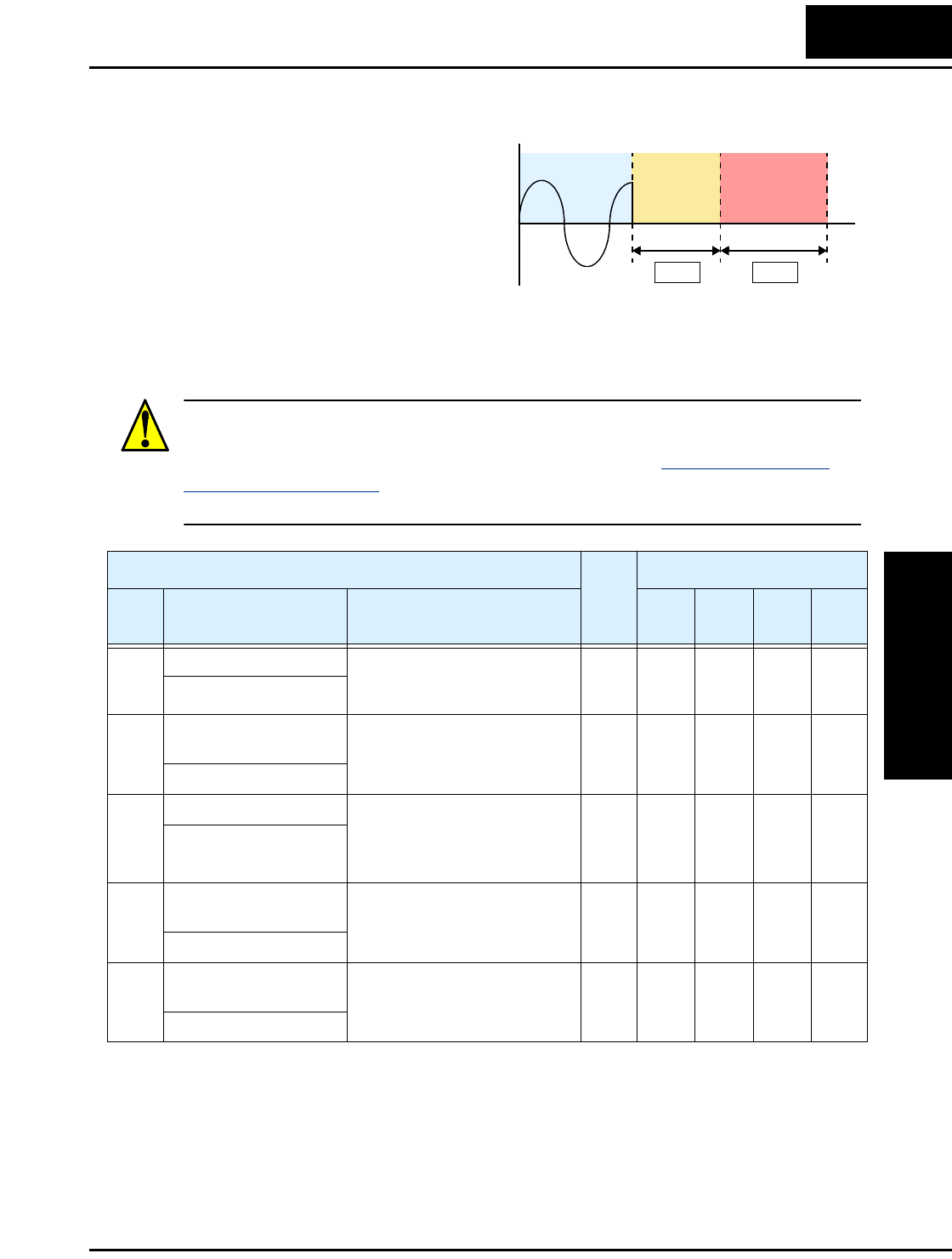
L100 Inverter
Configuring
Drive Parameters
3–15
DC Braking Settings
The DC braking feature can provide
additional stopping torque when
compared to a normal deceleration to a
stop. DC braking is particularly useful
at low speeds when normal decelera-
tion torque is minimal. When you
enable DC braking, the inverter injects
a DC voltage into the motor windings
during deceleration below a frequency you can specify (A_52). The braking power
(A_54) and duration (A_55) can both be set. You can optionally specify a wait time
before DC braking (A_53), during which the motor will free run (coast).
CAUTION: Be careful to avoid specifying a braking time that is long enough to cause
motor overheating. If you use DC braking, we recommend using a motor with a built-in
thermistor, and wiring it to the inverter’s thermistor input (see “
Thermistor Thermal
Protection” on page 4–20). Also refer to the motor manufacturer’s specifications for
duty-cycle recommendations during DC braking.
DC brakingFree runRunning
A53 A55
t
0
+
–
“A” Function
Run
Mode
Edit
Defaults
Func.
Code
Name /
SRW Display
Description
–FE
(CE)
–FU
(UL)
–FR
(Jpn)
Units
A_51 DC braking enable Two options; select codes:
00 ...Disable
01 ...Enable
✘ 00 00 00 —
DCB SW OFF
A_52 DC braking frequency
setting
The frequency at which DC
braking occurs,
range is 0.5 to 10 Hz
✘ 0.5 0.5 0.5 Hz
DCB F 00.5Hz
A_53 DC braking wait time The delay from the end of Run
command to start of DC
braking (motor free runs until
DC braking begins)
✘ 0.0 0.0 0.0 sec.
DCB WAIT 0.0s
A_54 DC braking during
deceleration
Applied level of DC braking
force, settable from 0 to 100%
✘ 000%
DCB V 000
A_55 DC braking time for
deceleration
Sets the duration for DC
braking, range is 0.1 to 60.0
seconds
✘ 0.0 0.0 0.0 sec.
DCB T 00.0s