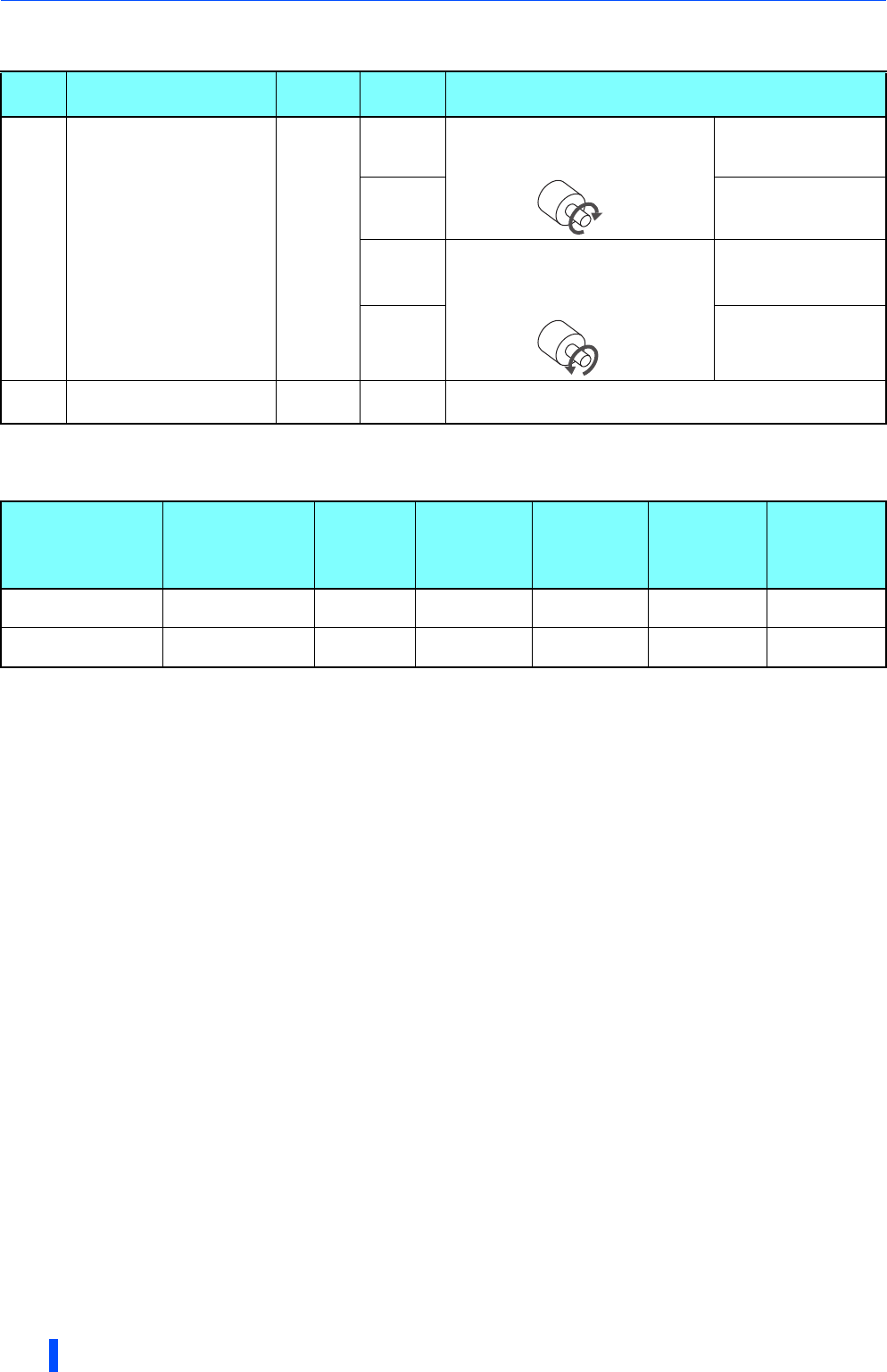
Connection of motor with encoder (vector control)
56
INSTALLATION AND WIRING
Parameter for the encoder (Pr.359, Pr.369)
Parameter settings for the motor under vector control
Pr. Name
Initial
value
Setting
range
Description
359
C141
Encoder rotation
direction
1
0
Set when using a motor for which
forward rotation (encoder) is clockwise
(CW) viewed from the shaft.
Set for the operation at
120 Hz or less.
100
Set for the operation at a
frequency higher than
120 Hz.
1
Set when using a motor for which
forward rotation (encoder) is
counterclockwise (CCW) viewed from
the shaft.
Set for the operation at
120 Hz or less.
101
Set for the operation at a
frequency higher than
120 Hz.
369
C140
Number of encoder
pulses
1024 0 to 4096
Set the number of encoder pulses output.
Set the number of pulses before it is multiplied by 4.
The above parameters can be set when the FR-A8AP (option) is mounted.
Motor name
Pr.9
Electronic
thermal O/L relay
Pr.71
Applied
motor
Pr.80
Motor
capacity
Pr.81
Number of
motor poles
Pr.359
Encoder
rotation
direction
Pr.369
Number of
encoder
pulses
Standard motor Rated motor current 0 (3) Motor capacity
Number of
motor poles
Constant-torque motor Rated motor current 1 (13) Motor capacity
Number of
motor poles
Offline auto tuning is required (Refer to the FR-A800 Instruction Manual (Detailed))
Set this parameter according to the motor.
CW
CCW