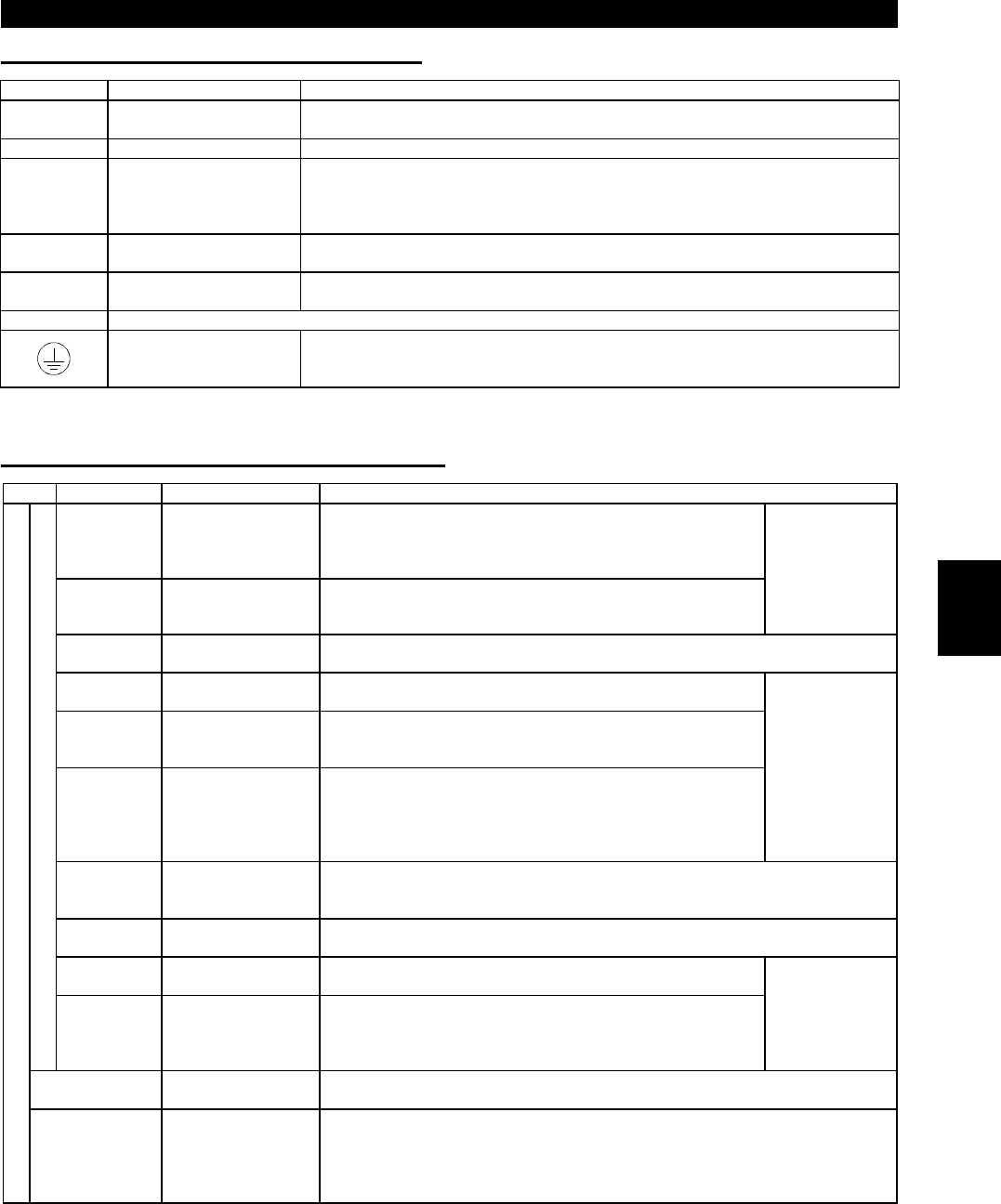
INSTALLATION AND WIRING
10
(
1
)
Description of main circuit terminals
Symbol Terminal Name Description
R, S, T
〈
L
1
, L
2
, L
3
〉
AC power input
Connect to the commercial power supply. Keep these terminals unconnected when
using the high power factor converter (FR-HC).
U, V, W Inverter output Connect a three-phase squirrel-cage motor.
R1, S1
〈
L
11
, L
21
〉
Power supply for control
circuit
Connected to the AC power supply terminals R and S
〈
L
1
and L
2
〉
. To retain the alarm
display and alarm output or when using the high power factor converter (FR-HC),
remove the jumpers from terminals R-R1 and S-S1
〈
L
1
-L
11
and L
2
-L
21
〉
and apply
external power to these terminals.
P, N
〈
+, -
〉
Brake unit connection
Connect the optional FR-BU brake unit, power regeneration converter (FR-RC) or high
power factor converter (FR-HC).
P, P1
〈
+, P1
〉
Power factor improving
DC reactor connection
Disconnect the jumper from terminals P-P1
〈+
-P1
〉
and connect the optional power
factor improving reactor (FR-BEL).
PR, PX Please do not alter or adjust terminals PR and PX of the connecting jumper.
Ground For grounding the inverter chassis. Must be earthed.
Note:
〈
〉
Terminal names in parentheses are those of the EC version.
(
2
)
Description of control circuit terminals
Type Symbol Terminal Name Description
STF Forward rotation start
Turn on the STF signal to start forward rotation and turn it off to
stop. Acts as a programmed operation start signal in the
programmed operation mode. (Turn on to start and turn off to
stop.)
STR Reverse rotation start
Turn on the STR signal to start reverse rotation and turn it off to
stop.
When the STF
and STR signals
are turned on
simultaneously,
the stop
command is
given.
STOP
Start self-holding
selection
Turn on the STOP signal to select the self-holding of the start signal.
RH, RM, RL Multi-speed selection
Use the RH, RM and RL signals as appropriate to select multiple
speeds.
JOG JOG mode selection
Turn on the JOG signal to select jog operation (factory setting).
Jog operation can be performed with the start signal (STF or
STR).
RT
Second acceleration/
deceleration time
selection
Turn on the RT signal to select the second acceleration/
deceleration time. When the second functions such as "second
torque boost" and "second V/F (base frequency)" functions have
been set, these functions can also be selected by turning on the
RT signal.
Input terminal
function selection
(Pr. 180 to
Pr. 186) change
terminal
functions.
MRS Output stop
Turn on the MRS signal (20ms or longer) to stop the inverter output.
Used to shut off the inverter output to bring the motor to a stop by the magnetic
brake.
RES Reset
Used to reset the protective circuit activated. Turn on the RES signal for more than
0.1 second, then turn it off.
AU
Current input
selection
Only when the AU signal is turned on, the inverter can be
operated with the 4-20mADC frequency setting signal.
Contact input
CS
Automatic restart after
instantaneous power
failure selection
With the CS signal on, restart can be made automatically when
the power is restored after an instantaneous power failure. Note
that this operation requires restart parameters to be set. When
the inverter is shipped from the factory, it is set to disallow restart.
Input terminal
function selection
(Pr. 180 to
Pr. 186) change
terminal
functions.
SD
Contact input
common (sink)
Common to the contact input terminals and terminal FM. Common output terminal for
24VDC 0.1A power (PC terminal).
Input signals
PC
24VDC power and
external transistor
common
Contact input
common (source)
When transistor output (open collector output), such as a programmable controller, is
connected, connect the external power supply common for transistor output to this
terminal to prevent a fault caused by undesirable current. This terminal can be used
as a 24VDC, 0.1A power output. When source logic has been selected, this terminal
serves as a contact input common.
2