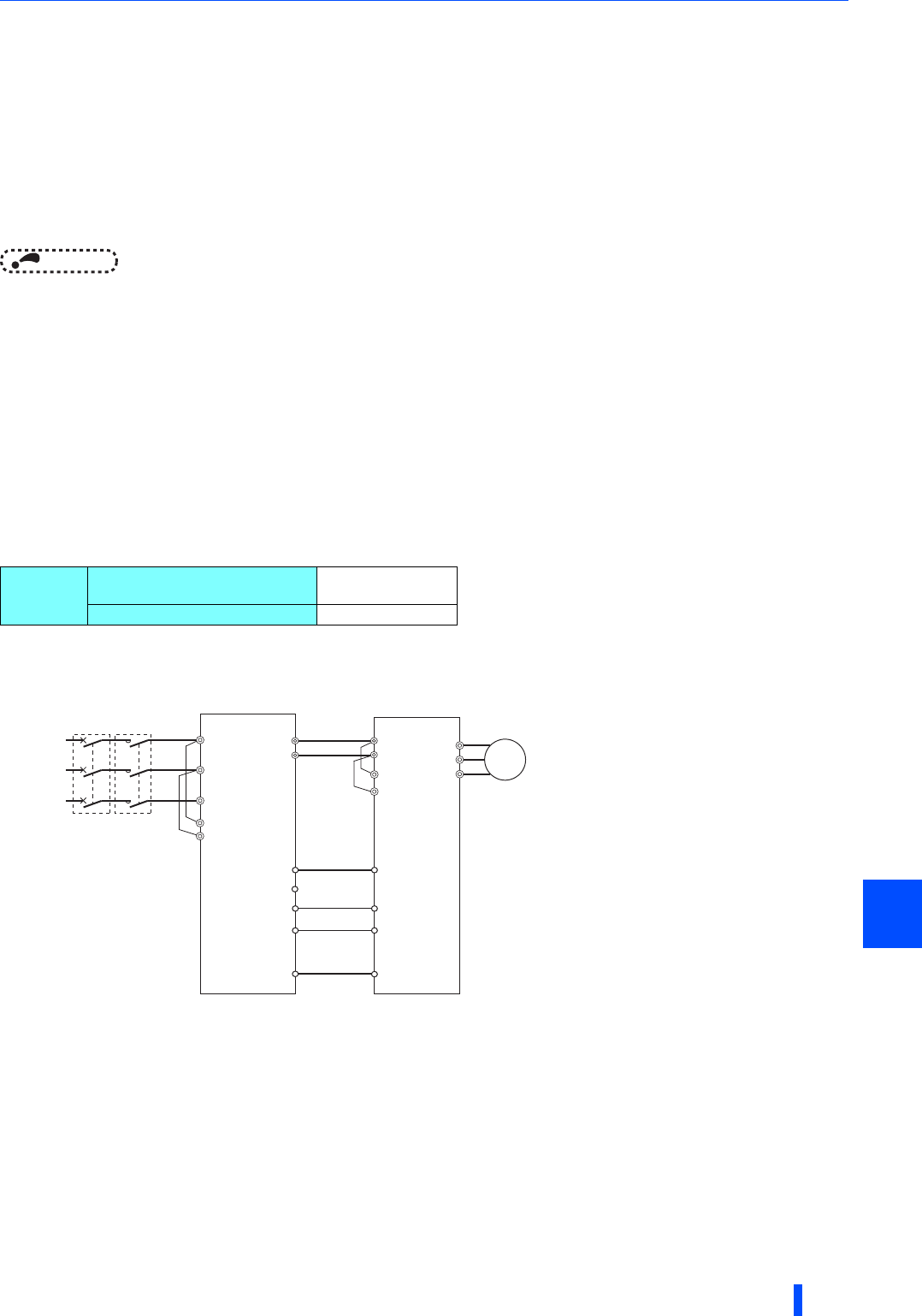
Terminal connection diagrams
INSTALLATION AND WIRING
27
2
The terminals R1/L11 and S1/L21 are connected to the terminals P/+ and N/- with a jumper respectively. When using separate power supply for
the control circuit, remove the jumpers from R1/L11 and S1/L21.
The function of these terminals can be changed with the input terminal assignment (Pr.178 to Pr.189).
Terminal JOG is also used as the pulse train input terminal. Use Pr.291 to choose JOG or pulse.
The X10 signal (NC contact input specification) is assigned to the terminal MRS in the initial setting. Set Pr.599 = "0" to change the input
specification of the X10 signal to NO contact.
Terminal input specifications can be changed by analog input specification switchover (Pr.73, Pr.267). To input a voltage (0 to 5 V/0 to 10 V), set
the voltage/current input switch OFF. To input a current (4 to 20 mA), set the voltage/current input switch ON. Terminals 10 and 2 are also used
as a PTC input terminal. (Pr.561)
It is recommended to use 2 W 1 k when the frequency setting signal is changed frequently.
The function of these terminals can be changed with the output terminal assignment (Pr.195, Pr.196).
The function of these terminals can be changed with the output terminal assignment (Pr.190 to Pr.194).
No function is assigned in the initial setting. Use Pr.192 for function assignment.
NOTE
• To prevent a malfunction due to noise, keep the signal cables 10 cm or more away from the power cables. Also, separate the
main circuit cables at the input side from the main circuit cables at the output side.
• After wiring, wire offcuts must not be left in the inverter.
Wire offcuts can cause an alarm, failure or malfunction. Always keep the inverter clean.
When drilling mounting holes in an enclosure etc., take caution not to allow chips and other foreign matter to enter the
inverter.
• Set the voltage/current input switch correctly. Incorrect setting may cause a fault, failure or malfunction.
Connection between the converter unit and the inverter
Perform wiring so that the commands sent from the converter unit are transmitted to the inverter without fail. Incorrect
connection may damage the converter unit and the inverter.
For the wiring length, refer to the table below.
For the cable gauge of the cable across the main circuit terminals P/+ and N/- (P and P, N and N), refer to page 30.
Do not install an MCCB across the terminals P/+ and N/- (across terminals P and P/+ or across N and N/-). Connecting the opposite polarity of
terminals N/- and P/+ will damage the inverter.
For the terminal used for the X10 signal input, set "10" in any of Pr.178 to Pr.189 (input terminal function selection) to assign the function.
(The X10 signal is assigned to the terminal MRS in the initial setting.)
For the X10 signal, NC contact input specification is selected in the initial setting. Set Pr.599 = "0" to change the input specification to NO
contact.
For the terminal used for the X11 signal input, set "11" in any of Pr.178 to Pr.189 (input terminal function selection) to assign the function. For
RS-485 or any other communication where the start command is only transmitted once, use the X11 signal to save the operation mode at the
time of an instantaneous power failure.
Always connect the terminal RDA of the converter unit and the terminal MRS (X10) of the inverter, and the terminal SE of the converter unit and
the terminal SD (sink logic) of the inverter. Not connecting these terminals may damage the converter unit.
Total wiring
length
Across the terminals P and P and
the terminals N and N
50 m or lower
Other control signal cables 30 m or lower
Inverter
Converter unit
(FR-CC2)
M
R1/L11
S1/L21
R/L1
S/L2
T/L3
Power
supply
MCCB
MC
U
V
W
R1/L11
S1/L21
P/+P/+
N/-
N/-
X11
RES
SD
IPF
RSO
SE
MRS(X10)
RDA
RDB