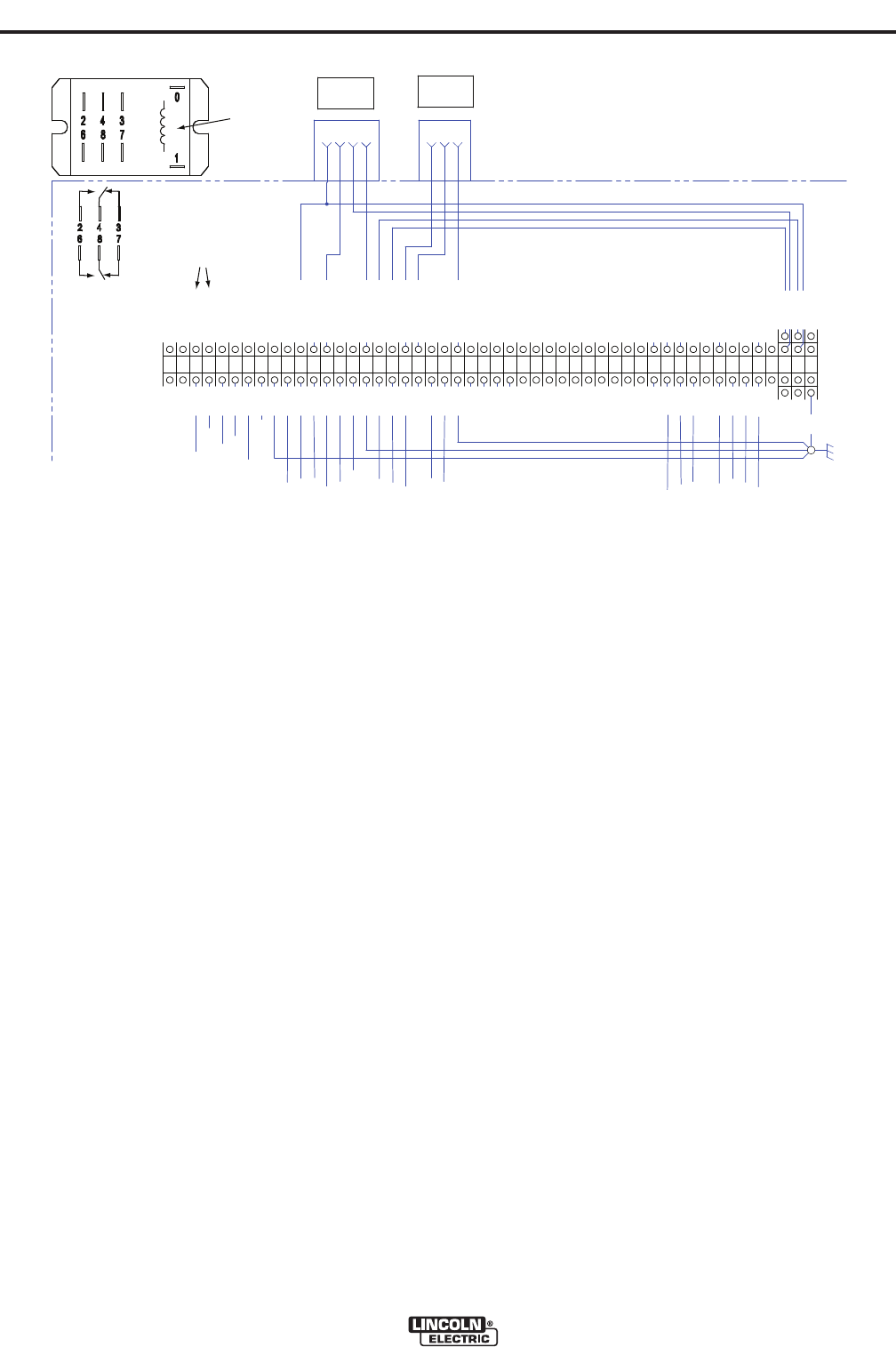
A-6
INSTALLATION
MAXsa™ 10 CONTROLLER
A-6
SWITCH GROUP #2 SUPPLY
3-PIN FLUX
RECEPTACLE
A
B
C
TERMINAL
S
TRIP
CR3 INPUT #8
852
855
858
859
CR3 NO #2
CR3 NO #6
CR3 NC #3
CR3 INPUT #4
CR1 INPUT #8
CR1 NO #2
CR1 NO #6
CR1 NC #3
FLUX GND
CR1 INPUT #4
CR3 NC #7
SHUTDOWN #2 SUPPLY
SHUTDOWN #1
SHUTDOWN #1 SUPPLY
532B-49
SWITCH GROUP #1 SUPPLY
START
FLUX FILL
GND IN
CR1 NC #7
TRAVEL #1 GND
531B-48
4-PIN TRAVEL
RECEPTACLE
A
B
C
D
CR2 INPUT #8
CR2 NO #2
CR2 NO #6
CR2 NC #3
CR2 INPUT #4
CR2 NC #7
TRAVEL #2 GND
GND
1
2
5
6
7
8
9
10
11
12
13
14
15
16
17
18
19
20
21
22
23
24
25
26
27
28
29
30
31
32
33
34
35
36
37
38
39
40
41
42
43
44
45
49
50
3
4
47
48
46
851
8510
859
CR1-4
CR1-8
CR1-2
CR1-6
CR1-3
CR1-7
GND-B
CR3-4
CR3-8
CR3-2
CR3-6
CR3-3
CR3-7
GND-A
CR2-4
CR2-8
CR2-2
CR2-6
CR2-3
CR2-7
531A-48
532A-49
GND-C
8511
SHUTDOWN #2
853
856
857
STOP
INCH FORWARD
INCH REVERSE
Numbers Refer to
Relay Terminals
CR1, CR2 CR3
Relays
CONTROLLING NON-LINCOLN AUXILIARY
EQUIPMENT
Custom motion control and/or other auxiliary equipment
can be powered using the terminal strip and relays. To
use non-Lincoln motion control and/or flux hoppers, fol-
low instructions below. See Figure A.4.
1. Remove all input power to the MAXsa™ 10 CON-
TROLLER including any auxiliary power supplies.
2. Remove the wire duct cover to gain access to the
leads on the right side of the terminal strip.
3. Remove a plug button from one of the .875” (22.2mm)
access holes on the bottom of the MAXsa™ 10 CON-
TROLLER control box. Install a suitable strain relief to
protect the leads. See Figure A.1.
4. Remove the leads going from the terminal strip to the
corresponding connectors, i.e. terminal strip blocks
#11, #13, and #16 for the 4-pin TC-3 Travel Carriage
or terminal strip blocks #19, #20, and #23 for the 3-pin
Automatic Flux Hopper. See the Wiring Diagram.
