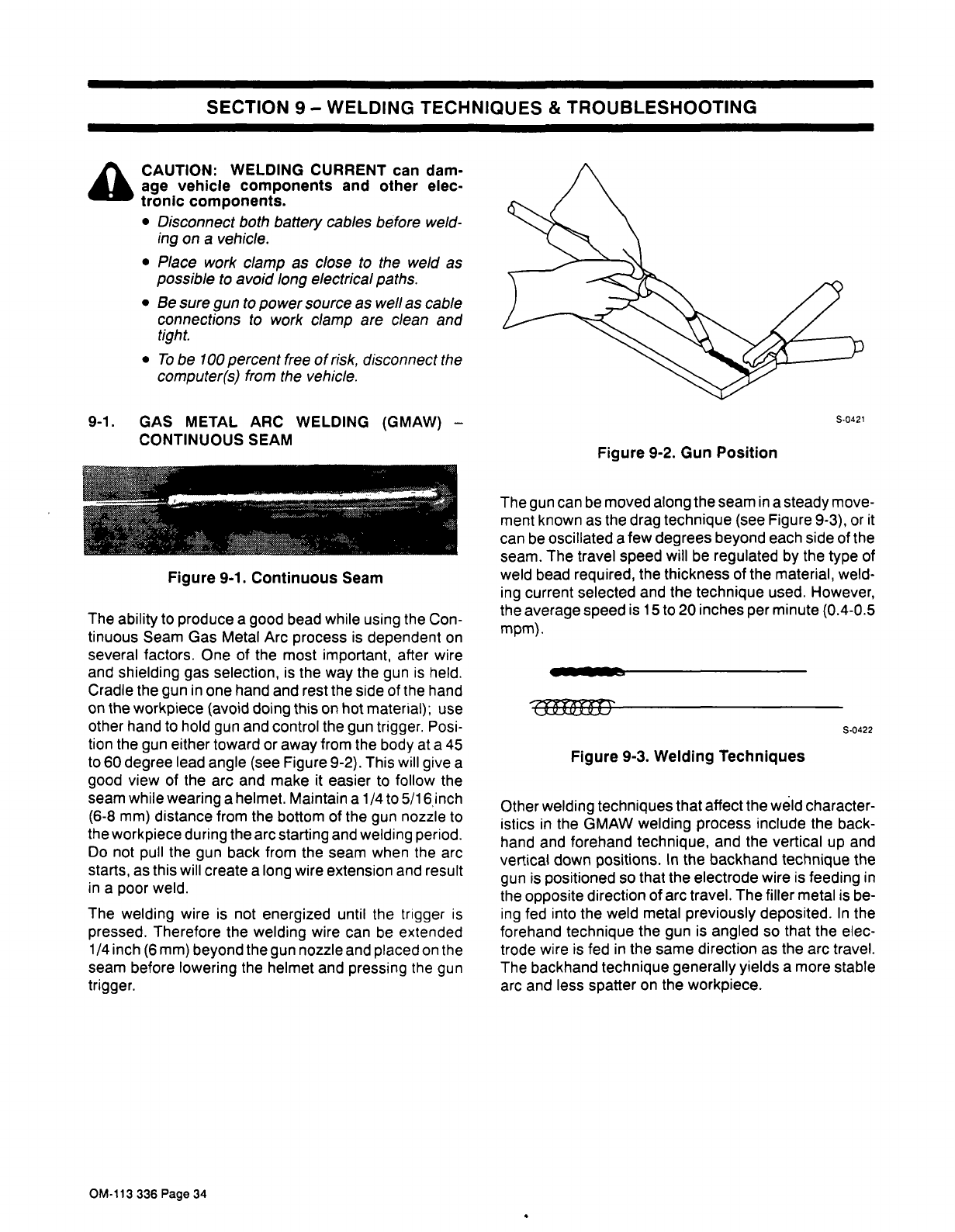
SECTION
9
WELDING
TECHNIQUES
&
TROUBLESHOOTING
a
CAUTION:
WELDING
CURRENT
can
dam
age
vehicle
components
and
other
elec
tronic
components.
Disconnect
both
battery
cables
before
weld
ing
on
a
vehicle.
Place
work
clamp
as
close
to
the
weld
as
possible
to
avoid
long
electrical
paths.
Be
sure
gun
to
power
source
as
well
as
cable
connections
to
work
clamp
are
clean
and
tight.
To
be
100
percent
free
of
risk,
disconnect
the
computer(s)
from
the
vehicle.
The
ability
to
produce
a
good
bead
while
using
the
Con
tinuous
Seam
Gas
Metal
Arc
process
is
dependent
on
several
factors.
One
of
the
most
important,
after
wire
and
shielding
gas
selection,
is
the
way
the
gun
is
held.
Cradle
the
gun
in
one
hand
and
rest
the
side
of
the
hand
on
the
workpiece
(avoid
doing
this
on
hot
material);
use
other
hand
to
hold
gun
and
control
the
gun
trigger.
Posi
tion
the
gun
either
toward
or
away
from
the
body
at
a
45
to
60
degree
lead
angle
(see
Figure
9-2).
This
will
give
a
good
view
of
the
arc
and
make
it
easier
to
follow
the
seam
while
wearing
a
helmet.
Maintain
a
1/4
to
5/1
6inch
(6-8
mm)
distance
from
the
bottom
of
the
gun
nozzle
to
theworkpieceduringthearcstartingandwelding
period.
Do
not
pull
the
gun
back
from
the
seam
when
the
arc
starts,
as
this
will
create
a
long
wire
extension
and
result
in
a
poor
weld.
The
welding
wire
is
not
energized
until
the
trigger
is
pressed.
Therefore
the
welding
wire
can
be
extended
1/4
inch
(6mm)
beyond
the
gun
nozzle
and
placed
on
the
seam
before
lowering
the
helmet
and
pressing
the
gun
trigger.
The
gun
can
be
moved
along
the
seam
in
a
steady
move
ment
known
as
the
drag
technique
(see
Figure
9-3),
or
it
can
be
oscillated
a
few
degrees
beyond
each
side
of
the
seam.
The
travel
speed
will
be
regulated
by
the
type
of
weld
bead
required,
the
thickness
of
the
material,
weld
ing
current
selected
and
the
technique
used.
However,
the
average
speed
is
15
to
20
inches
per
minute
(0.4-0.5
mpm).
rn~r
Figure
9-3.
Welding
Techniques
Other
welding
techniques
that
affect
the
weld
character
istics
iii
the
GMAW
welding
process
include
the
back
hand
and
forehand
technique,
and
the
vertical
up
and
vertical
down
positions.
In
the
backhand
technique
the
gun
is
positioned
so
that
the
electrode
wire
is
feeding
in
the
opposite
direction
of
arc
travel.
The
filler
metal
is
be
ing
fed
into
the
weld
metal
previously
deposited.
In
the
forehand
technique
the
gun
is
angled
so
that
the
elec
trode
wire
is
fed
in
the
same
direction
as
the
arc
travel.
The
backhand
technique
generally
yields
a
more
stable
arc
and
less
spatter
on
the
workpiece.
9-1.
GAS
METAL
ARC
WELDING
(GMAW)
-
CONTINUOUS
SEAM
S-
04
2
1
Figure
9-2.
Gun
Position
Figure
9-1.
Continuous
Seam
S.0422
OM-113
336
Page
34