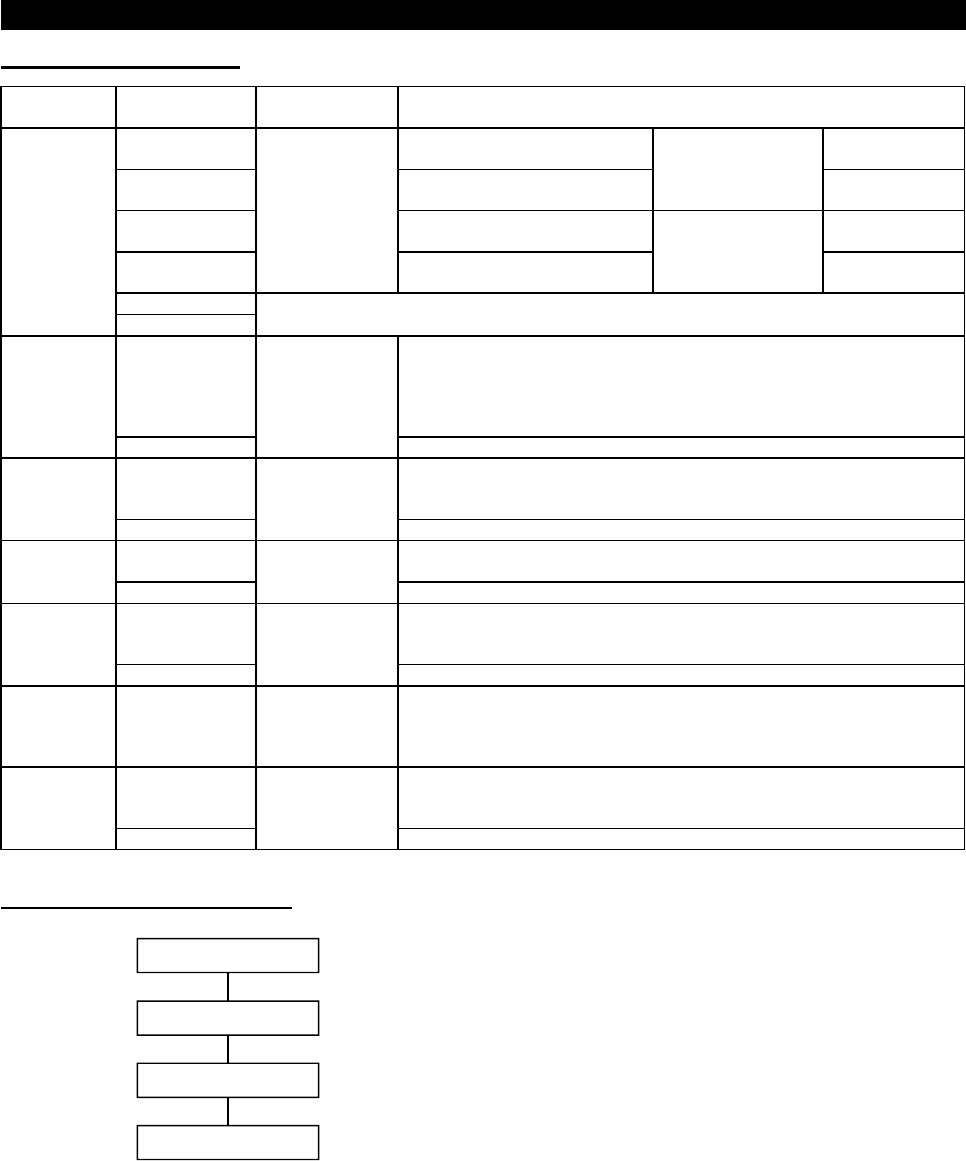
PARAMETERS
124
(5) Parameter setting
Parameter
Number
Setting Name Description
10
For heating, pressure control,
etc.
PID reverse
action
11 For cooling, etc.
Deviation value
signal input
(terminal 1)
PID forward
action
20
For heating, pressure control,
etc.
PID reverse
action
21
PID action
selection
For cooling, etc.
Set point (terminal 2
or Pr. 133), Process
value input, (terminal
4)
PID forward
action
30
128
31
Advanced PID control (NA, EC versions only)
0.1 to 1000%
If the proportional band is narrow (parameter setting is small), the
manipulated variable varies greatly with a slight change of the process value.
Hence, as the proportional band narrows, the response sensitivity (gain)
improves but the stability deteriorates, e.g. hunting occurs.
Gain K = 1/proportional band.
129
9999
PID proportional
band
No proportional control
0.1 to 3600 s
Time only required for the integral (I) action to provide the same manipulated
variable as that for the proportional (P) action. As the integral time
decreases, the set point is reached earlier but hunting occurs more easily.
130
9999
PID integral time
No integral control.
0 to 100%
Set the upper limit. If the feedback value exceeds the setting, the FUP signal
is output. (Process value of 4mA is equivalent to 0% and 20mA to 100%.)
131
9999
Upper limit
No function
0 to 100%
Set the lower limit. If the feedback value falls below the setting, the FDN
signal is output. (Process value of 4mA is equivalent to 0% and 20mA to
100%.)
132
9999
Lower limit
No function
133 0 to 100%
PID action set
point for PU
operation
Only valid for the PU command in the PU operation or PU/external combined
mode.
For external operation, the voltage across 2-5 is the set point.
(Pr. 902 value is equivalent to 0% and Pr. 903 value to 100%.)
0.01 to 10.00 s
Time only required for the differential (D) action to provide the same process
value as that for the proportional (P) action. As the differential time
increases, greater response is made to the deviation change.
134
9999
PID differential
time
No differential control.
(
6
)
Adjustment procedure
Set the I/O terminals for PID control. (Pr. 180 to Pr. 186, Pr. 190 to Pr.195)
Pr. 128 = 10, 11, 20, 21
Parameter setting
Terminal setting
Switch X14 signal on.
Run
Adjust the PID control parameters, Pr. 128 to Pr. 134