURE 17
Each insert provides 8 scraping edges. As an edge
become dull and worn, the insert can be turned and
reinstalled to expose a new, sharp edge. FIGURE
18. When all 4 edges of one side become worn and
dull, the insert c
an be turned over to expose an
additional 4 edges.
Many materials such as adhesives, rubber deposits
and mastics have the tendency to extrude or smear
rather than shear from the concrete floor material.
The occurrence is also aggravated by higher
ambient temperatures. This problem can be
significantly reduced with the addition of various
amounts of water or a water saturated, fine sand
combination placed on the floor. The use of the
Safety and Dust Shield Assembly with the
SURFACE GRINDER is highly recommended to
contain the water/sand slurry mixture from damaging
surrounding walls and other vertic
al surfaces.
FIGURE 19.
FIGURE 18
FIGURE 19
To index the tungsten carbide insert, proceed as
follows:
Tools required:
1 each, 5/32 Allen wrench.
1) Clean the SCRAPE-R-TACH unit with a suitable
safety solvent to remove excess material build-
up. Remove as much foreign material from the
female hexagon socket area of the capscrew.
This will allow the wrench to make full contact
and maximize the torque transfer to the cap
screw.