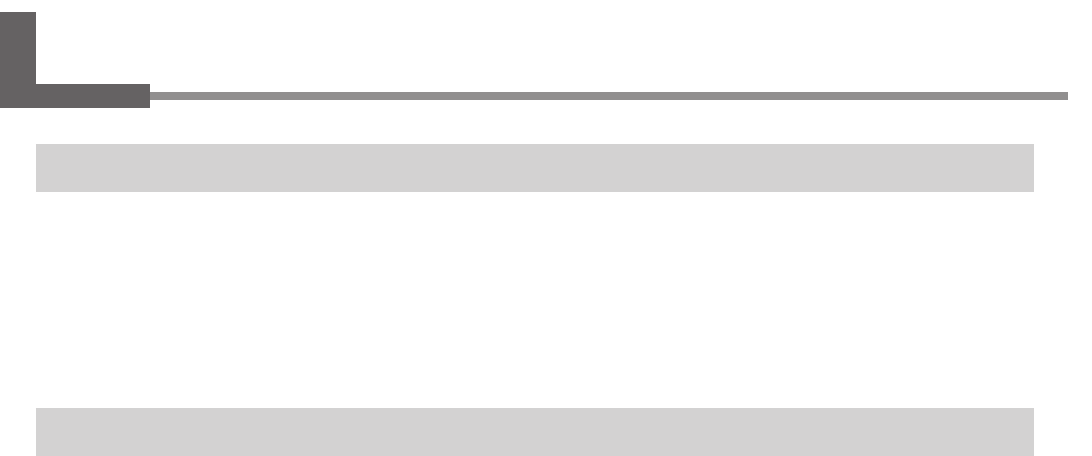
135
Chapter 9 - Appendix
9-2. The Nose Unit
Considerations for Fluctuations in Workpiece Thickness
When you're using a character cutter, it is important to keep the cutting-in depth uniform. Changes in the cutting-in depth
alter the line width, affecting the appearance. Materials such as acrylic panels may exhibit variations in thickness or
slight curvature. You cannot obtain a uniform cutting-in depth when you engrave these as they are.
When you use the machine's nose unit, the nose tracks the surface of the workpiece and makes it possible to perform
engraving at a constant depth at all times without having to give special consideration to variations in thickness.
Structure of the Nose Unit
You loosen the lock nut for the spindle when using the nose unit. Loosening the lock nut puts the spindle in a floating
state, allowing the entire spindle to move up and down freely. In this state, the nose is pressed against the surface of the
workpiece and the spindle is maintained at a constant height from the workpiece surface.
The cutting-in depth is determined mechanically by the amount of extension of the cutter from the nose tip. It is impor-
tant to note that it is not determined by the vertical movement of the spindle effected by the Z-axis drive motor. The
vertical motion due to the Z-axis drive motor is performed simply to press the nose against the workpiece.
The amount of pressure of the nose against the workpiece is determined automatically (when [AUTO Z CONTROL]
function is [ON]), and there is no need to set this expressly. The machine detects when the nose tip touches the workpiece
and automatically moves the spindle up or down by a suitable distance.