5. These loose leads can be taped and secured in the
wire duct.
.
6. Any custom or non-Lincoln equipment can be powered
by the normally open contacts from relays CR1, CR2,
or CR3. The contacts for CR1 are connected to the
terminal strip blocks #3 through #8. The contacts for
CR2 are connected to terminal strip blocks #10
through #15. The contacts for CR3 are connected to
terminal strip blocks #17 through #22. See Figure A.3.
CR1 and CR2 relay coils are in parallel and are BOTH
turned ON and OFF as determined by the Travel Options
setting (P12 in the Set-up Menu) as long as the TRAVEL
MODE is set to AUTO. CR3 turns ON with the START
command and OFF with the STOP Command.
7. The supply voltage to power the devices is provided
by the end user. As shipped, the MAXsa™ 10 has the
auxiliary supply blocks (terminal strip blocks #48 and
#49) connected to the CR2 relay and CR3 relay
inputs, respectively. When the end user connects a
supply to the AUX blocks #48 and #49, this voltage will
be jumpered to the CR2 and CR3 relay inputs on ter-
minal strip blocks #11, #17, and #18.
NOTE: The CR1 relay is not connected to the AUX
terminal strip blocks; the customer must con-
nect power to this relay if it is to be used. See
relay ratings listed earlier.
8. Connect input supply voltage per the Auxiliary Input
Power Connection Instructions listed earlier.
9. The relays can also be used to provide contact closure
for any interfacing signals out using the normally open
contacts. An external auxiliary supply voltage would
not be necessary to use the relays as hard contact clo-
sure out signals.
NOTE: The CR1 relay as shipped does not have AUX
leads connected to it. This relay operates as
described above and has two normally open /
normally closed contacts that could be used as
a signal out when interfacing to PLC’s or cus-
tom controls.
FIGURE A.4 - CONTROLLING NON-LINCOLN EQUIPMENT